XINTU’s Top Load Case Packer is perfect for various packaging forms, especially for products that require careful handling and precise placement.
This machine excels in packaging applications such as:
- Food and Beverage: Ensuring products like bottles, cans, and cartons are packed securely.
- Pharmaceuticals: Providing gentle handling for sensitive medical products.
- Consumer Goods: Perfect for items that need to maintain their orientation during packing.
Our Top Load Case Packer can achieve impressive efficiency rates, reaching up to 40 cases per minute.Standout features such as Gentle Product Handling,Versatility in Packaging,High-Speed Performance,Easy Integration and Customization,Advanced Automation and Control,Space Efficiency and Cost-Effective Operation.
Main Features
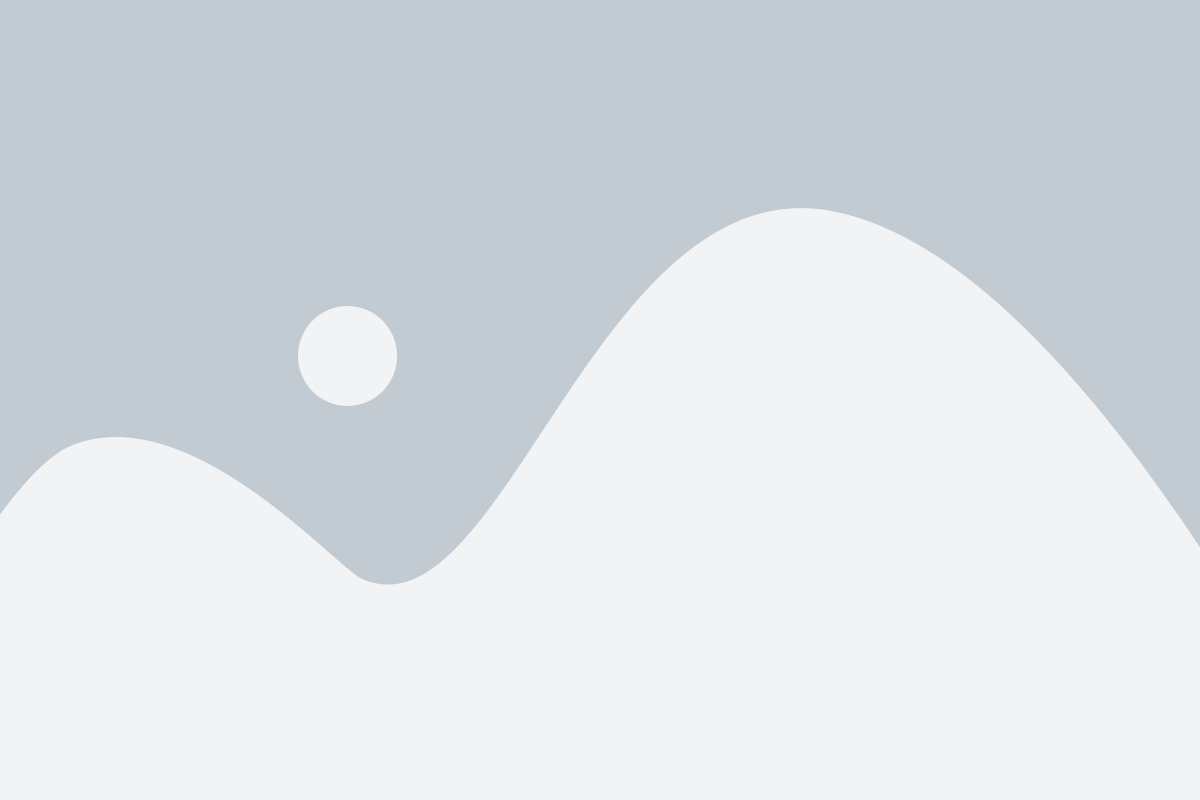
Remote Support Capability
Benefit from remote access capability, enabling real-time monitoring and support. This feature ensures prompt assistance and troubleshooting from our experts, reducing downtime and maintaining peak performance.
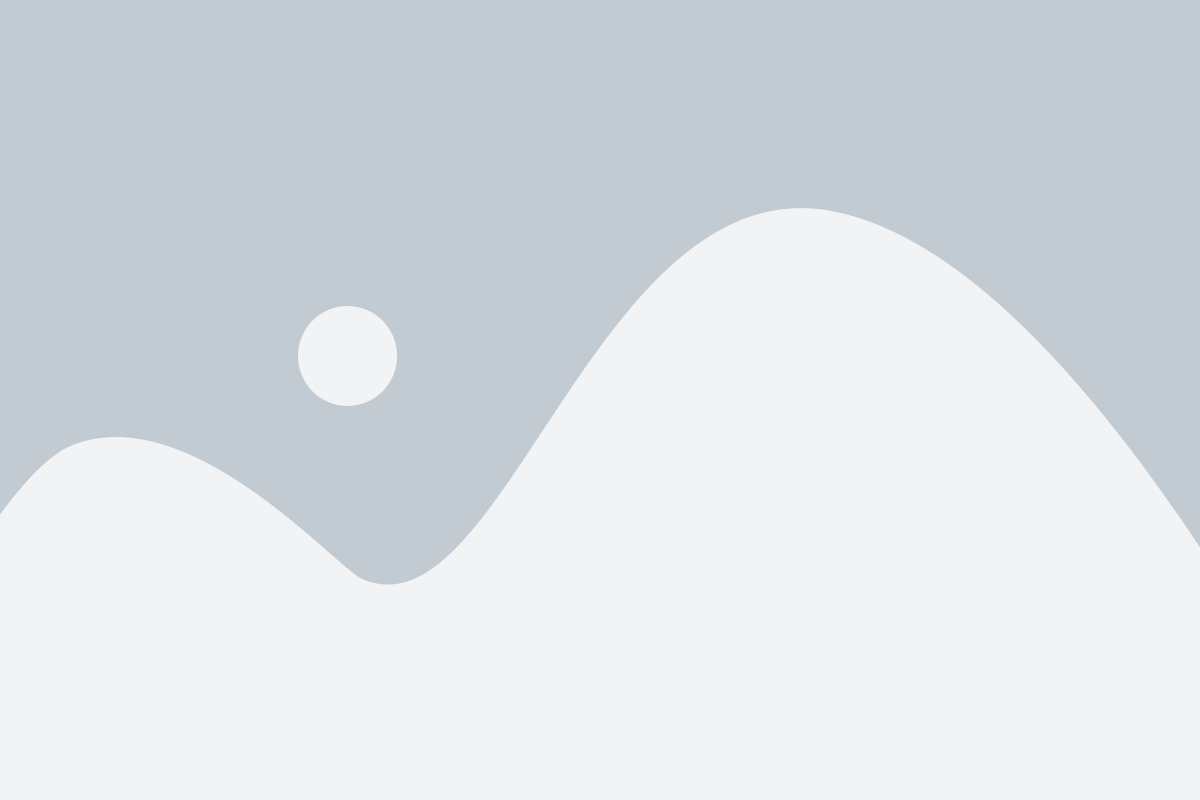
Convenient Maintenance Space
Our top load case packer features a convenient maintenance space, allowing for easy access to machine components. This facilitates maintenance and troubleshooting without disrupting production.
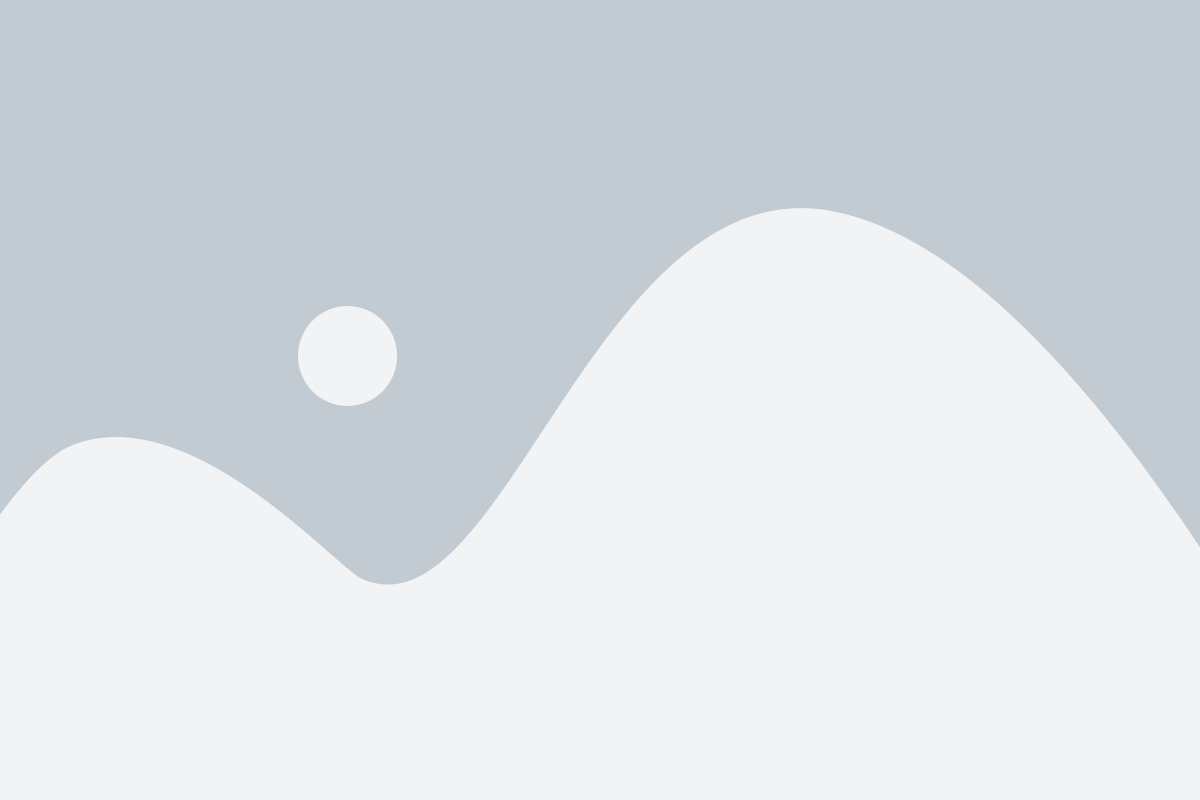
Advanced HMI Design
Experience the industry’s most advanced HMI design with XINTU’s top load case packer. Its intuitive and clean layout simplifies operation and training, reducing errors and enhancing efficiency. Interactive guides and live sensor maps ensure smooth and efficient processes.
