Boost your packaging efficiency with the XINTU Drop Load Case Packer.
Designed for versatile applications, it seamlessly handles beverages, edible oils, daily chemicals, and other light industrial products.
Capable of packing 600-800 cases per hour, it supports customized carton sizes with top open carton types.
Key features include automatic product arrangement, carton opening and positioning, compact design for space efficiency, and easy fault detection via a touch screen. With PLC control, touch screen interface, and manual/automatic modes, this machine ensures precise, reliable operation while minimizing downtime.
Main Features
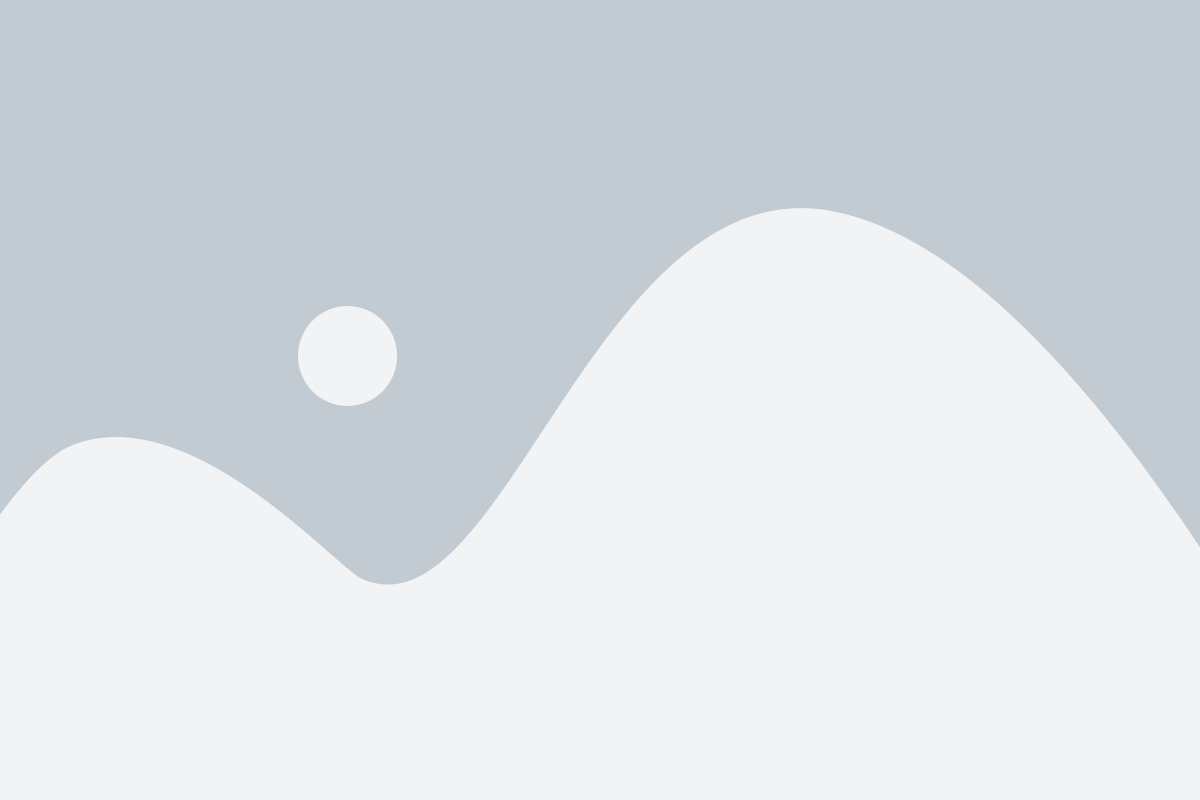
High-Speed Operation
Achieve up to 60 cases per minute. Maximize your production capacity with reliable and consistent performance.
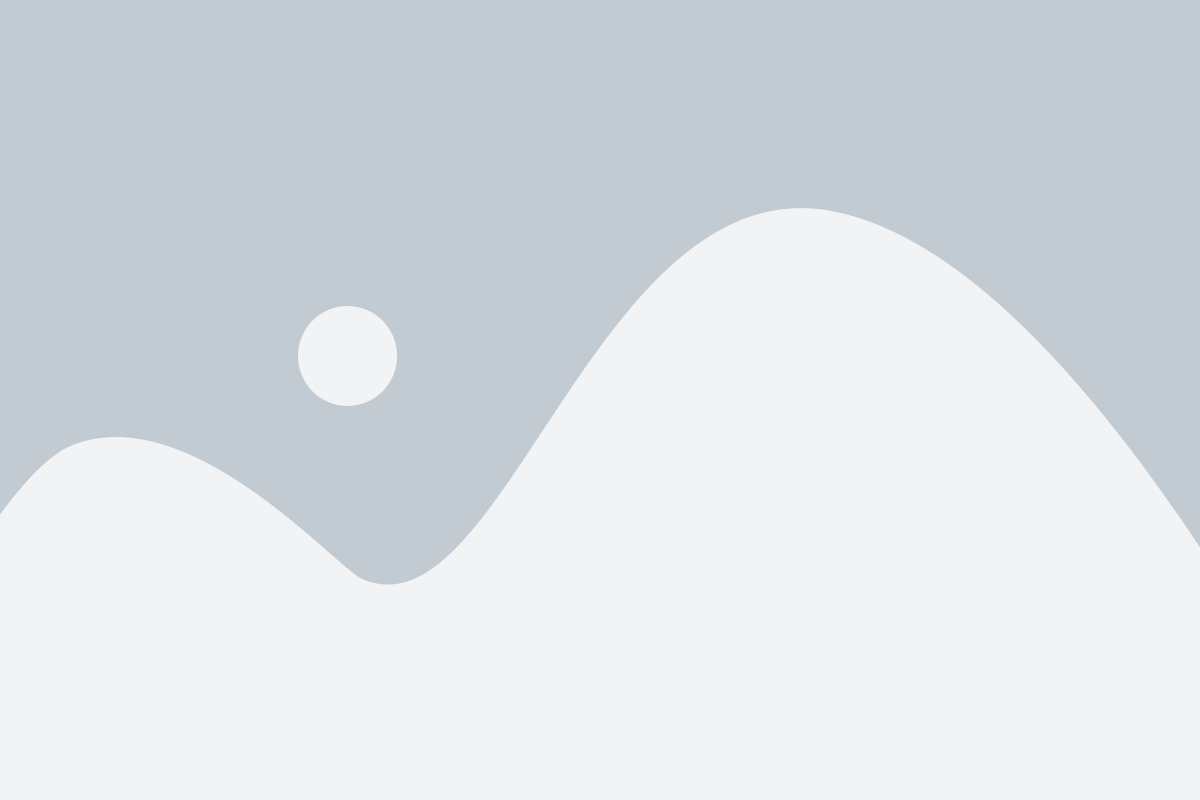
Versatile Packaging
Handle a variety of packaging forms including bottles, cans, and cartons. Adapt quickly to changing market demands with this flexible solution.
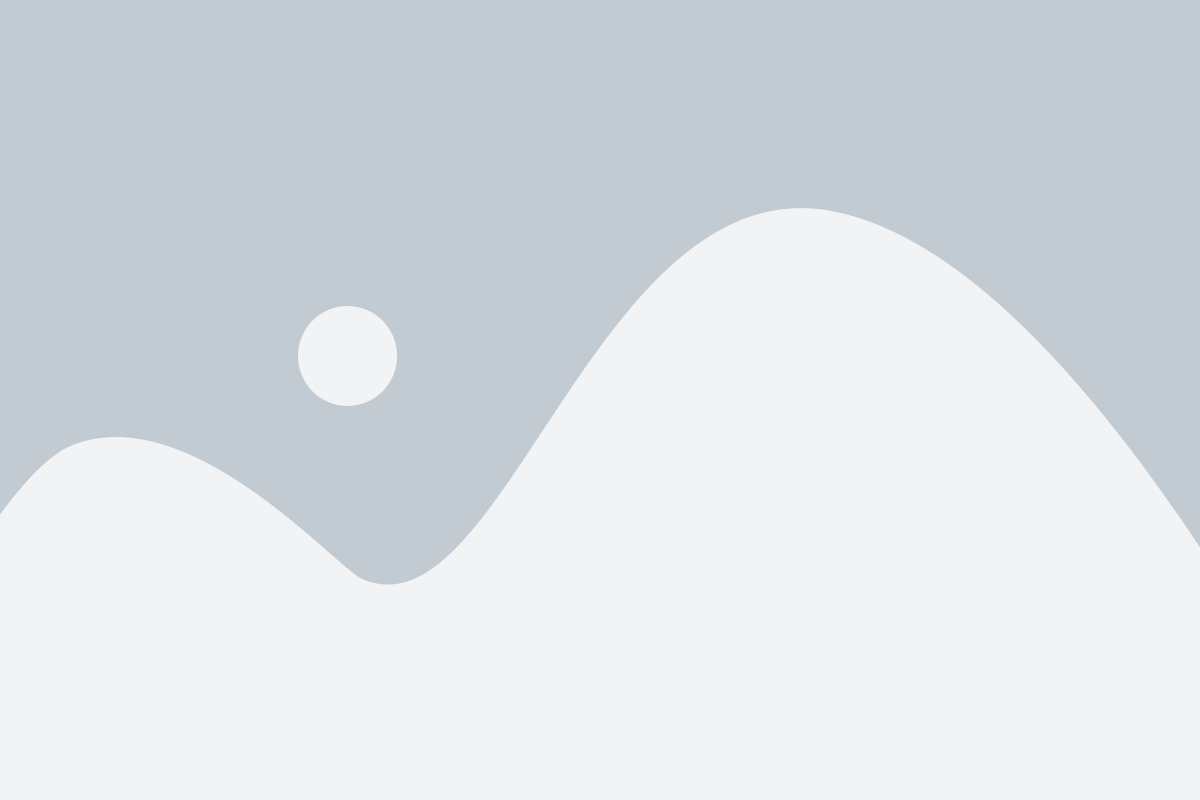
Seamless Integration
Easily incorporate into your existing production line. Enjoy hassle-free installation and minimal downtime, ensuring continuous operation.