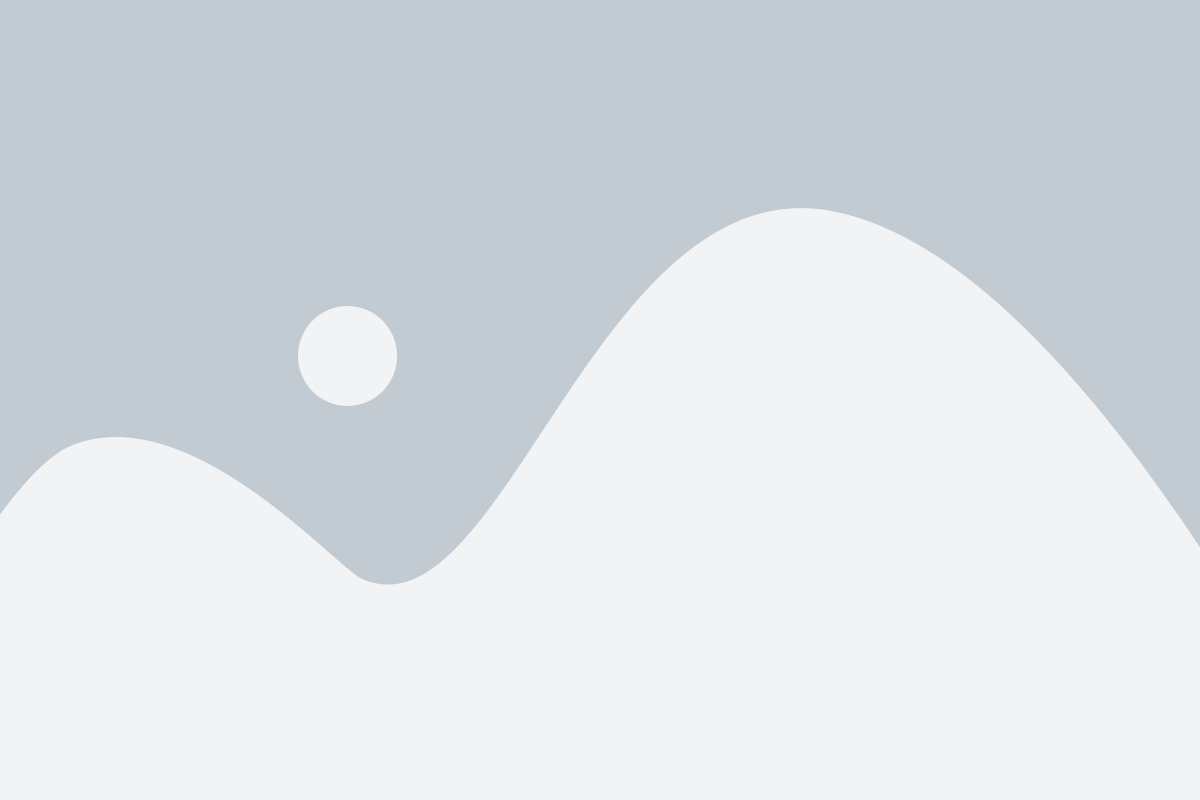
Quick Changeover
Achieve fast and seamless changeovers with XINTU’s cutting-edge HMI system. Designed for efficiency, it features intuitive navigation, interactive changeover guides, fault-recovery support, live sensor maps, and advanced maintenance options. Technicians can execute changeovers in under 5 minutes, eliminating the need for additional tools.
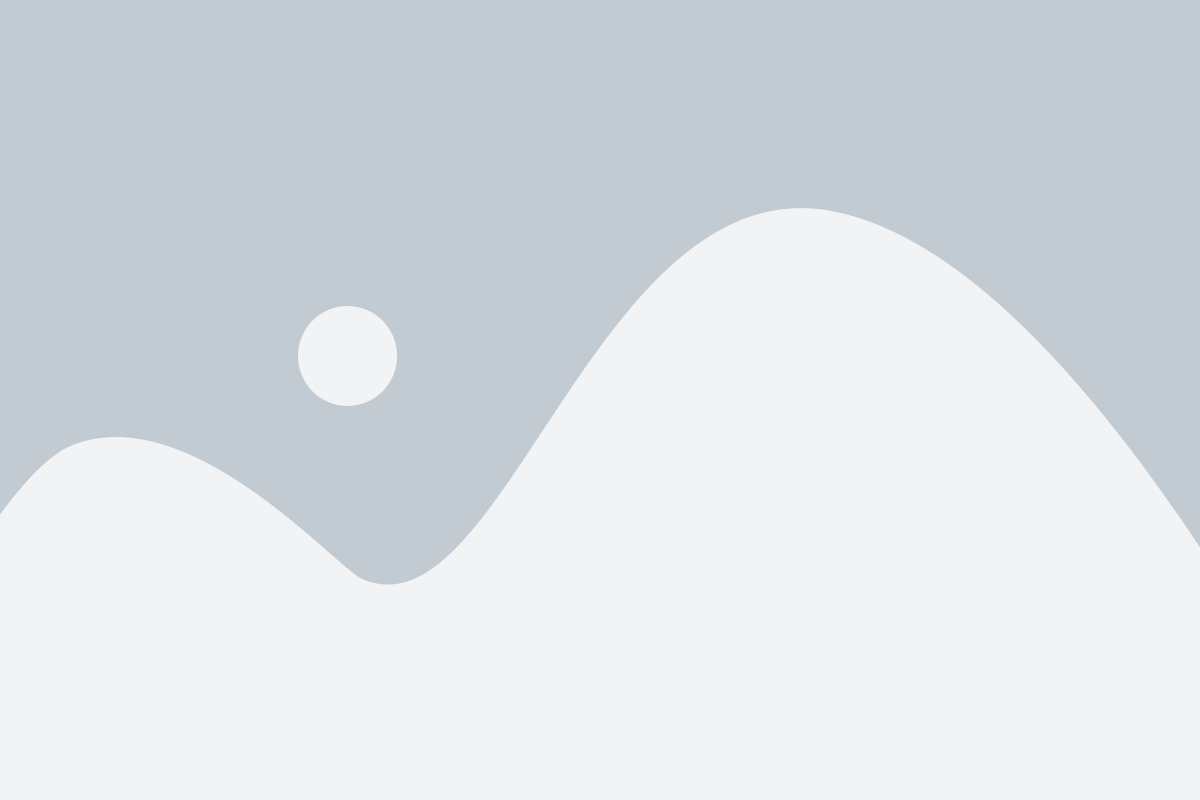
Enhanced Operator Station
XINTU’s top load case packer is equipped with a dedicated operator station that enhances control and flexibility. This station ensures smooth operation and easy adjustments, promoting continuous and efficient packing processes.
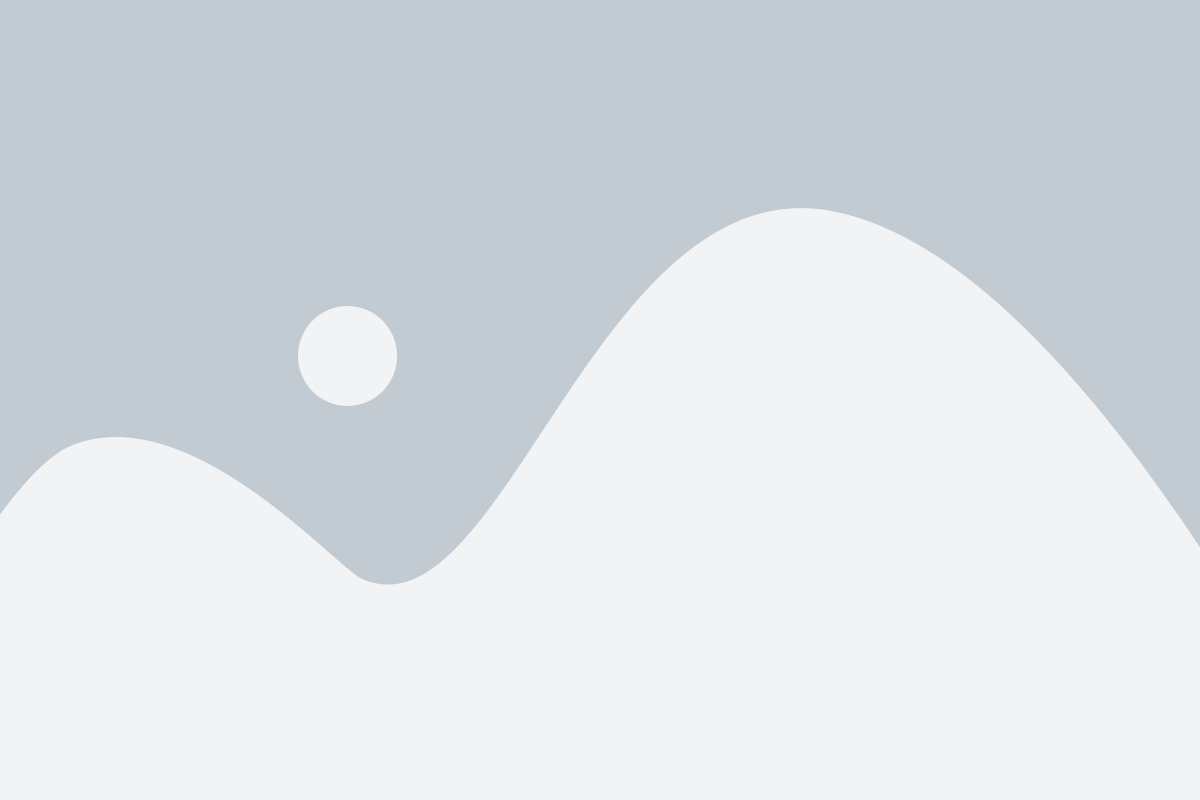
Robust Non-Contact Interlocks
Rely on the highest level of security with our robust non-contact interlocks. These interlocks ensure safe and efficient machine operation, minimizing the risk of downtime due to safety concerns.
ADVANTAGES
High-Speed Efficiency
Up to 60 cases/min for maximum productivity.
Precision Handling
99.9% accuracy in product placement.
Space-Saving Design
25% smaller footprint than competitors
Cost-Effective Operation
Reduces maintenance costs by 30%
SPECIFICATION
Speed
Up to 5-15 cases per minute
Up to 300-900 cases per hour
Packaging speed vary according to number of Servo Modules.
Case sizes
Can be customized
Operation
Servo Modules
Changeover
- Intuitive HMI Graphical Instructions
- Quick, Easy Tool Changeover,Simple External Adjustments
- 10 Minutes Changeover (Estimated time for Skilled Technician)
Construction
Carbon steel
Stainless steel
Control Method
PLC+Touch Screen
Power Supply
380V/50Hz or 60Hz(Customized to the industrial voltage of the customer’s plant)
Air Supply
Approx. 6-7kg/cube
Package Support
Bottles,jars,cans, soft bags,pouches,boxes etc.
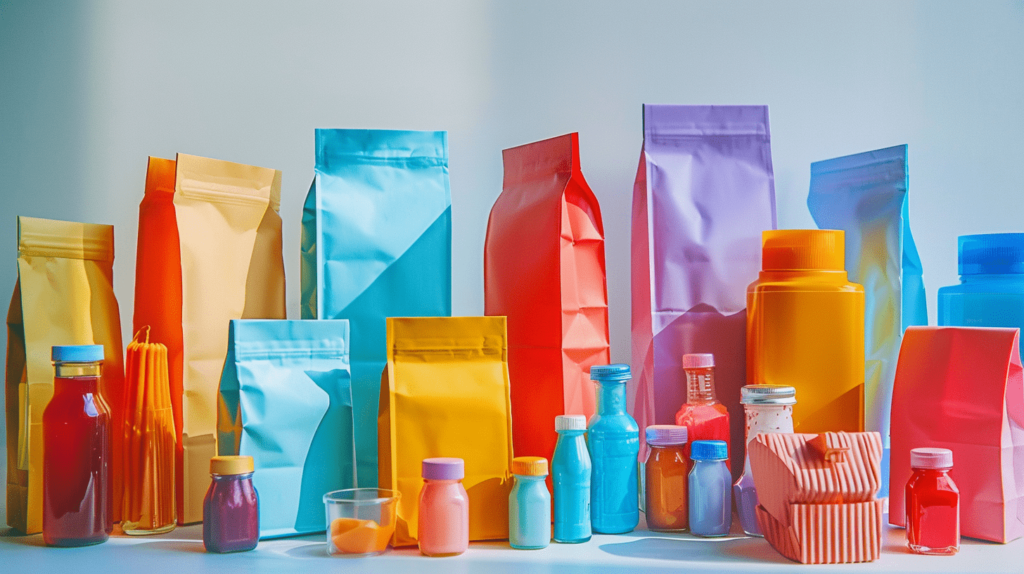
Case Support
Regular Slotted Cartons(RSC)/Windowed Box/Display Box/Double Wall Box/Mailer Box/Telescope Box/Display carton
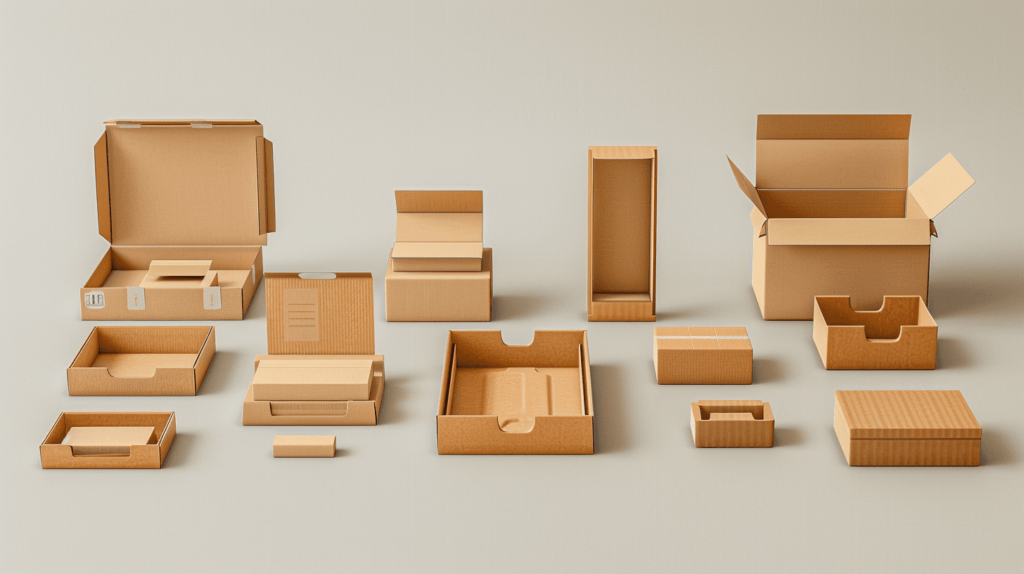
VIDEOS
Top Load Case Packer For Gable Top Catons
Your production line can achieve unmatched speed and efficiency with our Top Load case packaging machine, packing 12 gable top or Tetra Pak cartons in just 6 seconds per cycle. Handling up to 7,200 cartons per hour, it ensures high productivity and reliability. Perfect for dairy, beverage, and food industries.
Top Load Case Packer For Bottled Sterilizer
Your production line benefits from our case packer’s precision, organizing and packing 56 bottles in just 10 seconds. It handles high volumes with ease, ensuring reliable, consistent packaging. Ideal for pharmaceuticals, personal care, and household products.
Top Load Case Packer For Ice Cream
Your production line will benefit from our case packer’s efficient operation, packing 8 ice cream packs in 4 seconds. It reorients packs and places them seamlessly into cartons, ensuring high-volume, consistent packaging. Ideal for frozen foods, dairy products, and other high-demand sectors.
LAYOUT DRAWINGS
Explore our extensive range of Packaging layout solutions tailored for your project needs.