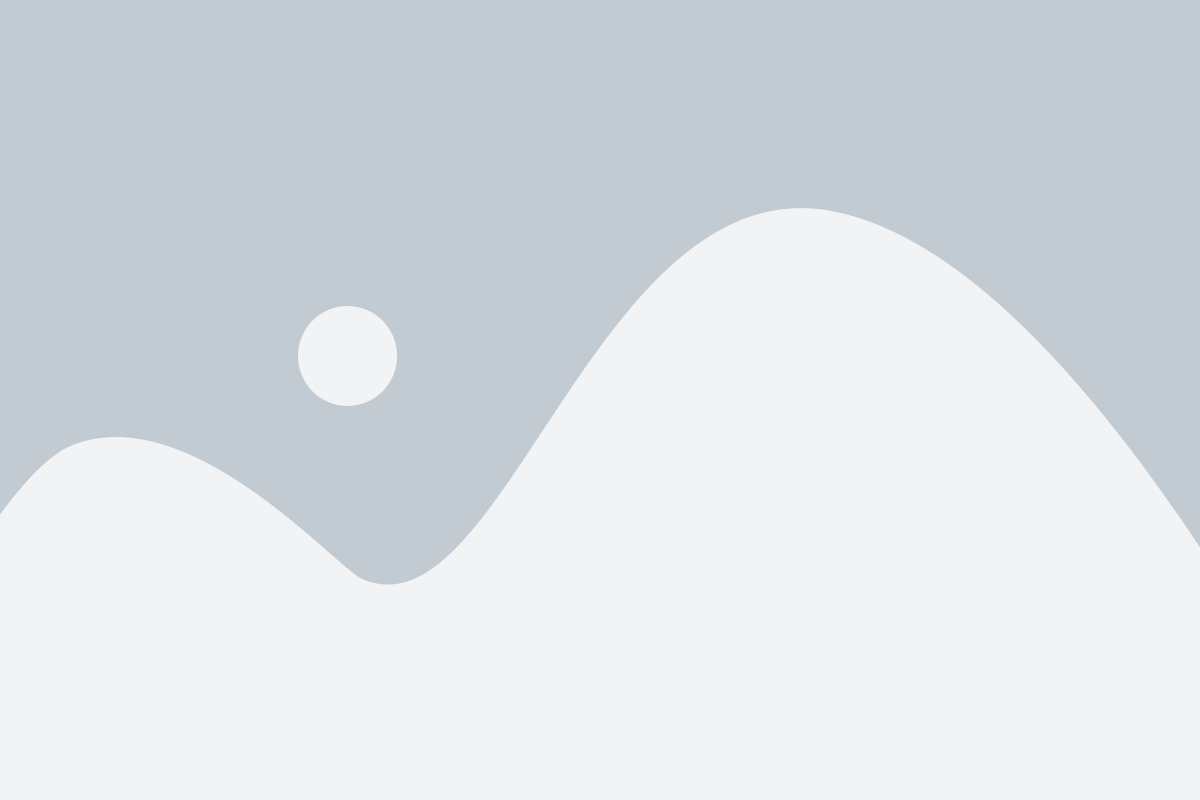
Advanced Automation
Reduce labor costs and human error with state-of-the-art automation. Benefit from precise control and monitoring, enhancing overall productivity.
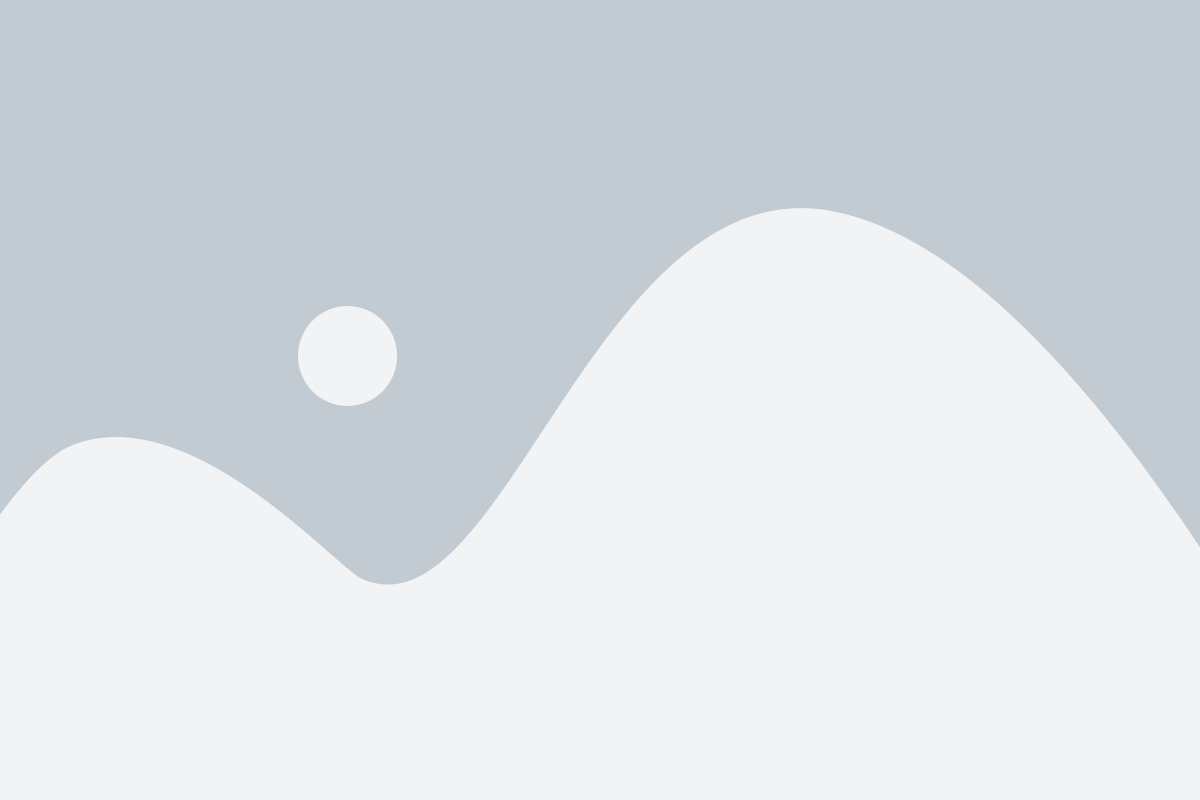
Compact Design
Optimize your workspace with our space-efficient design. Perfect for facilities with limited space, allowing you to maintain a streamlined and organized production area.
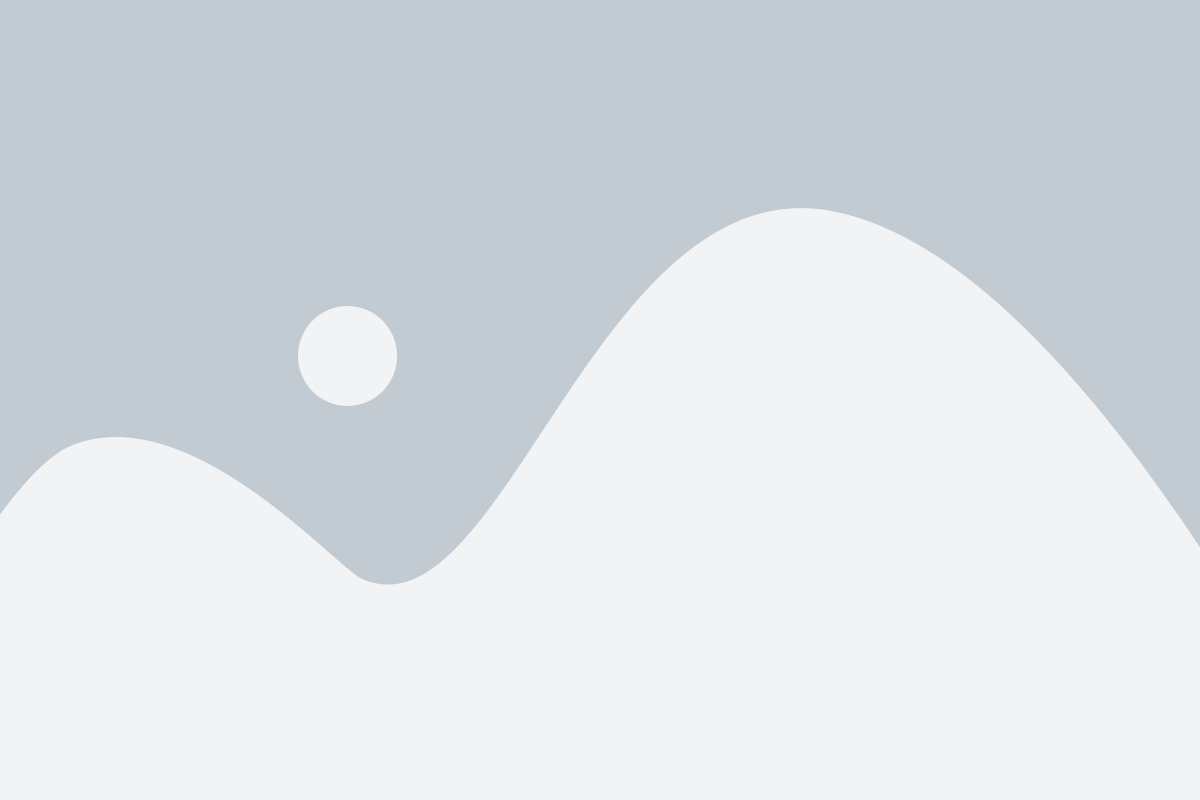
Robust Construction
Built for durability and long-term use. Experience reliable performance and reduced maintenance costs with our high-quality construction materials and engineering.
ADVANTAGES
Rapid Packaging
Up to 30 cases/min
Quick Changeover
Less than 10 minutes
Space Efficiency
Compact design saves 30% space
Cost Reduction
Cuts labor costs by 50%
SPECIFICATION
Speed
Up to 10-15 cases per minute
Up to 600-900 cases per hour
Packaging speed vary according to number of drop filling stations.
Case sizes
Can be customized
Operation
Drop down
Changeover
- Change grippers or fixtures: Adapt grippers for different products.
- Adjust guides and dividers: Modify guide positions for product sizes.
- Update programming settings: Adjust parameters via software.
Construction
Stainless Steel
Aluminum Alloy
Control Method
PLC + touch screen + standard control buttons + signal switch, automatic / manual control modes optional
Power Supply
380V/50Hz or 60Hz(Customized to the industrial voltage of the customer’s plant)
Air Supply
Approx. 5-6kg/㎠ 460L/min
Package Support
Bottles, Cans, and Boxed goods
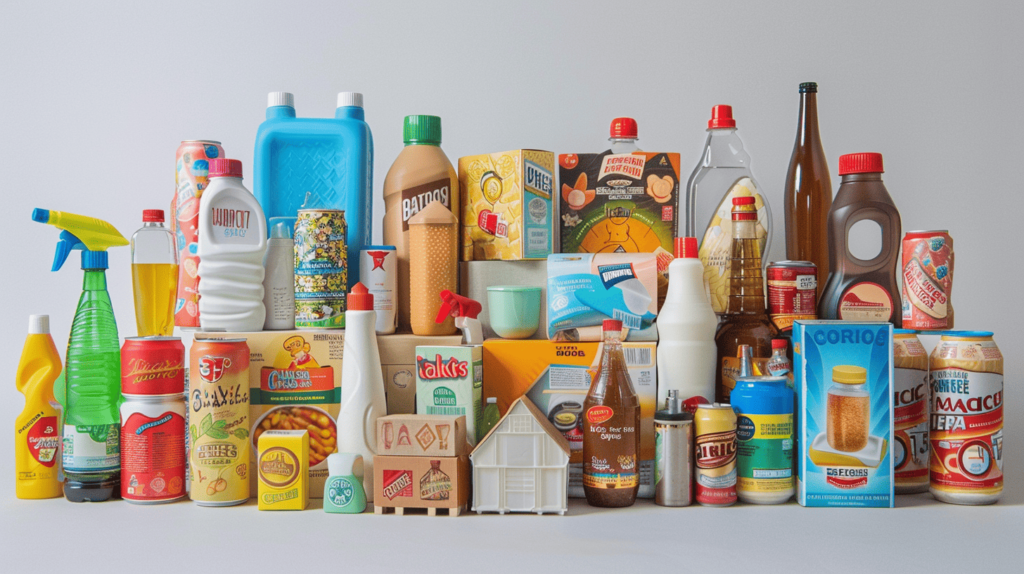
Case Support
Regular Slotted Cartons(RSC)/Windowed Box/Display Box/Double Wall Box/Mailer Box/Telescope Box/Display carton
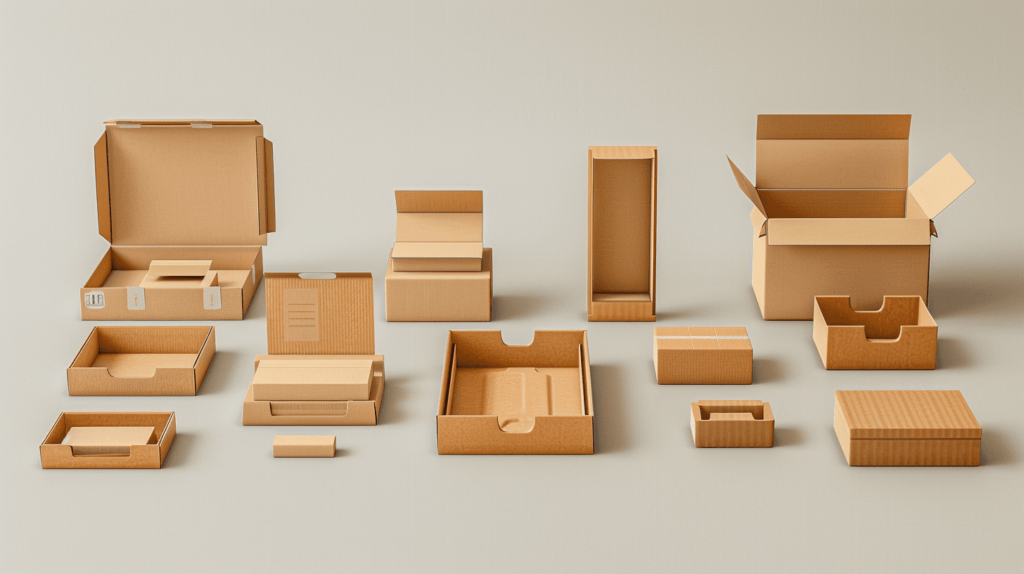
VIDEOS
Drop Load Case Packer For Bottled drinks
Incredible Speed: Imagine packing 20 bottles into a case in just 3 seconds. With our Drop Load Case Packer, you can significantly ramp up your packaging speed to 20-30 cases per minute. Ideal for bottled drinks, it serves the beverage, food, cosmetics, and household products industries, ensuring efficient and reliable operation to meet your demanding production schedules.
Drop Load Case Packer For bagged food
Boost your efficiency with our Drop Load Case Packer for bagged food. Packing 10-25 cartons per minute, it’s perfect for the food industry, handling products like snacks, grains, and powders. This versatile machine ensures rapid, reliable packaging, meeting your high-demand production needs effortlessly.
Top Load Case Packer For bottled liquor
Enhance your production line with our Drop Load Case Packer for bottled liquor, packing 10-25 cartons per minute. Designed for the beverage industry, it handles various bottle sizes and shapes, ensuring consistent, high-volume packaging. Ideal for liquor, wine, and spirits, this machine guarantees efficient, reliable operation to meet your demanding production schedules.
LAYOUT DRAWINGS
Explore our extensive range of Packaging layout solutions tailored for your project needs.
RELATED EQUIPMENT
Integrated packaging line solutions
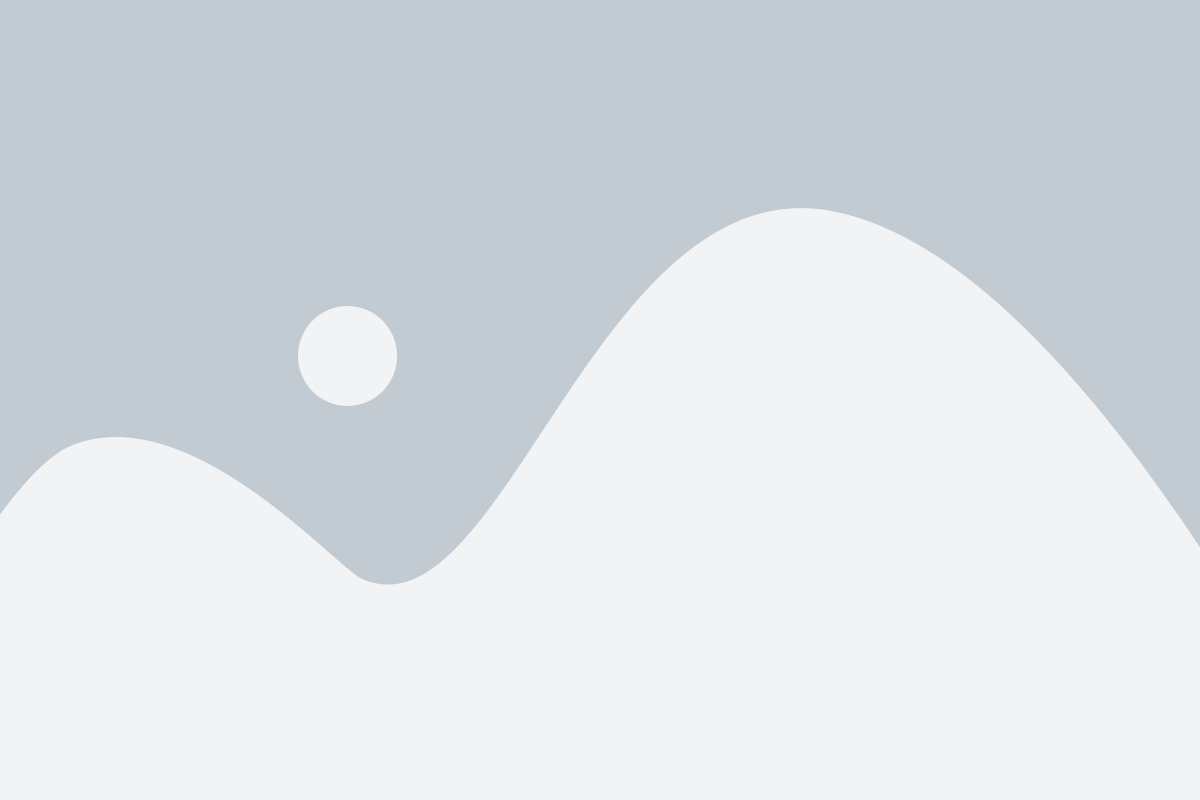
Add Your Heading Text Here
Lorem ipsum dolor sit amet, consectetur adipiscing elit. Ut elit tellus, luctus nec ullamcorper mattis, pulvinar dapibus leo.
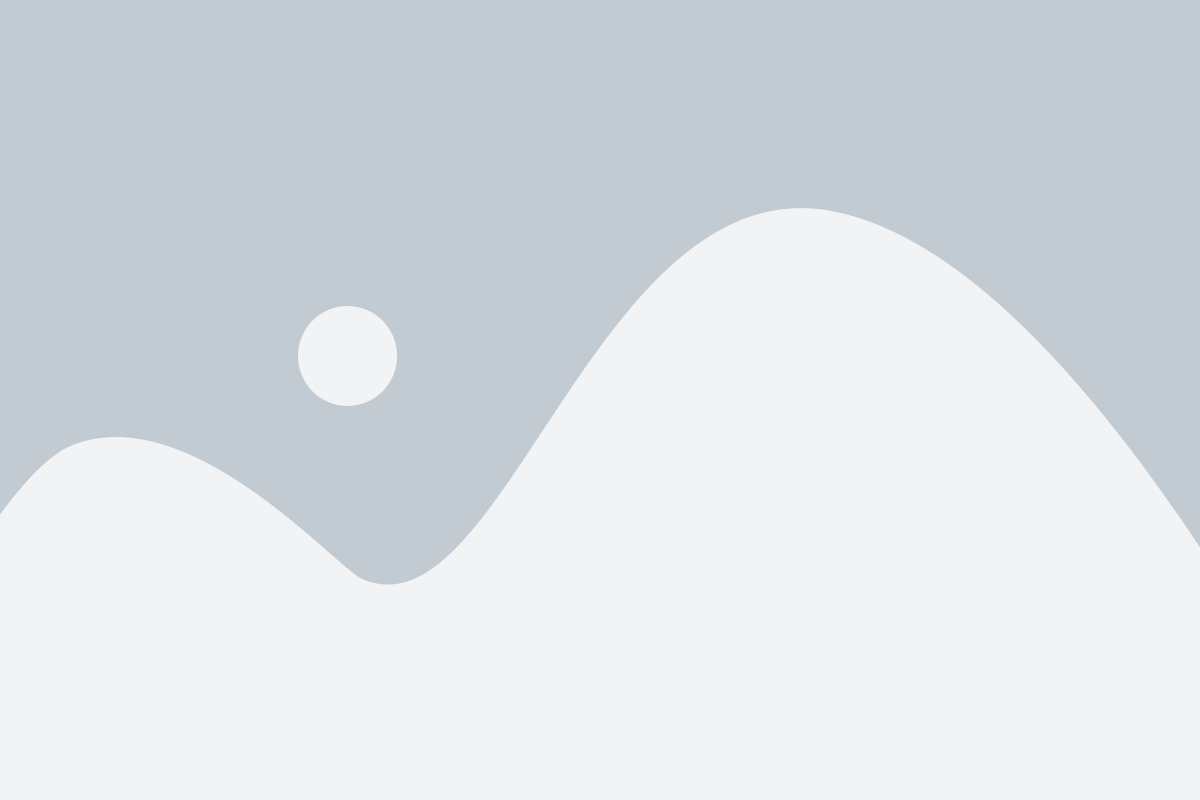
Add Your Heading Text Here
Lorem ipsum dolor sit amet, consectetur adipiscing elit. Ut elit tellus, luctus nec ullamcorper mattis, pulvinar dapibus leo.
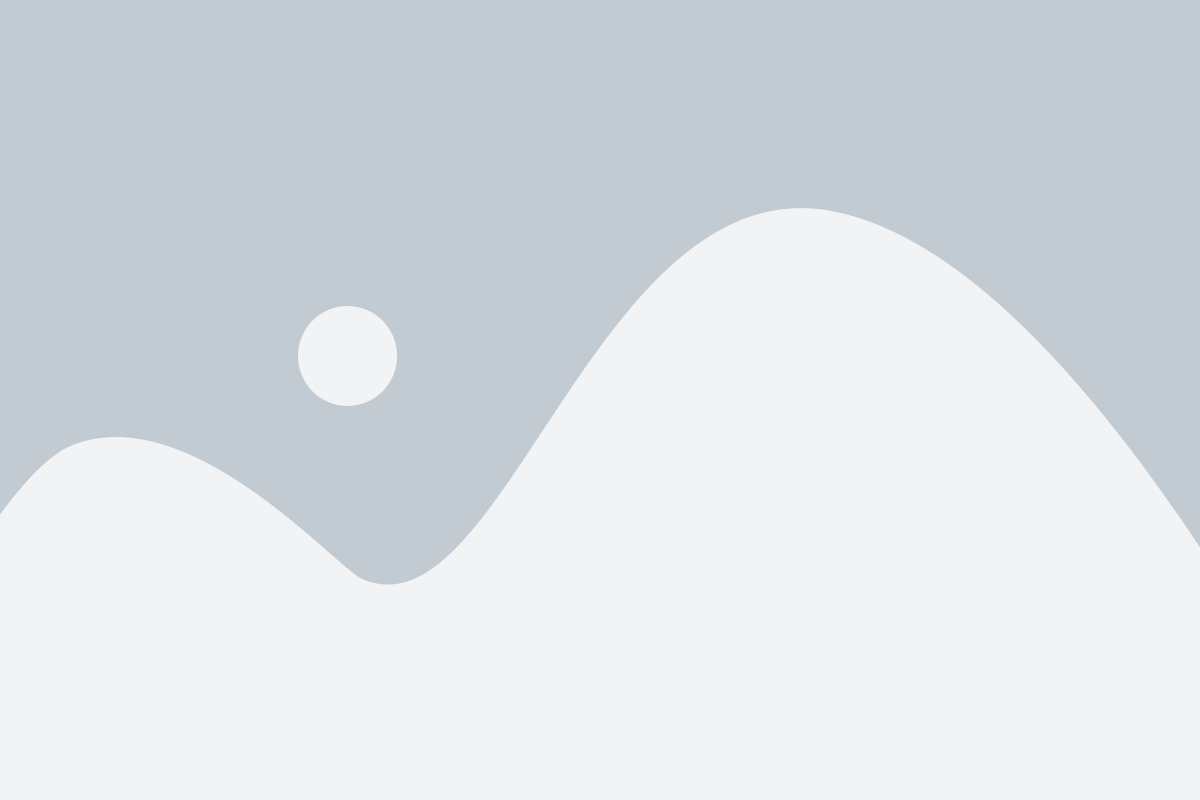
Add Your Heading Text Here
Lorem ipsum dolor sit amet, consectetur adipiscing elit. Ut elit tellus, luctus nec ullamcorper mattis, pulvinar dapibus leo.