RELATED EQUIPMENT
Integrated packaging line solutions
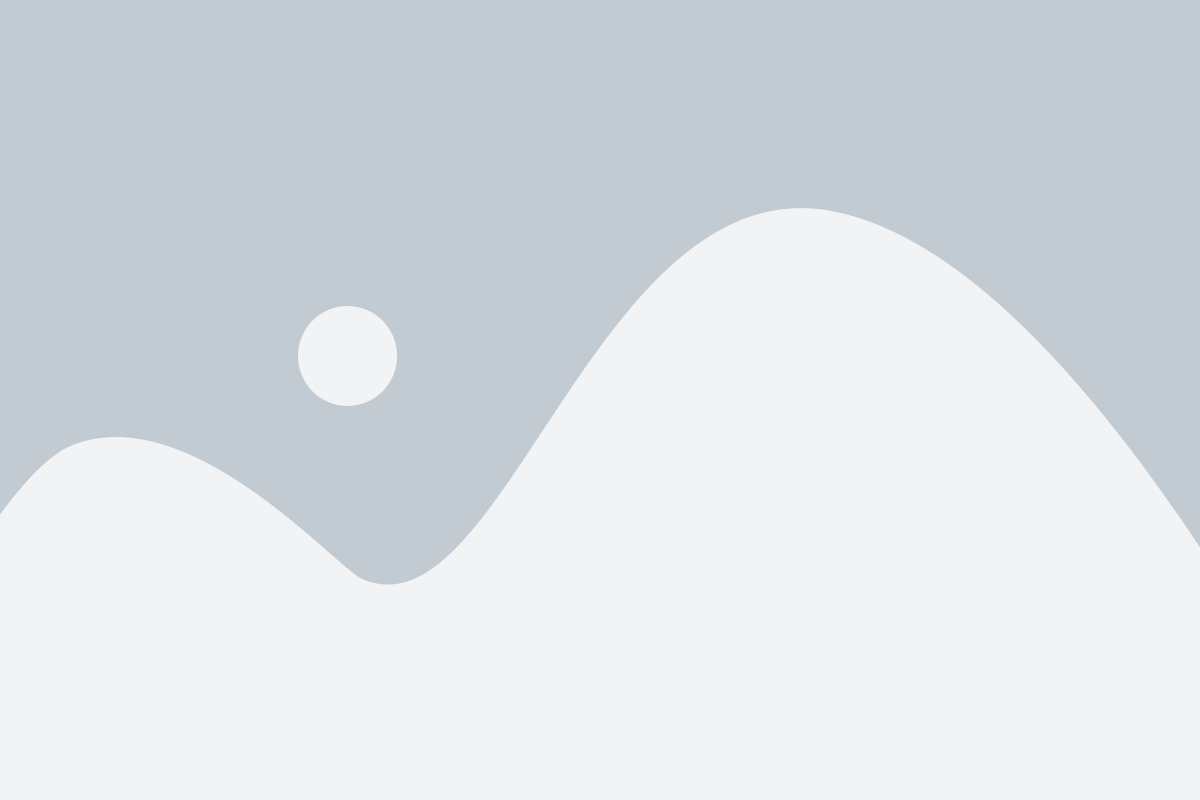
Add Your Heading Text Here
Lorem ipsum dolor sit amet, consectetur adipiscing elit. Ut elit tellus, luctus nec ullamcorper mattis, pulvinar dapibus leo.
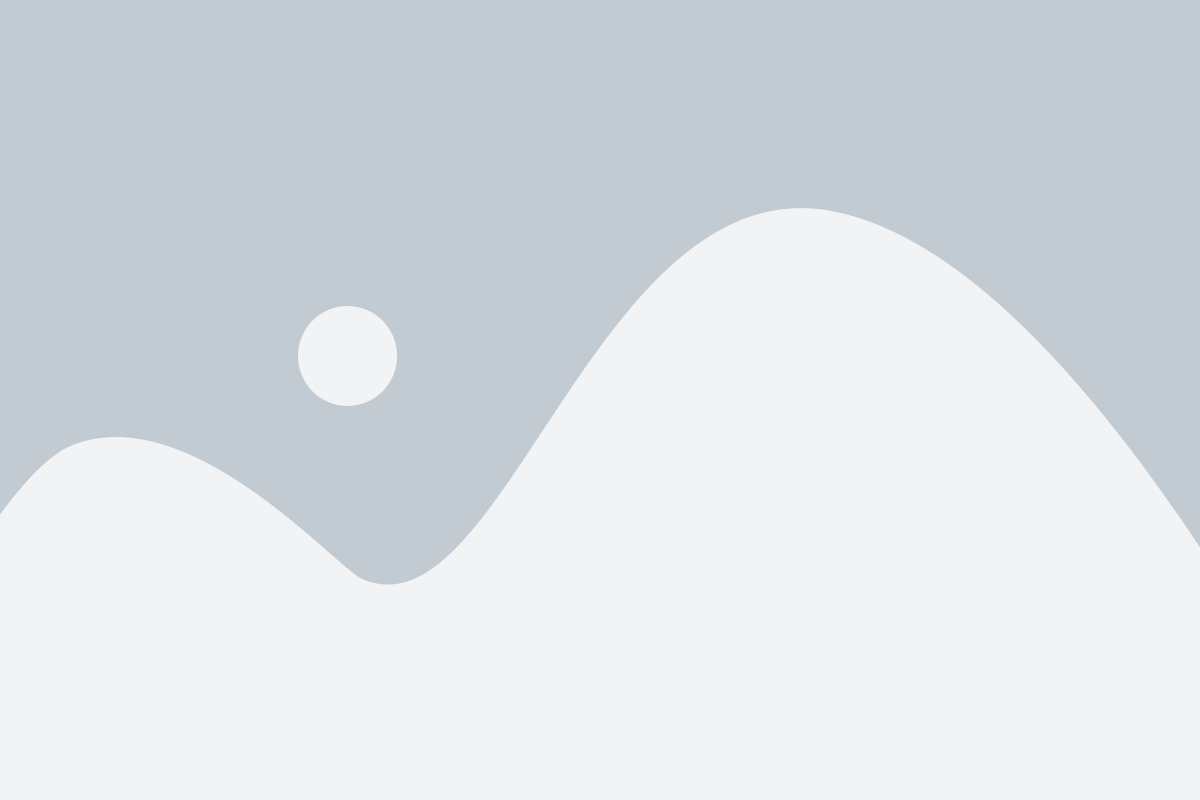
Add Your Heading Text Here
Lorem ipsum dolor sit amet, consectetur adipiscing elit. Ut elit tellus, luctus nec ullamcorper mattis, pulvinar dapibus leo.
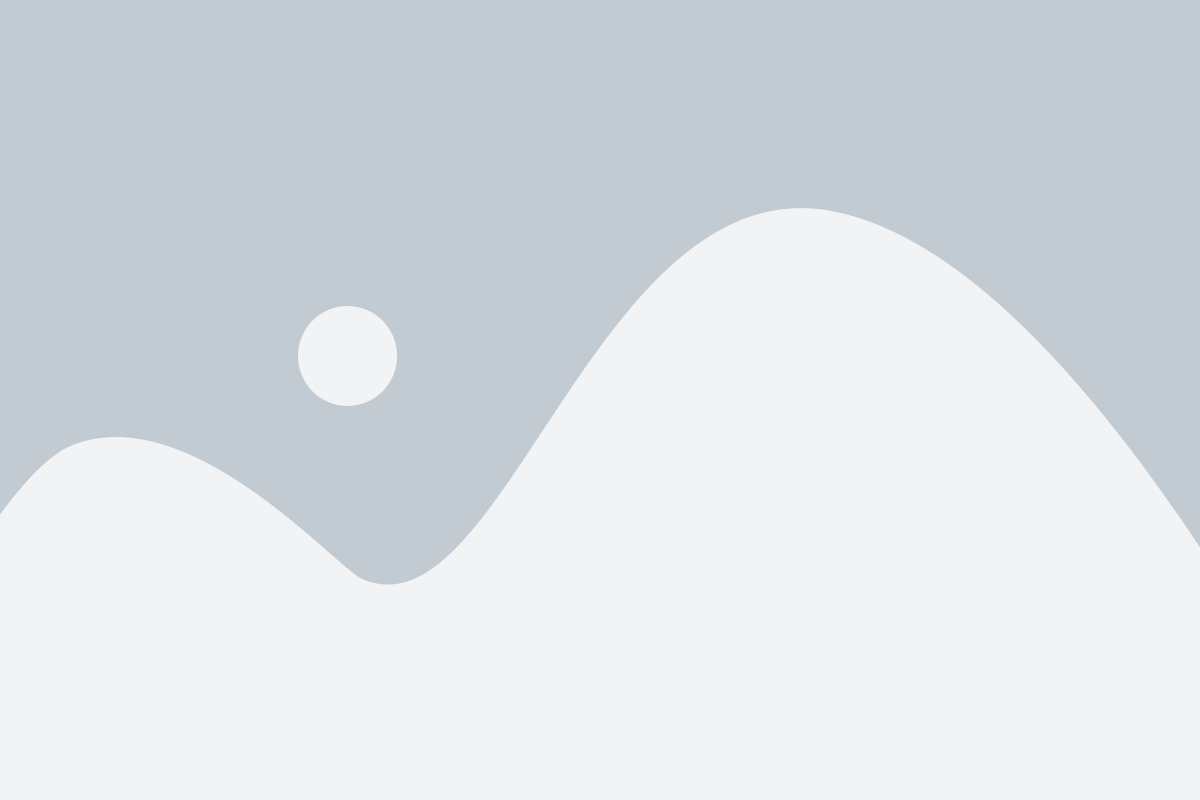
Add Your Heading Text Here
Lorem ipsum dolor sit amet, consectetur adipiscing elit. Ut elit tellus, luctus nec ullamcorper mattis, pulvinar dapibus leo.