FAQ
Listed below are the types of technical questions you may have about XINTU Drop case packers.
Working Principles of XINTU Drop Load Case Packer
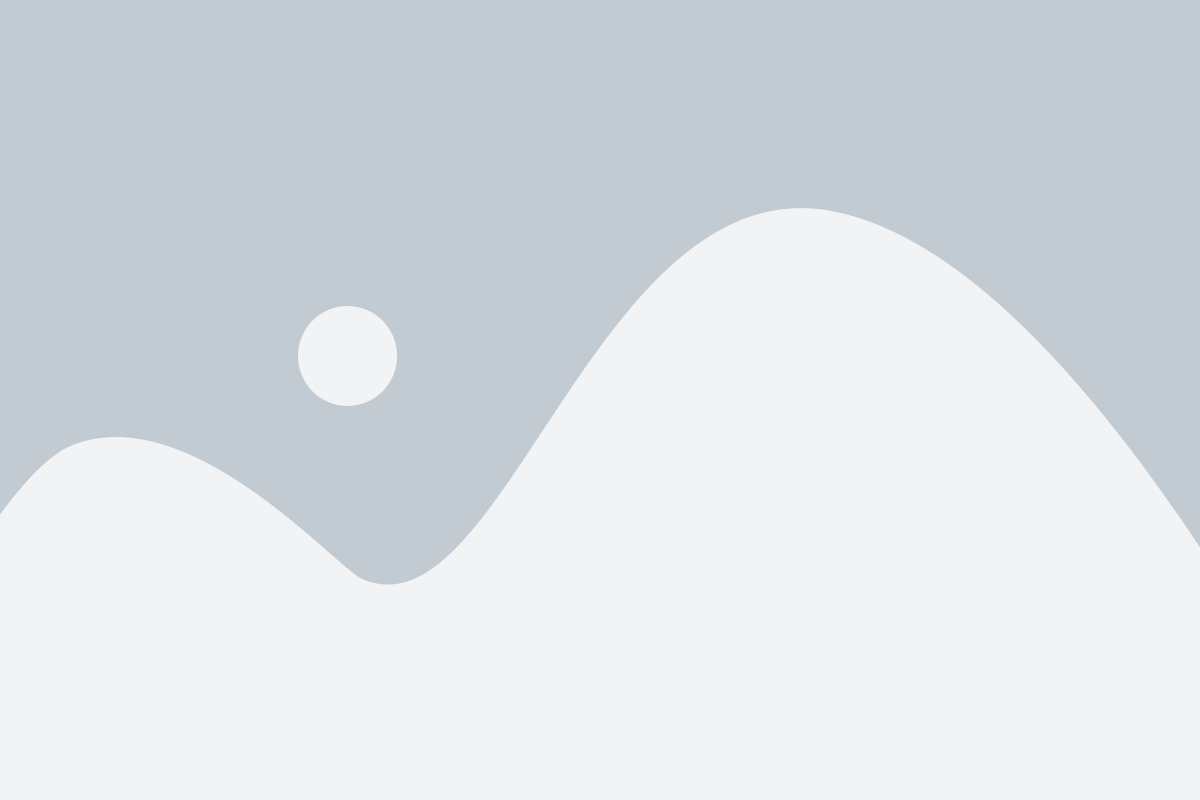
Efficient packaging requires a seamless integration of processes to ensure high-quality output. XINTU’s Drop Case Packer offers a comprehensive solution, combining precision and speed in a single, automated unit. This advanced system is designed to streamline your packaging workflow, maximizing productivity and ensuring cost-effectiveness. Key working principles include:
Product Arrangement System
The system automatically arranges products according to your packing requirements. High-precision mechanisms ensure accurate positioning, reducing the risk of product damage. This step is vital for maintaining the integrity of your products during packing.
Carton Handling System
Your cartons are opened and positioned automatically, ensuring a smooth packing process. The system eliminates the risk of carton jamming, enhancing operational efficiency. This feature is essential for maintaining a steady flow in high-volume operations.
Versatile Application
Our Drop Case Packer is versatile, handling a wide range of product specifications. This flexibility ensures that you can meet diverse market demands with ease, making it an ideal solution for various industries.
Compact and Efficient Design
The compact design of the XINTU Drop Case Packer allows you to perform product arrangement and packing at a single station. This innovative design solves the space constraints typical of conventional packing machines.
Advanced Control System
The advanced control system integrates PLC, touchscreen, standard control buttons, and signal switches, offering both automatic and manual operation modes. This ensures precise control and ease of use.
Easy Fault Detection
With the touchscreen interface, you can easily locate and resolve faults, minimizing downtime and maintaining production efficiency.
Broad Industry Application
Suitable for beverages, edible oils, daily chemicals, and other light industries, the XINTU Drop Case Packer meets the diverse needs of various sectors. Key specifications include:
- Model: FYZX-01DLS
- Carton Size Range: L260-480W180-360H180-360mm
- Packing Speed: 600-800 cases/hour
- Number of Drop Points: 1 group
- Machine Dimensions: L900W1500H1550mm
- Power Supply: 380V, 50/60Hz
- Air Supply: 5-6kg/cm², 460L/min
- Machine Weight: 520kg
This sophisticated machine is built with high-quality materials to ensure durability and long-term performance. By integrating these features, the XINTU Drop Case Packer enhances your packaging efficiency, reduces labor costs, and ensures product safety and quality.
Maintenance of Your XINTU Drop Case Packer
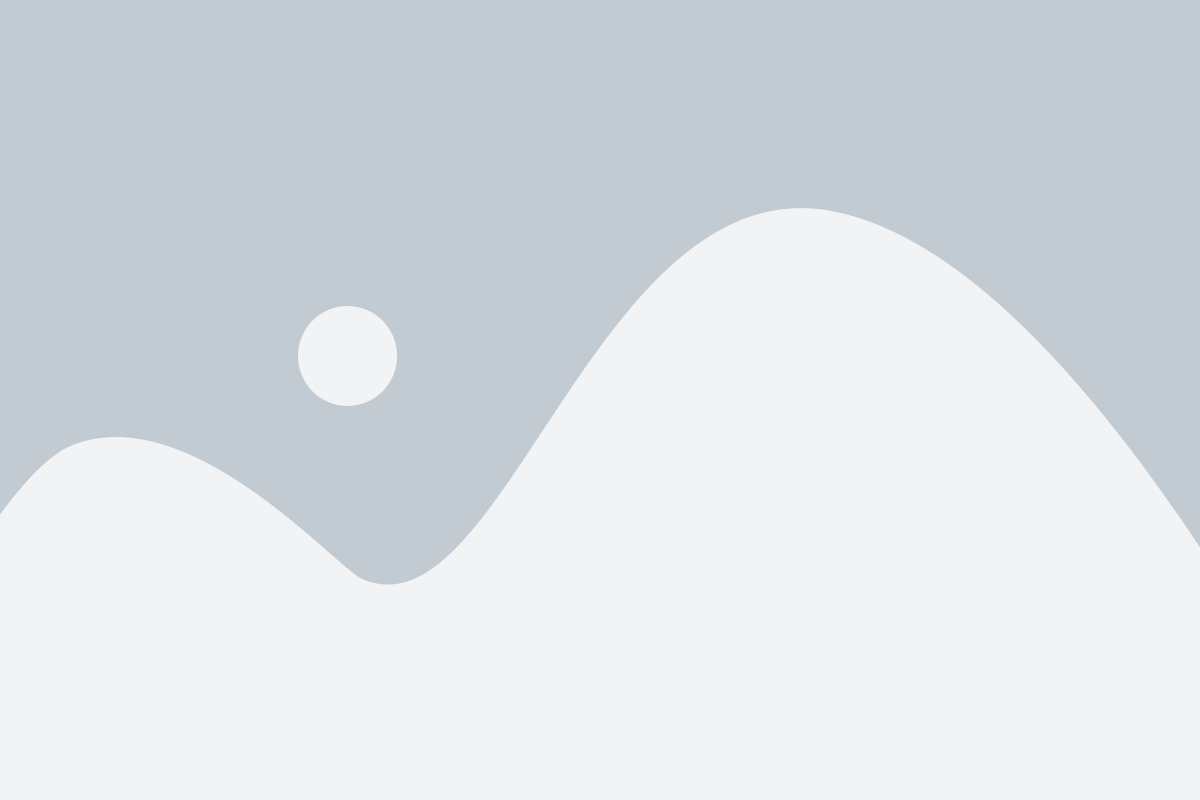
Maintenance of Your XINTU Drop Case Packer
Proper maintenance of your XINTU Drop Case Packer is crucial to ensure its efficient and reliable operation. Here are comprehensive steps and best practices to maintain your equipment:
1. Regular Cleaning and Sanitization
- Daily Cleaning: At the end of each shift, clean the exterior surfaces of the machine to remove dust, debris, and any product residues. Use approved cleaning solutions and ensure no moisture enters the electrical components.
- Weekly Deep Cleaning: Perform a more thorough cleaning weekly, including the interior parts that come into contact with products. This prevents build-up that could affect the machine’s performance.
2. Lubrication
- Identify Lubrication Points: Refer to the machine’s manual to locate all lubrication points. These typically include moving parts like bearings, gears, and actuators.
- Schedule: Lubricate according to the manufacturer’s recommended schedule, typically weekly or monthly, depending on usage. Use the appropriate type of lubricant specified by XINTU.
3. Inspection and Replacement of Worn Parts
- Routine Inspections: Regularly inspect all components for signs of wear and tear. Focus on critical parts such as belts, chains, rollers, and sealing elements.
- Replace Worn Parts: Replace any parts that show significant wear immediately to prevent breakdowns. Keep a stock of essential spare parts to minimize downtime.
4. Calibration and Adjustment
- Sensor Calibration: Regularly calibrate sensors to ensure accurate detection and operation. Misaligned or faulty sensors can lead to inconsistent packing.
- Mechanical Adjustments: Check and adjust mechanical settings such as drop height, alignment guides, and case positioning to maintain precision.
5. Electrical System Maintenance
- Electrical Connections: Inspect all electrical connections for signs of wear or corrosion. Ensure all connections are secure and replace any damaged wiring.
- Control System Updates: Periodically check for firmware or software updates for the machine’s control system. Install updates as provided by XINTU to enhance functionality and security.
6. Pneumatic System Maintenance
- Air Supply Quality: Ensure the air supply is clean and dry. Moisture in the pneumatic system can cause corrosion and reduce efficiency.
- Filter and Valve Inspection: Regularly check and clean air filters. Inspect pneumatic valves for proper operation and replace if necessary.
7. Preventive Maintenance Schedule
- Daily Tasks: Clean machine surfaces, check for obvious wear, and ensure the machine is free of debris.
- Weekly Tasks: Perform deeper cleaning, lubricate moving parts, and inspect key components.
- Monthly Tasks: Calibrate sensors, check electrical connections, and review the machine’s overall performance.
- Quarterly Tasks: Conduct comprehensive inspections, replace worn parts, and perform any necessary software updates.
8. Operator Training
- Comprehensive Training: Ensure all operators are trained on proper machine operation, basic troubleshooting, and maintenance procedures.
- Ongoing Education: Provide continuous training sessions to keep operators updated on best practices and any new features or updates to the machine.
9. Record-Keeping
- Maintenance Logs: Keep detailed records of all maintenance activities, including dates, tasks performed, and parts replaced. This helps track the machine’s history and predict future maintenance needs.
- Issue Reporting: Implement a system for operators to report issues immediately. Prompt reporting and addressing of minor problems can prevent major breakdowns.
10. Manufacturer Support
- Technical Support: Maintain a relationship with XINTU’s technical support team for assistance with complex issues or advanced troubleshooting.
- Service Agreements: Consider service agreements or maintenance contracts with XINTU to ensure regular professional maintenance and prompt support.
By following these maintenance guidelines, you can ensure the optimal performance and longevity of your XINTU Drop Case Packer, reducing downtime and maximizing productivity.
Enhance Your Packaging Efficiency with Drop-Type Case Packers
When it comes to optimizing your packaging line, a drop-type case packer is your ultimate solution. Here's how the advanced technology and essential components of our machine can revolutionize your operations:
Key Components and Technologies:
PLC Control System:
- Benefit: You gain precise control over every aspect of the packaging process, ensuring consistent performance and minimal downtime.
- Feature: Our machines are equipped with state-of-the-art PLC systems, providing you with an intuitive interface and easy programmability.
Servo Motors:
- Benefit: You experience faster, smoother, and more reliable operations, reducing wear and tear on mechanical parts.
- Feature: High-quality servo motors enhance the precision of product handling and placement.
Touchscreen HMI (Human-Machine Interface):
- Benefit: You enjoy a user-friendly interface for monitoring and adjusting machine settings, leading to increased productivity and ease of use.
- Feature: Our HMI panels offer real-time data and diagnostics to keep your operations running smoothly.
Stainless Steel Frame:
- Benefit: You benefit from a durable and easy-to-clean structure, ensuring long-lasting performance even in harsh environments.
- Feature: The robust stainless steel construction meets stringent hygiene standards, making it ideal for food and pharmaceutical industries.
Safety Sensors and Guards:
- Benefit: You can rest assured knowing that your operators are protected, reducing the risk of accidents and ensuring compliance with safety regulations.
- Feature: Advanced safety features include emergency stop buttons, interlocked guards, and safety light curtains.
High-Speed Conveyor System:
- Benefit: You achieve higher throughput with efficient product handling, minimizing bottlenecks and maximizing your production capacity.
Feature: Our conveyors are designed for high-speed operations with adjustable speeds to match your specific needs.
By integrating these advanced components and technologies, our drop-type case packers provide you with unmatched efficiency, reliability, and versatility. Invest in our cutting-edge solutions to enhance your packaging line and meet your production goals with confidence.
Discover the future of packaging with our innovative drop-type case packers—designed to meet your needs and exceed your expectations.
Effortless Installation of Your Drop-Type Case Packer
Ensuring a smooth installation of your drop-type case packer is essential for maximizing productivity and minimizing downtime. Follow these steps to seamlessly integrate your new equipment into your production line.
Installation Steps:
Preparation:
- What You Need: Ensure that you have all necessary tools and equipment ready, including a forklift or crane for heavy lifting, and any required safety gear.
- Site Requirements: Confirm that the installation area meets the machine's specifications, including floor space, power supply, and environmental conditions.
Unpacking and Inspection:
- Check Components: Carefully unpack the machine and inspect all parts for any signs of damage during transit. Verify that all components listed in the manual are present.
- Documentation: Keep the installation manual and any other provided documentation handy for reference throughout the process.
Positioning the Machine:
- Placement: Position the machine in its designated location, ensuring it is level and stable. Use a spirit level to verify alignment.
- Clearances: Make sure there is adequate space around the machine for maintenance and operation, as specified in the installation guide.
Electrical Connections:
- Power Supply: Connect the machine to the appropriate power source, following the voltage and frequency specifications in the manual.
- Grounding: Ensure proper grounding of the machine to prevent electrical hazards. Check that all electrical connections are secure and compliant with local regulations.
Air Supply (if applicable):
- Connection: Attach the air supply to the machine’s pneumatic system, ensuring the air pressure and flow rate meet the manufacturer’s recommendations.
- Testing: Test the air supply connections for leaks and proper functionality.
Mechanical Assembly:
- Components: Assemble any additional mechanical components as instructed in the manual, such as the conveyor system, gripper heads, or safety guards.
- Fasteners: Tighten all bolts and fasteners securely, but avoid over-tightening to prevent damage.
System Integration:
- Interfaces: Integrate the case packer with your existing production line systems, such as upstream and downstream conveyors, sensors, and control systems.
- Communication: Ensure that all control signals and data connections are properly configured for seamless communication between machines.
Initial Calibration:
- Setup: Follow the manual’s instructions to perform an initial calibration of the machine, including setting parameters for product handling and case packing.
- Trial Runs: Conduct trial runs with empty cases to fine-tune the settings and ensure smooth operation.
Operator Training:
- Training Session: Provide a comprehensive training session for your operators, covering machine operation, safety protocols, and basic troubleshooting.
- Manuals and Resources: Make sure that operators have access to the machine’s user manual and any additional training resources.
Final Checks:
- Inspection: Perform a final inspection to ensure all connections are secure, safety features are operational, and the machine is functioning correctly.
- Documentation: Record the installation process and any adjustments made for future reference.
By following these steps, you will ensure that your drop-type case packer is installed correctly and ready to deliver optimal performance. Enjoy the efficiency and reliability that comes with a professionally installed case packer, and watch your production line thrive.
Absolutely, your drop-type case packer is designed to handle products of varying sizes and shapes. Here’s how it achieves this flexibility:
Features and Mechanisms:
Adjustable Gripper Heads:
- How It Works: The machine is equipped with gripper heads that can be easily adjusted to fit different product dimensions. By loosening and tightening screws or using quick-change mechanisms, you can modify the gripper heads to secure products of various sizes and shapes.
- Benefit: This allows for quick and efficient changeovers between different product types without needing extensive downtime.
Programmable PLC System:
- How It Works: The PLC (Programmable Logic Controller) system stores multiple product profiles. Operators can program different settings for various product sizes and shapes, such as drop height, speed, and positioning.
- Benefit: You can switch between different product configurations seamlessly, ensuring optimal performance and minimizing manual adjustments.
Flexible Conveyor System:
- How It Works: The conveyor system features adjustable guides and belts that can be repositioned to accommodate different product widths and lengths. The flexibility in the conveyor setup ensures that products are aligned and conveyed accurately.
- Benefit: This adaptability ensures smooth product flow and precise handling, regardless of the product size or shape.
Customizable Drop Heights and Angles:
- How It Works: The drop mechanism can be adjusted to change the height and angle at which products are dropped into the cases. This customization ensures that products are placed gently and accurately into the cases, reducing the risk of damage.
- Benefit: Tailoring the drop parameters for different products enhances packaging quality and efficiency.
Interchangeable Tooling:
- How It Works: The machine is designed with interchangeable tooling options, allowing operators to swap out components such as chutes and guides that are specific to different product sizes and shapes.
- Benefit: This feature provides versatility and reduces the time needed for changeovers between different product runs.
Advanced Sensors and Detection Systems:
- How It Works: Sensors and detection systems monitor the position and alignment of products as they move through the machine. These sensors can detect variations in product size and shape, automatically adjusting the handling process.
- Benefit: Ensuring that products are correctly aligned and positioned improves packing accuracy and consistency.
User-Friendly HMI (Human-Machine Interface):
- How It Works: The touchscreen HMI allows operators to easily input and adjust settings for different product types. The interface provides real-time feedback and diagnostics, making it simple to fine-tune the machine for various products.
- Benefit: Simplifies the setup process and ensures that the machine operates efficiently across different product configurations.
By incorporating these advanced features, your drop-type case packer can efficiently handle a wide range of product sizes and shapes. This flexibility not only enhances your packaging line's efficiency but also ensures that your operations can adapt to changing product requirements with ease.
There are several types of drop load case packers designed to meet different packaging requirements and production environments. Here's an overview of the main types:
Manual Drop Load Case Packers:
- Description: These packers require manual loading of products into the drop zone before they are automatically placed into cases.
- Applications: Suitable for small-scale operations or facilities with lower production volumes.
Semi-Automatic Drop Load Case Packers:
- Description: Combine manual and automated processes. Operators manually place products into a staging area, and the machine completes the drop and case sealing processes.
- Applications: Ideal for medium-sized operations seeking a balance between cost and automation.
Fully Automatic Drop Load Case Packers:
- Description: Completely automated systems that handle the entire process from product feeding, orientation, dropping, to case sealing without human intervention.
- Applications: Best suited for large-scale operations requiring high-speed, high-volume packaging.
Vertical Drop Load Case Packers:
- Description: Designed to drop products vertically into open cases. This method is often used for products that need to be carefully aligned or oriented.
- Applications: Common in industries packaging bottles, cans, or other items that must maintain a specific orientation.
Horizontal Drop Load Case Packers:
- Description: These packers drop products horizontally into cases, suitable for items that can be laid flat without orientation concerns.
- Applications: Useful for packaging products like trays, blister packs, and other flat items.
Robotic Drop Load Case Packers:
- Description: Utilize robotic arms to pick and place products into cases, offering flexibility and precision.
- Applications: Ideal for complex packaging requirements or products that need delicate handling.
Customizable Drop Load Case Packers:
- Description: Tailored systems designed to meet specific customer needs, accommodating unique product sizes, shapes, and packaging requirements.
- Applications: Suitable for specialized industries with specific packaging demands.
By understanding the different types of drop load case packers, you can choose the one that best fits your production needs, ensuring efficiency, flexibility, and cost-effectiveness in your packaging operations.
Efficiency Benefits of Using the XINTU Drop Case Packer
Leveraging the XINTU Drop Case Packer can significantly enhance the efficiency of your packaging operations. Here are the key benefits:
High-Speed Operation:
- Benefit: You can achieve faster packaging speeds, significantly increasing your throughput.
- Feature: The XINTU Drop Case Packer is designed for high-speed performance, ensuring rapid and efficient packing cycles.
Reduced Downtime:
- Benefit: You minimize production stoppages and maintenance interruptions.
- Feature: The machine is built with durable components and a robust design, reducing the frequency of breakdowns and the need for maintenance.
Versatile Product Handling:
- Benefit: You can handle a wide range of product sizes and shapes with ease, allowing for greater flexibility in your production line.
- Feature: Adjustable gripper heads, customizable drop heights, and interchangeable tooling ensure that the machine can adapt to various products without extensive reconfiguration.
Improved Product Safety:
- Benefit: You reduce the risk of product damage during the packaging process, ensuring higher quality and less waste.
- Feature: The gentle handling mechanisms and precise drop control of the XINTU Drop Case Packer protect your products from damage.
Ease of Use:
- Benefit: You can streamline training and operation processes, reducing the learning curve for new operators.
- Feature: The user-friendly HMI (Human-Machine Interface) provides intuitive controls and real-time diagnostics, simplifying operation and troubleshooting.
Consistent Packing Quality:
- Benefit: You maintain a high standard of packaging quality, ensuring that each product is securely and accurately packed.
- Feature: Advanced sensors and detection systems ensure consistent product placement and alignment within each case.
Energy Efficiency:
- Benefit: You can lower your energy consumption, reducing operational costs and environmental impact.