FAQ
Listed below are the types of technical questions you may have about top case packers.
Working Principles of XINTU Top Load Case Packer
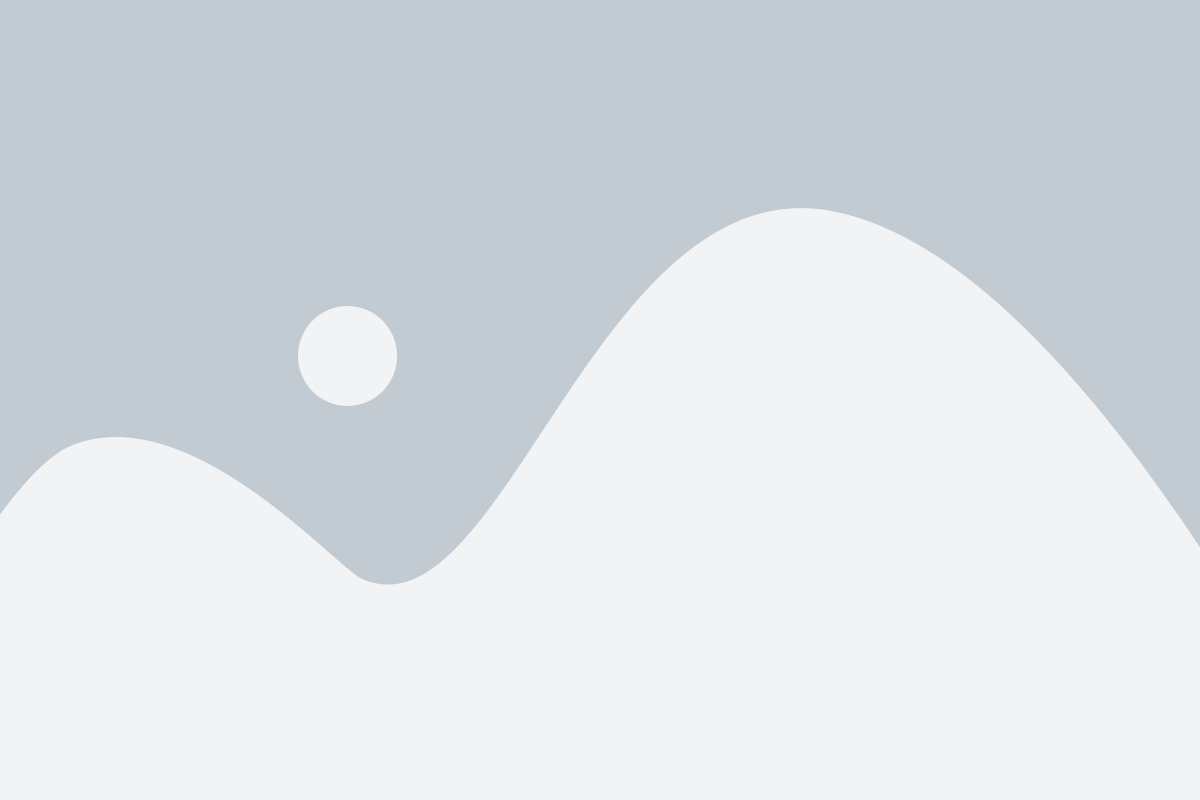
Efficient packaging is critical for maintaining productivity and product quality in high-volume manufacturing. The XINTU top load case packer integrates advanced technology to streamline your packaging process, ensuring reliable, high-speed performance. This machine combines precision, speed, and flexibility, making it ideal for various industries. The key working principles of the XINTU top load case packer include:
Product Orientation System
Your packaging process begins with the product orientation system. This system ensures each product is correctly aligned for packing. Using advanced sensors and conveyors, the system detects and adjusts the position of each item, ensuring they are ready for accurate placement. Proper orientation is crucial for maintaining packing efficiency and preventing damage.
Product Grouping System
Next, your products are grouped into the desired quantities for packing. The grouping system uses synchronized conveyors and automated gates to organize products into neat, uniform groups. This precise arrangement ensures that each case receives the correct number of items, optimizing packing speed and consistency.
Case Loading System
The core of the XINTU top load case packaging system is the case loading system. Using robotic arms equipped with vacuum grippers, this system lifts and places grouped products into open cases. The robotic arms operate with high precision, ensuring each product is securely placed without damage. The automated system allows for high-speed operation, enhancing your overall productivity.
Case Sealing System
Once the products are loaded, your cases are sealed to ensure secure transport. The case sealing system applies tape or adhesive to close the top of each case. The sealing mechanism is carefully calibrated to provide consistent and reliable seals, maintaining the integrity of your packaging during transit.
Additional Features and Benefits
The XINTU top load case packaging machine is versatile, accommodating various product sizes and packaging formats. The machine features user-friendly HMI controls, enabling easy operation and quick adjustments. Real-time monitoring ensures optimal performance and allows for immediate troubleshooting. Built with durable materials, the machine ensures longevity and minimal maintenance requirements. The automated design significantly reduces labor costs while increasing throughput, making it an excellent choice for large-scale operations.
In summary, the XINTU top load case packing machine is essential for any high-volume packaging line. Its integration of product orientation, grouping, loading, and sealing maximizes efficiency and ensures high-quality packaging. This machine is a valuable asset, providing a compact, efficient, and cost-effective solution for your packaging needs.
Maintenance of XINTU Top Load Case Packer
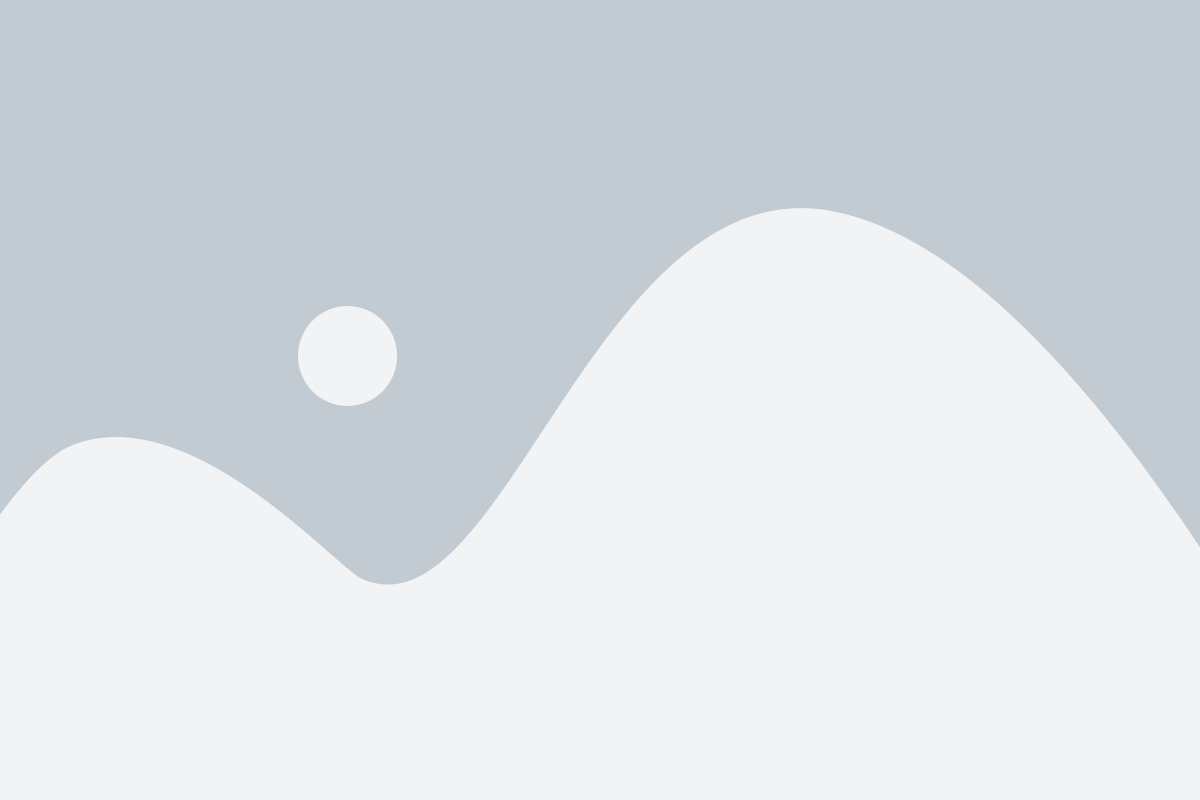
Efficient and high-quality packaging of products requires a well-maintained top load case packer. The XINTU top load case packer integrates advanced features for optimal performance. To keep your machine running smoothly and ensure product quality, a comprehensive maintenance program is essential. Here are the key maintenance requirements for the XINTU top load case packer:
Cleaning and Sanitization
Regular Cleaning:
Regularly clean the packing system with approved solutions to remove any residues or contaminants.