- Feature: The machine is designed with energy-efficient components and optimized for minimal power usage during operation.
Quick Changeovers:
- Benefit: You can rapidly switch between different product types, minimizing downtime and maximizing production flexibility.
- Feature: Programmable PLC settings and easily adjustable machine components enable quick and efficient changeovers.
Enhanced Safety Features:
- Benefit: You can ensure a safer working environment for your operators, reducing the risk of accidents and injuries.
- Feature: Comprehensive safety mechanisms, including emergency stop buttons, safety guards, and light curtains, protect operators and enhance workplace safety.
Integrated Solutions:
- Benefit: You can seamlessly integrate the drop case packer with other production line equipment, enhancing overall line efficiency.
- Feature: The XINTU Drop Case Packer is compatible with various upstream and downstream systems, allowing for a cohesive and streamlined packaging process.
By utilizing the XINTU Drop Case Packer, you gain significant efficiency advantages, ensuring that your packaging operations are faster, more reliable, and cost-effective. This investment not only boosts your production capabilities but also enhances the quality and safety of your packaging process.
Key Features of the XINTU Drop Case Packer
1. Advanced Automation Controls
- PLC Integration: The packer features a sophisticated PLC control system, ensuring precise and reliable operation. The touch screen interface and standard control buttons make it easy to switch between automatic and manual modes, providing flexibility and ease of use.
2. Compact and Versatile Design
- Space-Saving: The machine's compact footprint allows it to perform product arrangement and packing in a single station, optimizing floor space and improving efficiency. This design is particularly beneficial for facilities with limited space.
3. High Packing Speed
- Efficiency: Capable of packing 600-800 cases per hour, the XINTU Drop Case Packer enhances productivity, making it ideal for high-volume production lines. This high speed does not compromise on the accuracy and quality of packing.
4. Precise Product Handling
- Gentle and Accurate: The system ensures delicate handling of products, minimizing the risk of damage. It accurately arranges and drops products into cases, maintaining their integrity and appearance.
5. Versatile Application Range
- Adaptability: Suitable for a wide variety of products, including beverages, edible oils, daily chemicals, and other light industrial items. The packer can handle different product sizes and shapes, making it highly versatile for diverse production needs.
6. Easy Fault Detection
- User-Friendly Interface: The touch screen interface allows operators to easily identify and troubleshoot faults, minimizing downtime and maintaining continuous operation. This feature ensures quick and efficient problem resolution.
7. Robust Construction
- Durability: Built with high-quality materials, the XINTU Drop Case Packer is designed for long-term use and reliability. Its robust construction ensures minimal maintenance and consistent performance over time.
8. Energy Efficiency
- Sustainable Operation: Designed with energy-saving features, the packer reduces power consumption without sacrificing performance, contributing to lower operational costs and environmental impact.
These key features make the XINTU Drop Case Packer an efficient, reliable, and versatile solution for your packaging needs, enhancing productivity and ensuring high-quality results.
Ensuring Consistent Packing with the XINTU Drop Case Packer
1. Precise Control Systems
- Advanced PLC Controls: The XINTU Drop Case Packer is equipped with advanced PLC controls that provide precise management of the packing process. These controls ensure that each product is handled and packed consistently, maintaining uniformity across all cases.
2. High-Quality Components
- Reliable Mechanisms: The use of high-quality materials and components ensures the machine operates smoothly and reliably. This consistency in performance helps maintain the uniformity of the packing process, reducing variability.
3. Regular Calibration
- Accurate Adjustments: Routine calibration of the machine’s sensors, filling nozzles, and capping heads ensures that each bottle or product is packed to the exact specifications. This process helps maintain consistent fill levels and precise placement within cases.
4. Automated Monitoring and Adjustments
- Real-Time Feedback: The XINTU Drop Case Packer includes sensors and feedback mechanisms that continuously monitor the packing process. Any deviations from the set parameters are immediately corrected, ensuring consistent results.
5. Comprehensive Maintenance Schedule
- Preventive Maintenance: Implementing a thorough maintenance schedule helps prevent wear and tear on the machine’s components. Regular inspections and timely replacements of worn parts ensure the packer operates at peak efficiency, maintaining consistency in packing.
6. Consistent Supply of Materials
- Uniform Inputs: Ensuring a steady supply of uniform bottles, caps, and cases helps maintain consistent packing. Variability in the materials can lead to inconsistencies in the final packed product.
7. Operator Training
- Skilled Workforce: Training operators on the correct use and maintenance of the XINTU Drop Case Packer is crucial. Well-trained operators can identify and resolve minor issues quickly, preventing disruptions and maintaining consistent packing quality.
8. Temperature and Viscosity Control
- Stable Conditions: Maintaining consistent temperature and viscosity of the liquids being packed ensures uniformity. Variations in these parameters can affect the packing process and the quality of the final product.
9. Quality Control Procedures
- Regular Inspections: Implementing stringent quality control measures, such as regular inspections and sampling of packed products, helps ensure that each case meets the required standards. Automated inspection systems can further enhance this process by providing continuous monitoring.
10. Data Analysis and Optimization
- Continuous Improvement: Analyzing production data helps identify trends and areas for improvement. By continuously optimizing the packing process based on this data, you can maintain high levels of consistency and quality.
By focusing on these strategies, the XINTU Drop Case Packer ensures consistent, high-quality packing for all your production needs, enhancing both efficiency and customer satisfaction.
Integrating the XINTU Drop Case Packer into an Existing Production Line
1. Evaluate Current Production Layout
- Site Assessment: Conduct a thorough assessment of your current production layout to identify the optimal location for the new Drop Case Packer. Consider factors such as space availability, workflow, and accessibility for maintenance and operation.
2. Compatibility Check
- Equipment Synchronization: Ensure that the XINTU Drop Case Packer is compatible with your existing equipment, including conveyors, upstream and downstream machines, and control systems. Verify that the mechanical and electrical interfaces align with your current setup.
3. Develop a Detailed Installation Plan
- Step-by-Step Guide: Work with XINTU’s technical team to develop a comprehensive installation plan. This plan should outline each step of the installation process, from initial site preparation to final testing. Include timelines, required resources, and responsibilities.
4. Prepare the Installation Site
- Site Preparation: Clear the designated installation area and ensure it meets the necessary requirements, such as adequate power supply, air pressure, and proper drainage. Make any structural modifications needed to accommodate the new equipment.
5. Mechanical and Electrical Installation
- Professional Setup: Engage professional installers to connect the XINTU Drop Case Packer to your production line. This includes securing the machine, connecting it to power and air supplies, and integrating it with your existing control systems.
6. Integration with Control Systems
- System Integration: Ensure that the Drop Case Packer’s control system is integrated with your existing production line’s control architecture. This might involve configuring PLCs, SCADA systems, and other automation components to ensure seamless operation.
7. Operator Training
- Comprehensive Training: Provide thorough training for your operators on the new machine’s operation, safety protocols, and maintenance procedures. XINTU offers training sessions to ensure your team is fully prepared to handle the new equipment.
8. Conduct Initial Testing
- Test Runs: Perform initial test runs to ensure the Drop Case Packer operates correctly within the production line. Monitor the machine for any issues and make necessary adjustments. This step is crucial for identifying and resolving any integration challenges.
9. Fine-Tuning and Optimization
- Process Optimization: After initial testing, fine-tune the machine settings to optimize performance. Adjust parameters such as packing speed, product handling, and case sealing to achieve the best results. Continuously monitor performance and make incremental improvements.
10. Implement Quality Control Measures
- Consistency Checks: Establish quality control protocols to regularly check the output of the Drop Case Packer. Ensure that the packed products meet your standards and that the machine operates reliably.
11. Ongoing Maintenance and Support
- Regular Maintenance: Implement a maintenance schedule to keep the Drop Case Packer in optimal condition. Regular inspections, lubrication, and part replacements will help prevent downtime and ensure consistent performance. XINTU’s support team is available for any technical assistance you may need.
12. Monitor and Analyze Performance
- Data Collection: Continuously collect and analyze data on the Drop Case Packer’s performance. Use this information to identify areas for further optimization and to ensure the machine operates at peak efficiency.
By following these steps, you can successfully integrate the XINTU Drop Case Packer into your existing production line, enhancing efficiency, productivity, and product quality.
Production Capacity of Different Models of Drop Load Case Packers
The production capacity of Drop Load Case Packers can vary significantly based on the model, design, and intended application. Here’s an overview of the typical capacities for different types of Drop Load Case Packers:
1. Entry-Level Models
- Capacity: 10-20 cases per minute (CPM)
- Suitable For: Small to medium-sized operations, lower volume production lines.
- Applications: Ideal for businesses with limited production needs or those just starting with automated packing solutions.
2. Mid-Range Models
- Capacity: 20-40 cases per minute (CPM)
- Suitable For: Medium-sized operations with moderate production volumes.
- Applications: Suitable for companies experiencing growth and needing to scale up their packaging efficiency.
3. High-Performance Models
- Capacity: 40-60 cases per minute (CPM)
- Suitable For: Large-scale operations requiring high-speed packing solutions.
- Applications: Best for high-volume production lines in industries such as food and beverage, pharmaceuticals, and consumer goods.
4. Customized High-Speed Models
- Capacity: 60+ cases per minute (CPM)
- Suitable For: Very large-scale, high-demand production environments.
- Applications: Tailored for industries with extremely high output requirements, ensuring maximum efficiency and minimal downtime.
Factors Affecting Production Capacity
1. Product Type and Size
- Variability: The size, shape, and fragility of products can impact the speed at which they can be packed. Larger or more delicate items may require slower speeds to ensure careful handling.
2. Case Configuration
- Complexity: The design and complexity of the case configuration can also affect the production speed. More intricate case setups may slow down the packing process.
- Type of Case: Regular slotted containers (RSC), half slotted containers (HSC), and other types of cases may have different handling requirements.
3. Automation Level
- Manual vs. Automated: Fully automated systems generally offer higher speeds compared to semi-automatic or manual systems.
- Advanced Features: Machines with advanced features such as automated fault detection, real-time monitoring, and quick changeover capabilities can enhance overall production speed.
4. Machine Design and Build Quality
- Durability: High-quality, durable machines are designed to operate at higher speeds without frequent maintenance or downtime.
- Precision Engineering: Machines with precise engineering and robust components can handle higher speeds more reliably.
5. Integration with Existing Systems
- Seamless Integration: Machines that integrate seamlessly with existing production lines can maintain higher speeds by reducing bottlenecks and ensuring smooth transitions between different stages of the packing process.
6. Operator Training and Efficiency
- Skilled Workforce: Well-trained operators can maintain and troubleshoot machines more effectively, helping to sustain higher production speeds.
- Efficiency Practices: Implementing efficient operational practices can maximize the machine’s output capabilities.
By considering these factors and understanding the specific needs of your production line, you can select the appropriate model of Drop Load Case Packer that matches your desired production capacity and operational goals.
How to Optimize the Efficiency of a Drop Load Case Packer
Optimizing the efficiency of a Drop Load Case Packer involves several strategies that ensure smooth operation, minimize downtime, and maximize productivity. Here’s a comprehensive guide to achieving optimal efficiency:
1. Regular Maintenance and Inspection
- Preventive Maintenance: Schedule regular maintenance to keep the machine in peak condition. This includes lubrication, cleaning, and checking for worn parts.
- Inspection Routines: Implement routine inspections to identify potential issues before they cause downtime. Focus on key components such as belts, bearings, and sensors.
2. Proper Training for Operators
- Comprehensive Training: Ensure operators are well-trained in using the Drop Load Case Packer. Training should cover machine operation, safety protocols, troubleshooting, and maintenance procedures.