Sanitization: Use approved sanitizing agents to thoroughly sanitize the packing components, ensuring a high level of hygiene.
Cleaning Schedule: Implement a comprehensive cleaning schedule, including daily, weekly, and monthly tasks to maintain consistent cleanliness.
Environmental Compliance: Ensure proper disposal or treatment of used cleaning and sanitizing solutions to comply with environmental regulations.
Surface Cleaning: Clean all machine surfaces before operation and apply clean lubricating oil to each moving part.
Lubrication
Identify Moving Parts: Identify all moving parts that require lubrication, such as bearings, gears, and actuators.
Use Recommended Lubricants: Use lubricants specified by the manufacturer to ensure compatibility and optimal performance.
Lubrication Schedule: Establish a lubrication schedule based on operating hours and manufacturer recommendations.
Monitor Levels: Regularly check lubricant levels and replenish as needed to prevent wear and tear.
Frequent Oil Addition: Frequently add oil to the machine’s lubrication system, maintaining the correct amount to ensure smooth operation.
Preventive Maintenance
Maintenance Plan: Develop a preventive maintenance plan that includes regular inspections, component replacements, and calibrations.
Inspect Components: Regularly inspect and replace worn or damaged components, such as seals, valves, and sensors, to prevent breakdowns.
Calibrate Systems: Calibrate sensors and control systems to ensure accurate and consistent performance.
Check Mechanisms: Regularly check the proper functioning of the product handling and packing mechanisms, making adjustments as needed.
Spare Parts Inventory: Maintain a stock of spare parts to minimize downtime during maintenance or repairs.
Filter Cleaning: Regularly clean filters to ensure the system operates efficiently.
Operator Training
Comprehensive Training: Provide comprehensive training to operators on the proper operation, troubleshooting, and maintenance of the case packer.
Importance of Maintenance: Ensure operators understand the importance of following maintenance protocols and reporting any issues.
Ongoing Training: Implement a training program that includes initial onboarding and ongoing refresher sessions.
Pre-Operation Checks: Train operators to perform pre-operation checks to identify and resolve any issues before starting the machine.
Documentation and Record-keeping
Maintenance Logs: Maintain detailed maintenance logs, including dates, tasks performed, parts replaced, and any issues encountered.
Preventive Activities Records: Keep records of all preventive maintenance activities, repairs, and machine performance data.
Tracking System: Establish a system for tracking maintenance schedules, inventory of spare parts, and service history.
Review Records: Regularly review maintenance records to identify trends and plan for future upgrades or replacements.
Specific Maintenance Tasks
Drain Water: Frequently drain any accumulated water in the system to prevent damage.
Replace Seal Rings: Replace seal rings on the packing components when worn out to ensure optimal performance.
Stainless Steel Maintenance: Keep the stainless steel body clean and smooth, avoiding any scratches or damage.
Filter Elements: Clean or replace filter elements as needed to maintain the efficiency of the system.
Valve and Tank Inspection: Regularly inspect and maintain valves and tanks to ensure they function correctly.
By adhering to these comprehensive maintenance practices, your XINTU top load case packer can maintain optimal performance, ensure product quality, and minimize the risk of unplanned downtime. Regular maintenance not only extends the life of your equipment but also contributes to the overall efficiency and success of your packaging operation.
The key components and technologies used in the XINTU top load case packer for efficient, high-quality packaging include:
Product Handling
- Advanced Grippers: Securely handle various product types, ensuring precise placement in cartons.
- Adjustable Collators: Organize products into desired pack patterns, ready for loading.
- Durable stainless steel construction: Ensures longevity and hygiene.
Case Packing System
- Servo-Driven Pick-and-Place Systems: Provide consistent and accurate placement of products into cases.
- Vacuum Grippers: Handle delicate products without damage, ensuring product integrity.
- Quick Changeover Configurations: Meet specialized packing requirements efficiently.
- Easy Clean-in-Place (CIP) and Steam-in-Place (SIP) capabilities: Facilitate maintenance and ensure hygiene.
- Stainless steel construction: Ensures corrosion resistance and durability throughout the packing process.
- Integrated Storage Hoppers: Minimize environmental contamination during packing.
Case Sealing System
- Precision Sealing Heads: Ensure reliable sealing with consistent pressure and alignment.
- Adjustable Sealing Parameters: Accommodate various case types and sealing methods.
- User-Friendly Control Panel: Allows easy adjustments and monitoring.
- Robust stainless steel and tempered glass construction: Ensures safety and longevity of the sealing system.
Packaging Equipment and Machinery
- Automated Packing Lines: Ensure efficient product handling and packing.
- Integration with Conveyor Systems: Provides seamless product transport.
- Quality Control Systems: Ensure consistent packaging quality throughout the process.
- Flexible Packaging Machines: Ideal for businesses of all sizes.
- Industrial-Scale Packaging Systems: Suitable for large-scale manufacturing operations.
Overall, the key technologies in modern XINTU top load case packers emphasize sanitation, precision, and reliability. The use of stainless steel components, automated controls, and specialized handling and sealing mechanisms ensures high-quality packaging. These advanced packing machines cater to various production scales, from small businesses to large-scale manufacturing plants.
Here are the essential steps for installing a top load case packer, considering layout, integration, electrical safety, hygiene, and commissioning:
Layout and Integration
- Materials: Use food-grade, corrosion-resistant materials such as stainless steel for all machine parts. These materials ensure the longevity and safety of the case packer.
- Sizing: Size the machine to fit your production line's space requirements, ensuring efficient operation.
- Isolation Valves: Install isolation valves for maintenance and servicing without disrupting the entire system.
- Layout: Minimize bends and dead-legs in the layout to maintain optimal product flow and prevent contamination risks.
- Drainage: Integrate proper drainage and spill containment systems to manage any potential leaks or spills effectively.
Electrical and Mechanical Safety
- Grounding and Protection: Ensure proper electrical grounding and cabinet protection to prevent any electrical hazards.
- Safety Standards: Comply with international safety standards for mechanical and electrical equipment.
- Safety Features: Install guarding, interlocks, and emergency stop buttons for operator safety.
Hygiene and Sanitation
- Installation Environment: Install the machine in a clean, well-ventilated environment to maintain high hygiene standards.
- Materials: Use materials that can be easily cleaned and sanitized for product contact surfaces.
- Cleaning Protocols: Establish thorough cleaning and sanitization protocols for the machine and accessories to maintain consistent hygiene.
Commissioning and Testing
- Comprehensive Testing: Perform comprehensive commissioning and testing of the installed machine before production start.
- Performance Validation: Validate the machine’s performance parameters against the manufacturer’s specifications.
- Operator Training: Train operators on the machine’s usage, maintenance, and safety protocols.
By following these key steps, you can ensure the top load case packer is installed safely, efficiently, and in compliance with relevant standards and regulations. Proper installation and maintenance of the machine are critical to the success of any packaging operation.
Yes, the XINTU top load case packer can handle different product sizes and shapes without the need for additional equipment. The key features that enable this versatility are:
Accommodates Various Product Sizes
The machine can handle a range of product sizes through the use of adjustable grippers. This flexibility makes it ideal for different production needs, whether you are packing small or large items.
Efficient Product Orientation
The product orientation system ensures effective handling by moving in synchronization with the products. It completes a full 360-degree adjustment for thorough alignment, ensuring that every product is correctly positioned for packing.
Seamless Product Grouping
The product grouping system operates seamlessly, allowing each section to move in tandem with the products. This ensures precise and efficient grouping of various items.
Smooth Case Loading
The case loader facilitates smooth loading, with products being automatically arranged and conveyed to the packing station. This automation ensures that each case is securely packed, maintaining the quality and safety of the product.
Integrated Versatility
The top load case packer is designed to streamline the packing process by integrating product handling, grouping, and loading functions into a single unit. This automation reduces the need for manual intervention and enhances efficiency, making it suitable for various production environments.
By incorporating these advanced features, the XINTU top load case packer offers a versatile and efficient solution for handling different product sizes and shapes, making it a valuable asset in any packaging system. Whether you’re working with food products, personal care items, or industrial components, this system ensures optimal performance and flexibility.
When discussing top load case packers specifically for packaging various products, there are several types of machines. Here are the main types:
Gravity Feed Packers
Gravity feed packers use gravity to move products into cases. The products flow from a hopper into the cases due to gravity, making them suitable for uniform items like boxes or cans.
Servo-Driven Packers
Servo-driven packers are designed to handle products to a consistent level by using servo motors. They are ideal for various product types, ensuring each case is uniformly packed.