- Continuous Education: Provide ongoing training sessions to keep operators updated on best practices and new technologies.
3. Optimize Workflow and Layout
- Efficient Layout: Arrange your production line to minimize unnecessary movement and ensure a smooth flow of products. Position the Drop Load Case Packer strategically to reduce bottlenecks.
- Streamline Processes: Analyze and streamline processes leading up to and following the packing stage to ensure seamless transitions and continuous operation.
4. Use High-Quality Materials and Parts
- Reliable Components: Invest in high-quality materials and spare parts to reduce the likelihood of breakdowns and ensure consistent performance.
- Consistent Supply: Maintain a consistent supply of quality packing materials, such as cases and inserts, to prevent disruptions.
5. Implement Automation and Advanced Technologies
- Automation Upgrades: Utilize advanced automation features such as real-time monitoring, automated adjustments, and fault detection systems to enhance efficiency.
- PLC and SCADA Systems: Integrate programmable logic controllers (PLCs) and supervisory control and data acquisition (SCADA) systems for precise control and monitoring of the packing process.
6. Monitor and Analyze Performance Data
- Data Collection: Use sensors and monitoring systems to collect data on the machine’s performance, such as packing speed, downtime, and error rates.
- Data Analysis: Analyze the collected data to identify trends, inefficiencies, and areas for improvement. Use this information to make informed decisions and optimizations.
7. Regular Calibration and Adjustments
- Accurate Calibration: Regularly calibrate the machine’s sensors and components to ensure precise operation. This helps maintain consistent packing quality and speed.
- Fine-Tuning: Adjust machine settings based on production needs and product specifications to optimize performance.
8. Implement Quality Control Measures
- Consistent Inspections: Conduct regular quality control checks to ensure that packed products meet required standards. This includes checking case seals, product placement, and overall packaging integrity.
- Automated Quality Control: Consider integrating automated quality control systems that can detect and reject defective packs, ensuring only high-quality products proceed.
9. Minimize Changeover Time
- Quick Changeover Techniques: Implement quick changeover techniques to reduce downtime when switching between different products or case sizes. Use standardized processes and tools to speed up the changeover.
- Flexible Machine Design: Choose a Drop Load Case Packer designed for easy and fast changeovers, with features such as adjustable guides and tool-free adjustments.
10. Ensure Proper Integration with Production Line
- Seamless Integration: Ensure the Drop Load Case Packer integrates seamlessly with upstream and downstream equipment. Synchronize speeds and operations to prevent bottlenecks.
- Communication Systems: Utilize communication systems between different machines to coordinate operations and maintain a steady production flow.
By implementing these strategies, you can optimize the efficiency of your Drop Load Case Packer, leading to increased productivity, reduced operational costs, and enhanced overall performance.
Common Issues with Drop Load Case Packers and How to Troubleshoot Them
Drop Load Case Packers, like any machinery, can encounter various issues that may disrupt production. Here are some common problems and their troubleshooting steps:
1. Inconsistent Case Packing
- Cause: Misalignment of products or cases.
- Troubleshooting:
- Check Alignment: Ensure that products and cases are properly aligned before entering the packing area. Adjust guides and conveyors as needed.
- Inspect Sensors: Verify that sensors detecting product and case positions are clean and functioning correctly.
2. Product Jams
- Cause: Incorrect product size, shape, or improper feeding.
- Troubleshooting:
- Product Specifications: Ensure products meet the size and shape specifications required for the machine.
- Feeding Mechanism: Inspect and adjust the feeding mechanism to ensure smooth product flow. Clear any obstructions immediately.
3. Case Jams
- Cause: Improper case setup or feeding.
- Troubleshooting:
- Case Setup: Verify that cases are correctly set up and fed into the machine. Adjust the case magazine and feeder for consistent operation.
- Clear Obstructions: Remove any cases causing jams and inspect the feeding area for blockages.
4. Inaccurate Drop Placement
- Cause: Miscalibration of the dropping mechanism or timing issues.
- Troubleshooting:
- Recalibrate: Recalibrate the dropping mechanism to ensure precise placement of products into cases.
- Check Timing: Adjust the timing of the drop cycle to synchronize with the case movement.
5. Machine Downtime
- Cause: Mechanical failures, lack of maintenance, or operator error.
- Troubleshooting:
- Regular Maintenance: Implement a routine maintenance schedule to keep the machine in optimal condition. This includes lubrication, cleaning, and parts replacement.
- Operator Training: Ensure operators are well-trained in the machine's operation and maintenance procedures to prevent errors that cause downtime.
6. Electrical Issues
- Cause: Faulty wiring, sensors, or control systems.
- Troubleshooting:
- Inspect Wiring: Check all electrical connections and wiring for signs of wear or damage. Replace any faulty components.
- Test Sensors: Ensure all sensors are working correctly and replace any that are malfunctioning.
- Control System Check: Inspect the control system for errors and reset if necessary. Update software or firmware if needed.
7. Inconsistent Sealing
- Cause: Incorrect sealing temperature, pressure, or timing.
- Troubleshooting:
- Adjust Settings: Check and adjust the sealing temperature, pressure, and timing to match the specifications of the packaging material.
- Inspect Sealing Mechanism: Ensure the sealing mechanism is clean and free of debris. Replace worn or damaged sealing elements.
8. Excessive Noise
- Cause: Loose components or lack of lubrication.
- Troubleshooting:
- Tighten Components: Inspect the machine for any loose bolts or components and tighten them as needed.
- Lubricate Moving Parts: Apply lubrication to moving parts to reduce friction and noise.
9. Product Damage
- Cause: Rough handling or improper machine settings.
- Troubleshooting:
- Adjust Handling Settings: Fine-tune the machine settings to handle products more gently. This may include adjusting the drop height and speed.
- Use Protective Materials: Introduce protective materials or inserts to cushion products during the packing process.
10. Faulty Automation Controls
- Cause: Software glitches or programming errors.
- Troubleshooting:
- Software Update: Check for and install any available updates to the machine's software or control system.
- Reprogram if Needed: If there are persistent issues, reprogram the control system according to the manufacturer’s guidelines.
Preventive Measures
To minimize the occurrence of these issues, consider the following preventive measures:
- Regular Training: Continuously train operators and maintenance staff on the latest troubleshooting techniques and machine updates.
- Routine Inspections: Conduct regular inspections and maintenance to identify and address potential issues before they cause significant downtime.
- Spare Parts Inventory: Keep an inventory of critical spare parts to ensure quick replacements and minimize downtime.
- Manufacturer Support: Maintain a relationship with the manufacturer for technical support and advice on optimizing machine performance.
By addressing these common issues proactively and implementing preventive measures, you can ensure the efficient and reliable operation of your Drop Load Case Packer, enhancing overall productivity and reducing operational disruptions.
Energy Requirements for Operating the XINTU Drop Case Packer
1. Electrical Power Supply
- Voltage and Frequency: The XINTU Drop Case Packer typically requires a stable electrical supply of 380V at 50/60Hz. This ensures that the machine operates efficiently and reliably.
- Power Consumption: Depending on the specific model and its capacity, the power consumption for the XINTU Drop Case Packer generally ranges between 2 to 5 kilowatts (kW). Larger models with higher capacities may require up to 10 kW.
2. Compressed Air Supply
- Pressure Requirements: The machine requires a compressed air supply with a pressure of 5-6 kg/cm² (approximately 70-85 psi) to operate various pneumatic components, such as actuators and valves.
- Air Flow Rate: An air flow rate of around 460 liters per minute (L/min) is necessary to ensure consistent and reliable operation of the pneumatic systems.
3. Energy Efficiency Features
- Variable Frequency Drives (VFDs): The XINTU Drop Case Packer may be equipped with variable frequency drives, which adjust motor speeds based on real-time operational needs. This feature helps reduce overall energy consumption and improves efficiency.
- Energy-Saving Modes: Some models may include energy-saving modes that optimize power usage during idle times or low-demand periods, further reducing energy costs.
4. Regular Maintenance for Optimal Efficiency
- Preventive Maintenance: Regular maintenance of the machine ensures that it operates at peak efficiency. This includes routine inspections, lubrication, and timely replacement of worn parts, which helps prevent unnecessary energy consumption due to mechanical issues.
- Calibration and Tuning: Periodic calibration and tuning of the machine’s components ensure that it runs smoothly and efficiently, minimizing energy waste.
5. Environmental Considerations
- Eco-Friendly Design: The XINTU Drop Case Packer is designed with environmental sustainability in mind. Energy-efficient components and systems reduce the machine’s carbon footprint, aligning with green manufacturing practices.
- Waste Reduction: Efficient operation reduces product waste and energy usage, contributing to overall environmental conservation efforts.
6. Facility Requirements
- Electrical Infrastructure: Ensure that your facility’s electrical infrastructure can handle the power requirements of the XINTU Drop Case Packer. This includes adequate wiring, circuit breakers, and grounding to support the machine’s operation.
- Compressed Air System: A reliable compressed air system with appropriate capacity and pressure regulation is essential for optimal performance. Regular checks and maintenance of the air supply system are necessary to avoid interruptions.
By meeting these energy requirements and maintaining the machine properly, you can ensure that the XINTU Drop Case Packer operates efficiently and sustainably, contributing to reduced operational costs and environmental impact.
Safety Features Included in the XINTU Drop Case Packer
1. Automated Shutdown Mechanism
- Malfunction Detection: The machine is equipped with sensors that detect malfunctions or anomalies in operation. If any issue is detected, the automated shutdown mechanism activates to prevent accidents and damage.
- Overload Protection: This feature protects the machine from overloading by automatically shutting down if excessive load or pressure is detected, ensuring the safety of the equipment and operators.
2. Safety Guards and Enclosures
- Physical Barriers: Safety guards and enclosures are installed around moving parts to prevent accidental contact. These barriers protect operators from potential injuries caused by moving components.
- Transparent Covers: Transparent covers allow operators to monitor the machine’s operation while maintaining a safe distance from moving parts.
3. Emergency Stop Buttons
- Accessible Placement: Emergency stop buttons are strategically placed around the machine, ensuring they are easily accessible in case of an emergency. Operators can quickly halt the machine’s operation if needed.
- Instant Shutdown: Pressing the emergency stop button immediately shuts down the machine, preventing accidents and allowing for quick response to any hazardous situations.
4. Interlock Systems
- Guard Interlocks: The machine is equipped with interlock systems that prevent it from operating if a safety guard or door is open. This ensures that the machine cannot be started accidentally while maintenance or adjustments are being made.
- Door Safety Sensors: Sensors on access doors ensure that the machine stops operating when a door is opened, providing an additional layer of safety for operators.
5. Temperature and Pressure Sensors
- Real-Time Monitoring: Temperature and pressure sensors continuously monitor critical parameters within the machine. If these parameters exceed safe levels, the machine can shut down or alert the operator, preventing potential hazards such as overheating or overpressure.
- Alarm Systems: The machine includes alarm systems that notify operators of any deviations from normal operating conditions, allowing for immediate corrective action.
6. User-Friendly Interface
- Clear Warnings and Instructions: The control interface displays clear warnings and operational instructions, guiding operators through safe operation procedures. This reduces the likelihood of operator error and enhances overall safety.
- Diagnostic Displays: The interface provides diagnostic information, helping operators quickly identify and resolve issues without compromising safety.
7. Robust Construction
- Durable Materials: The XINTU Drop Case Packer is constructed using high-quality, durable materials that ensure long-term reliability and safety. The robust construction minimizes the risk of mechanical failures that could lead to accidents.
- Anti-Corrosive Coating: Components are treated with anti-corrosive coatings to prevent degradation, ensuring the machine’s structural integrity over time.