Robotic Packers
Robotic packers use robotic arms to place products into cases. They are versatile and can handle various product sizes and shapes, offering flexibility and precision.
Timed Flow Packers
Timed flow packers control the amount of product dispensed into each case by timing the flow. They are suitable for free-flowing items, providing consistent and accurate packing.
Volumetric Packers
Volumetric packers measure the volume of products dispensed into each case, ensuring precise packing. They are commonly used for various low-density items.
These types of packing machines are designed to handle different product types and ensure efficient and accurate packing. Whether you are setting up a packaging plant or upgrading your existing equipment, understanding these options can help you choose the right machine for your needs.
A top load case packer is specifically designed for non-carbonated and various packaged products, including boxed goods, bagged items, and other non-gaseous products. These machines are highly versatile and efficient for packing large quantities of items. The machine’s ability to handle various product sizes and shapes extends its utility to a wide range of packaging needs.
The top load case packer system integrates handling, grouping, and loading processes into one streamlined operation, ensuring that each step is meticulously performed to maintain product integrity and quality. This integration is crucial for maintaining efficiency and operational standards. For businesses packing a variety of products, the top load case packer’s adaptability makes it an essential piece of equipment in modern production lines. Additionally, the machine can also be referred to as a case packer or packing equipment, demonstrating its broad applicability in the packaging industry.
The orientation process in a top load case packer is critical for ensuring the correct positioning of products before they are packed. The process typically begins with the products being conveyed to the orientation station, where they are adjusted to the required position. These adjustments ensure that every product is correctly aligned, removing any misplacement or orientation issues.
This step is crucial for maintaining the overall quality and efficiency of the packaging process. Some advanced machines may also use a combination of mechanical and automated orientation systems to ensure optimal handling. Additionally, the orientation system can be adjusted to accommodate different product types, making the process more versatile and efficient. By ensuring that each product is properly oriented, the top load case packer helps maintain high standards in the packaging process.
Using a top load case packer offers numerous benefits, including improved efficiency, consistency, and cost savings. Firstly, integrating handling, grouping, and loading into a single machine streamlines the production process, reducing the time and labor required to move products between different stages. This leads to faster production times and lower operational costs.
Secondly, these machines are designed to maintain high consistency standards. The automated processes minimize human contact with the products, reducing the risk of contamination. This is especially important for products where consistency and integrity are key selling points. Additionally, the machines are often equipped with features for precise handling and placement, further ensuring the product’s quality.
Lastly, using a top load case packer can be more cost-effective in the long run. By combining multiple processes into one piece of equipment, businesses save on the cost of purchasing, maintaining, and operating multiple machines. This integration also means less space is required on the production floor, allowing for a more compact and efficient setup. Overall, the top load case packer is a valuable investment for companies packaging various products.
The packing process in a top load case packer is designed to ensure high accuracy and consistency, which are crucial for maintaining product quality and customer satisfaction. The machine typically uses advanced technologies such as sensors and control systems to precisely measure the placement of products. These sensors can detect even minor deviations in placement, ensuring that each product is correctly positioned.
The packing heads are usually equipped with mechanisms that are designed to prevent misalignment, further enhancing accuracy. The machine’s control system monitors and adjusts the packing speed and placement in real-time, compensating for any variations in product size or shape. This level of precision helps maintain uniformity across all cases, which is essential for branding and regulatory compliance.
Consistency is also achieved through the machine’s ability to maintain a steady packing rate during the process. The use of high-quality materials and components ensures that the machine operates smoothly and reliably over extended periods. By ensuring that each case is packed accurately and consistently, the top load case packer helps build trust with consumers and enhances the overall efficiency of the production line.
A top load case packer offers various sealing methods to ensure the secure sealing of cases after they have been packed. The most common sealing methods include tape sealing, adhesive sealing, and heat sealing. Each method is designed to cater to different types of packaging and ensure a tight seal to prevent leaks and contamination.
Tape Sealing is widely used for cases with flaps. The machine’s sealing head applies a strip of tape to the flaps, ensuring a secure fit. This method is reliable and provides a tamper-evident seal, which is important for product safety.
Adhesive Sealing is used for cases that require a stronger bond. The machine applies adhesive to the flaps and presses them together with sufficient force to ensure a secure seal. This method is quick and suitable for high-speed production lines.
Heat Sealing is typically used for cases made of heat-sensitive materials. The machine applies heat to seal the flaps, ensuring a tight bond. This method is often used for cases that require a more durable seal.
Each sealing method is integrated into the top load case packer, allowing for seamless transitions between handling, packing, and sealing. The choice of sealing method depends on the type of product and case being used, ensuring flexibility and efficiency in the packaging process.
Maintaining hygiene and safety in a top load case packer is crucial for producing high-quality packaged products. Regular cleaning and sanitization of the machine’s components, including the handling, grouping, and packing stations, are essential to prevent contamination. Using food-grade cleaning agents and following the manufacturer’s guidelines for cleaning procedures helps ensure the machine remains hygienic.
Implementing proper maintenance schedules is also vital. Regular inspection of the machine’s parts, such as seals, gaskets, and grippers, can help identify wear and tear early, preventing potential contamination sources. Ensuring that the machine is operating at the correct settings is important for maintaining product safety and quality.
Staff training is another critical aspect of maintaining hygiene and safety. Operators should be trained on the correct cleaning procedures, handling of chemicals, and safe operation of the machine. Personal protective equipment (PPE) should be worn at all times to minimize the risk of contamination from human contact.
In addition to these practices, using automated systems for monitoring and controlling the machine’s operations can enhance hygiene and safety. Automated systems can detect and alert operators to potential issues, allowing for quick intervention and reducing the risk of contamination. By following these practices, businesses can ensure their top load case packers produce safe and high-quality packaged products.
A high-quality top load case packer is characterized by several key features that ensure efficient, reliable, and hygienic operation. One of the most important features is the integration of handling, grouping, and packing processes into a single machine, which streamlines production and reduces the need for multiple pieces of equipment.
Advanced automation and control systems are also crucial. These systems allow for precise control over the packing placement, sealing pressure, and handling cycles, ensuring consistency and accuracy in every case. High-quality machines are often equipped with user-friendly interfaces that make it easy for operators to monitor and adjust settings as needed.
Durable construction materials are another important feature. High-quality machines are typically made from stainless steel and other corrosion-resistant materials, which ensure longevity and maintain hygiene standards. The use of high-quality components, such as reliable sensors and robust packing mechanisms, also contributes to the machine’s durability and performance.
Flexibility and adaptability are additional key features. A high-quality top load case packer can accommodate different product sizes and shapes, making it suitable for a wide range of production needs. The machine should also be easy to clean and maintain, with components that can be quickly disassembled and reassembled for thorough cleaning.
By incorporating these key features, a high-quality top load case packer can provide reliable, efficient, and hygienic operation, making it an essential asset for any packaging facility.
Choosing the right top load case packer for your production needs involves several important considerations. The first step is to determine the specific requirements of your production line, such as the types of products to be packed, the desired production capacity, and the types of cases to be used. This will help you narrow down the options and find a machine that meets your specific needs.
Production capacity is a critical factor to consider. Different models of top load case packers have varying capacities, so it’s important to choose a machine that can handle your expected production volume. Consider both your current production needs and any potential future growth to ensure the machine can scale with your business.
The types of products and cases you plan to use are also important. Ensure that the machine you choose can accommodate the sizes and shapes of your products and the types of cases you use. Some machines offer greater flexibility and can handle a wider range of product types, which can be beneficial if you plan to produce multiple products.
Additionally, consider the level of automation and control features you need. Advanced automation can improve efficiency and consistency, but it may also come with a higher cost. Evaluate whether the benefits of increased automation justify the investment for your specific operation. User-friendly controls and interfaces are also important, as they can simplify operation and reduce the training required for your staff.
Durability and maintenance requirements are other key factors. Look for machines made from high-quality materials, such as stainless steel, which offer resistance to corrosion and wear. Machines with easily accessible components can simplify maintenance and reduce downtime, keeping your production line running smoothly.
Lastly, consider the manufacturer’s reputation and the level of customer support they provide. A reliable manufacturer with a good track record can offer peace of mind, knowing that your machine is backed by solid support and service. Checking reviews and seeking recommendations from industry peers can also help in making an informed decision.
By carefully considering these factors, you can choose a top load case packer that meets your production needs, ensuring efficiency, reliability, and high-quality output.
The production capacity of top load case packers can vary significantly depending on the model and manufacturer. Entry-level models may offer a capacity of around 1,000 to 3,000 cases per hour, making them suitable for small to medium-sized operations. These machines are often more compact and cost-effective, providing a good starting point for businesses new to the industry or those with lower production needs.
Mid-range models typically have a capacity of 5,000 to 12,000 cases per hour. These machines are designed for medium to large-sized operations and offer a balance of performance, flexibility, and cost. They often come with additional features such as advanced automation, improved handling and packing accuracy, and higher speed sealing systems.