8. Regular Maintenance Protocols
- Scheduled Inspections: Regular maintenance schedules include thorough inspections of safety features and components, ensuring they are in optimal working condition. This proactive approach helps prevent accidents and maintain a safe working environment.
- Replacement of Worn Parts: Timely replacement of worn or damaged parts ensures that safety features remain effective and the machine operates safely.
9. Comprehensive Operator Training
- Safety Training Programs: Operators receive comprehensive training on the safe use and maintenance of the XINTU Drop Case Packer. This training includes proper handling of emergency situations and adherence to safety protocols.
- Ongoing Education: Regular refresher courses and updates on safety practices ensure that operators stay informed about the latest safety measures and procedures.
By incorporating these safety features, the XINTU Drop Case Packer provides a secure working environment, protecting both operators and products while ensuring efficient and reliable operation.
How to Choose the Right Drop Load Case Packer for Your Packaging Needs
Selecting the right Drop Load Case Packer for your packaging needs involves several important considerations. Here’s a guide to help you make an informed decision:
1. Determine Your Production Volume
- Current and Future Needs: Evaluate your current production volume and anticipate future growth. Choose a machine that can handle your current output while allowing for potential increases in production.
2. Understand Your Product Specifications
- Product Dimensions and Weight: Ensure the case packer can accommodate the size, shape, and weight of your products. Consider any variations in product dimensions.
- Product Fragility: If your products are fragile, look for a packer that offers gentle handling to minimize damage.
3. Define Packaging Requirements
- Case Sizes and Types: Verify that the machine can handle the range of case sizes and types you use. This includes regular slotted containers (RSC), half slotted containers (HSC), and others.
- Packaging Formats: Determine whether you need a packer that can handle specific packaging formats, such as bottles, cans, cartons, or trays.
4. Evaluate Speed and Efficiency
- Packing Speed: Consider the machine’s packing speed and ensure it aligns with your production line’s requirements. Higher speeds are essential for large-scale operations.
- Efficiency and Downtime: Look for machines with features that minimize downtime, such as easy maintenance access and quick changeover capabilities.
5. Integration with Existing Systems
- Compatibility: Ensure the case packer can integrate seamlessly with your existing production line and automation systems. This includes compatibility with conveyors, upstream, and downstream equipment.
- Control Systems: Check if the machine’s control system can interface with your existing PLC or SCADA systems for synchronized operation.
6. Assess the Level of Automation
- Manual, Semi-Automatic, or Fully Automatic: Choose the level of automation that fits your needs. Fully automatic machines are ideal for high-volume operations, while semi-automatic or manual options may be sufficient for smaller production lines.
- Advanced Features: Consider additional features such as automated fault detection, real-time monitoring, and touch screen interfaces for ease of use.
7. Quality and Durability
- Build Quality: Select a machine made from high-quality materials to ensure durability and long-term reliability. Look for features like corrosion-resistant coatings and robust construction.
- Manufacturer Reputation: Choose a machine from a reputable manufacturer known for producing reliable and high-quality equipment.
8. Maintenance and Support
- Ease of Maintenance: Opt for machines with easy access for maintenance and cleaning. Regular maintenance ensures optimal performance and longevity.
- Technical Support and Service: Ensure the manufacturer offers excellent technical support and after-sales service. Availability of spare parts and prompt service can minimize downtime.
9. Budget and Cost-Effectiveness
- Initial Investment vs. Long-Term Savings: Consider the initial cost of the machine against the long-term savings in labor, efficiency, and reduced downtime. Investing in a high-quality machine can offer better returns over time.
- Operational Costs: Evaluate the operational costs, including energy consumption and maintenance expenses, to ensure the machine fits within your budget.
10. Customization Options
- Tailored Solutions: If you have specific packaging needs, look for manufacturers that offer customization options. Tailored solutions can better meet your unique production requirements.
11. Compliance and Standards
- Industry Standards: Ensure the machine complies with industry standards and regulations relevant to your products and market. This includes safety standards, hygiene requirements, and environmental regulations.
By considering these factors, you can select the right Drop Load Case Packer that meets your packaging needs, enhances productivity, and ensures efficient and reliable operation.
How to Train Staff to Operate a Drop Load Case Packer Safely
Training staff to operate a Drop Load Case Packer safely is crucial for ensuring efficient operations, minimizing downtime, and preventing workplace accidents. Here’s a comprehensive guide to training your staff effectively:
1. Develop a Comprehensive Training Program
- Training Modules: Create detailed training modules covering all aspects of the machine, including operation, maintenance, troubleshooting, and safety protocols.
- Documentation: Provide operators with comprehensive manuals and documentation, including step-by-step guides, diagrams, and safety instructions.
2. Initial Training for New Operators
- Introduction to Equipment: Familiarize new operators with the Drop Load Case Packer, explaining its components, functions, and safety features.
- Hands-On Demonstrations: Conduct hands-on demonstrations, allowing operators to observe the machine in action. Highlight key operations, controls, and safety precautions.
3. Focus on Safety Protocols
- Personal Protective Equipment (PPE): Emphasize the importance of wearing appropriate PPE, such as gloves, safety glasses, and hearing protection.
- Emergency Procedures: Teach operators how to use emergency stop buttons and other safety devices. Ensure they understand the procedure for shutting down the machine safely in case of an emergency.
- Hazard Identification: Train staff to recognize potential hazards, such as pinch points, moving parts, and electrical components, and how to avoid them.
4. Detailed Operational Training
- Start-Up and Shut-Down Procedures: Provide clear instructions on how to start up and shut down the machine correctly, including pre-operation checks.
- Normal Operation: Train operators on the normal operation of the machine, including loading products, adjusting settings, and monitoring the packing process.
- Troubleshooting Common Issues: Teach operators how to identify and troubleshoot common issues, such as jams, misalignments, and sensor errors.
5. Maintenance Training
- Routine Maintenance: Instruct operators on routine maintenance tasks, such as cleaning, lubrication, and inspection of components.
- Preventive Maintenance: Emphasize the importance of preventive maintenance to ensure the machine operates efficiently and safely. Provide schedules and checklists for regular maintenance activities.
- Record-Keeping: Train operators to document maintenance activities, issues encountered, and actions taken in maintenance logs.
6. Continuous Education and Refresher Courses
- Ongoing Training: Offer regular refresher courses to keep operators updated on best practices, new technologies, and any changes in safety regulations.
- Advanced Training: Provide opportunities for advanced training on more complex aspects of the machine and its operation.
7. Hands-On Practice and Simulations
- Supervised Practice: Allow operators to practice operating the machine under supervision, providing guidance and feedback.
- Simulation Exercises: Conduct simulation exercises for emergency situations, such as power failures or mechanical malfunctions, to ensure operators can respond effectively.
8. Assessment and Certification
- Knowledge Tests: Administer written or oral tests to assess operators’ understanding of the machine, its operation, and safety protocols.
- Practical Assessments: Conduct practical assessments to evaluate operators’ ability to operate the machine safely and efficiently.
- Certification: Provide certification for operators who successfully complete the training program, demonstrating their competence in operating the Drop Load Case Packer.
9. Encourage a Safety Culture
- Open Communication: Foster an environment where operators feel comfortable reporting safety concerns or operational issues without fear of reprimand.
- Regular Safety Meetings: Hold regular safety meetings to discuss best practices, share experiences, and reinforce the importance of safety.
- Safety Incentives: Implement a safety incentive program to reward operators for following safety protocols and maintaining a safe working environment.
10. Utilize Manufacturer Support
- Manufacturer Training: Take advantage of training programs offered by the machine manufacturer. Manufacturer experts can provide in-depth knowledge and insights.
- Technical Support: Maintain contact with the manufacturer for technical support and guidance on complex issues or advanced training needs.
By implementing these training strategies, you can ensure that your staff is well-equipped to operate the Drop Load Case Packer safely and efficiently, reducing the risk of accidents and enhancing overall productivity.
Latest Technological Advancements in Drop Load Case Packers
The field of Drop Load Case Packers has seen significant technological advancements aimed at improving efficiency, flexibility, and safety. Here are some of the latest innovations:
1. Advanced Automation and Control Systems
- Programmable Logic Controllers (PLCs): Modern Drop Load Case Packers are equipped with sophisticated PLCs that offer enhanced control over the packing process, allowing for precise adjustments and real-time monitoring.
- Human-Machine Interfaces (HMIs): User-friendly HMIs provide operators with intuitive control panels, enabling easy operation, quick adjustments, and real-time data visualization.
2. Robotics Integration
- Robotic Arms: The integration of robotic arms allows for precise and flexible handling of products. These arms can be programmed for a variety of movements, ensuring gentle handling and accurate placement into cases.
- Collaborative Robots (Cobots): Cobots work alongside human operators, enhancing productivity and safety by taking on repetitive or strenuous tasks while operators manage more complex functions.
3. Vision Systems and Artificial Intelligence (AI)
- Vision Inspection Systems: Advanced vision systems use cameras and AI algorithms to inspect products and cases for defects, ensuring high-quality packing. These systems can detect misalignment, missing products, and other issues.
- AI-Powered Optimization: AI algorithms analyze data from the packing process to optimize machine performance, predict maintenance needs, and reduce downtime.
4. IoT and Connectivity
- Internet of Things (IoT): IoT-enabled Drop Load Case Packers connect to the internet, allowing for remote monitoring, diagnostics, and control. This connectivity facilitates predictive maintenance and reduces the need for on-site intervention.
- Cloud Integration: Data collected from IoT devices can be stored and analyzed in the cloud, providing insights into machine performance, production trends, and operational efficiency.
5. Enhanced Safety Features
- Advanced Safety Sensors: Modern machines are equipped with a variety of sensors that detect potential hazards and automatically shut down operations to prevent accidents.
- Virtual Fencing: Virtual fencing technology creates safe zones around the machine, ensuring operators stay clear of moving parts. If an operator enters a restricted area, the machine will stop immediately.
6. High-Speed and High-Precision Mechanisms
- Servo Motors: The use of servo motors allows for precise control of the packing process, enabling high-speed operation without sacrificing accuracy.
- High-Precision Actuators: Advanced actuators provide smooth and precise movements, reducing product damage and ensuring consistent packing quality.
7. Modular and Flexible Designs
- Modular Components: Modular design allows for easy upgrades and customization, enabling manufacturers to adapt the machine to changing production needs without extensive reconfiguration.
- Quick Changeover Systems: Quick changeover mechanisms enable fast transitions between different product sizes and case formats, reducing downtime and increasing productivity.
8. Energy Efficiency and Sustainability
- Energy-Saving Technologies: Modern Drop Load Case Packers incorporate energy-efficient motors, drives, and components that reduce power consumption and operational costs.
- Sustainable Materials: The use of sustainable materials in machine construction and packaging materials helps reduce the environmental impact.
9. Predictive Maintenance
- Condition Monitoring: Sensors continuously monitor the condition of critical components, providing data on wear and tear. This information helps schedule maintenance before failures occur, reducing unexpected downtime.
- Predictive Analytics: Advanced analytics use historical data to predict future maintenance needs, optimizing the maintenance schedule and extending the machine’s lifespan.
10. Enhanced Customization Options
- Tailored Solutions: Manufacturers offer highly customizable Drop Load Case Packers that can be tailored to specific production requirements, accommodating various product types, sizes, and packaging formats.
- Industry-Specific Features: Machines can be equipped with features specific to certain industries, such as food and beverage, pharmaceuticals, and consumer goods, ensuring compliance with industry standards and regulations.
By incorporating these technological advancements, Drop Load Case Packers have become more efficient, versatile, and reliable, meeting the evolving needs of modern production environments and enhancing overall operational efficiency.