High-end models can handle capacities of 15,000 to over 36,000 cases per hour. These machines are suited for large-scale production facilities and are equipped with the latest technologies to ensure maximum efficiency and precision. High-end models often feature sophisticated control systems, enhanced durability, and the ability to handle a wide range of product sizes and shapes.
When selecting a machine, it’s important to match the production capacity to your business’s current and anticipated future needs. Overestimating capacity can lead to unnecessary expenses, while underestimating it can result in production bottlenecks. Consulting with the manufacturer or a specialist can help determine the best model for your specific requirements.
Optimizing the efficiency of a top load case packer involves several strategies aimed at maximizing output while minimizing downtime and waste. One of the key steps is to ensure that the machine is properly maintained. Regular maintenance, including cleaning and inspecting components for wear and tear, can prevent unexpected breakdowns and keep the machine running smoothly.
Using high-quality products and cases can also enhance efficiency. Inferior materials can cause jams or malfunctions, slowing down the production process. Ensuring that all materials meet the machine’s specifications can reduce the likelihood of such issues.
Training staff to operate the machine correctly is another crucial factor. Well-trained operators can identify and resolve minor issues before they escalate, adjust settings for optimal performance, and perform routine maintenance tasks effectively. Providing comprehensive training and refresher courses can help maintain high levels of proficiency among the workforce.
Implementing automated monitoring systems can further boost efficiency. These systems can provide real-time data on machine performance, alerting operators to any deviations from optimal conditions. By addressing these issues promptly, you can minimize downtime and maintain a consistent production rate.
Additionally, optimizing the layout of the production line can reduce bottlenecks and improve workflow. Ensuring that the machine is integrated seamlessly with other equipment and that there is sufficient space for operations and maintenance can enhance overall efficiency.
By focusing on these areas, you can optimize the efficiency of your top load case packer, leading to higher productivity and lower operational costs.
Despite their efficiency, top load case packers can encounter various issues that may disrupt production. One common problem is inconsistent packing placement. This can be caused by incorrect settings, worn-out packing heads, or blockages in the handling system. To troubleshoot, ensure that the machine is calibrated correctly, inspect and clean the heads, and check for any obstructions in the system.
Another frequent issue is case jams. Jams can occur if cases are not aligned properly on the conveyor or if there are variations in case sizes. To address this, regularly check the alignment and condition of the conveyor system and ensure that all cases meet the required specifications. Adjusting the machine settings to better handle variations can also help reduce jams.
Sealing problems, such as loose or misaligned seals, can result from worn-out sealing heads or incorrect pressure settings. Inspect the sealing heads regularly and replace any worn parts. Adjusting the pressure settings to match the case type can ensure a secure fit.
Sanitation and hygiene issues can arise if the machine is not cleaned properly. Regular cleaning and maintenance routines should be established to prevent contamination. Using appropriate cleaning agents and following the manufacturer’s guidelines can help maintain hygiene standards.
If the machine experiences frequent breakdowns or malfunctions, it may indicate underlying issues with the components or the need for more thorough maintenance. Conducting a detailed inspection and working with the manufacturer’s support team can help diagnose and resolve these problems.
By understanding and addressing these common issues, you can ensure that your top load case packer operates efficiently and reliably, minimizing downtime and maintaining high production standards.
Cleaning and sanitizing a top load case packer is crucial for maintaining product quality and safety. The process involves several steps to ensure that all components are thoroughly cleaned and free from contaminants.
Start by disconnecting the machine from the power supply to ensure safety. Remove any residual products from the system by running the machine in a rinse cycle with clean water. This helps flush out any remaining product from the handling lines and heads.
Disassemble the machine parts that come into contact with the products, such as the handling heads, valves, and conveyors. Soak these parts in a solution of warm water and food-grade detergent to break down any residues. Use brushes and cleaning tools to scrub away any stubborn deposits.
Rinse all parts thoroughly with clean water to remove any soap residue. Sanitizing the parts is the next step, which can be done using a food-grade sanitizing solution. Follow the manufacturer’s instructions for the correct dilution and contact time to ensure effective sanitation.
Reassemble the machine and run another rinse cycle with clean water to ensure that no cleaning agents remain in the system. Inspect the machine to ensure all parts are properly reassembled and secure.
Regular cleaning and sanitization should be part of your maintenance schedule. Depending on the production volume and the type of products being packed, cleaning may be required daily or weekly. Following these steps helps maintain high hygiene standards and prevents contamination, ensuring the safety and quality of your packaged products.
Top load case packers are equipped with various safety features to protect both operators and the products being packed. One of the primary safety features is the machine’s automated shutdown capability. In the event of a malfunction or if a safety sensor detects an issue, the machine can automatically shut down to prevent accidents and damage.
Safety guards and enclosures are also common features. These prevent operators from coming into contact with moving parts and high-pressure systems, reducing the risk of injury. Emergency stop buttons are strategically placed around the machine, allowing operators to quickly halt operations in case of an emergency.
The machines are often equipped with interlock systems that prevent the machine from operating if a guard or door is open. This ensures that the machine cannot be started accidentally while maintenance or adjustments are being made.
Temperature and pressure sensors are used to monitor critical parameters within the machine. If these parameters exceed safe levels, the machine can shut down or alert the operator, preventing potential hazards such as overheating or overpressure.
Additionally, many machines feature user-friendly interfaces with clear warnings and instructions. These interfaces guide operators through safe operation procedures and alert them to any issues that need attention.
By incorporating these safety features, top load case packers provide a safe working environment for operators while ensuring the integrity of the products being packed.
Integrating a top load case packer into an existing production line requires careful planning and coordination to ensure seamless operation. The first step is to evaluate the current production line layout and identify the optimal location for the new machine. Consider factors such as accessibility, workflow, and space requirements.
Next, assess the compatibility of the new machine with existing equipment. Ensure that the conveyor systems, product handling mechanisms, and control systems can interface smoothly with the new machine. You may need to modify or upgrade certain components to ensure compatibility.
Work with the machine’s manufacturer or a professional integrator to develop a detailed installation plan. This plan should outline the steps required to install the machine, connect it to the existing systems, and test its operation. Ensure that all electrical and mechanical connections meet safety and operational standards.
Training is another critical aspect of integration. Ensure that your staff is trained on the operation, maintenance, and troubleshooting of the new machine. This will help minimize disruptions and ensure a smooth transition.
Conduct thorough testing before fully integrating the machine into your production line. Run test batches to ensure that the machine operates correctly and that there are no issues with product handling, packing, or sealing. Address any problems that arise during testing to ensure smooth operation once the machine is fully integrated.
By following these steps, you can successfully integrate a top load case packer into your existing production line, ensuring it operates efficiently and seamlessly with minimal disruption.
The energy requirements for operating a top load case packer depend on various factors, including the machine’s capacity, design, and the specific processes it integrates. Generally, these machines require a stable electrical supply to power their motors, control systems, and other components.
For small to medium-sized top load case packers, the power consumption typically ranges from 2 to 5 kilowatts (kW). Larger, high-capacity machines may require 10 kW or more. It’s essential to ensure that your facility’s electrical system can handle the machine’s power requirements without overloading.
In addition to electrical power, some top load case packers might require compressed air for certain functions, such as operating pneumatic valves or assisting in product handling. Ensuring a sufficient supply of compressed air at the appropriate pressure is crucial for these machines to function correctly.
Energy efficiency is an important consideration when selecting a top load case packer. Many modern machines are designed with energy-saving features, such as variable frequency drives (VFDs) that adjust motor speed based on real-time operational needs. This can help reduce overall energy consumption and lower operating costs.
To optimize energy use, it’s also important to regularly maintain the machine and ensure it operates under optimal conditions. Efficient operation not only conserves energy but also extends the lifespan of the machine and its components.
Ensuring product consistency with a top load case packer is crucial for maintaining brand reputation and customer satisfaction. The key to achieving consistency lies in precise control over the packing process and rigorous quality checks.
Firstly, calibrate the machine accurately to ensure that each case receives the exact number of products required. This can be achieved by using advanced sensors and control systems that monitor and adjust the placement in real-time. Regular calibration checks should be part of your maintenance routine to ensure ongoing accuracy.
Secondly, maintain a consistent supply of products and cases that meet the required specifications. Variations in product size, shape, or material can affect the packing process and lead to inconsistencies. Ensuring uniformity in packaging materials helps maintain a stable packing operation.
Implementing stringent quality control procedures is also essential. Regularly sample packed cases and conduct checks for product placement, sealing integrity, and overall appearance. Automated inspection systems can be integrated into the production line to provide continuous monitoring and immediate feedback.
Training staff to monitor the packing process and troubleshoot any issues that arise is another critical factor. Skilled operators can quickly identify and address problems, ensuring that the machine runs smoothly and consistently.
By focusing on these areas, you can ensure that your top load case packer produces consistent, high-quality products that meet your customers’ expectations.
Using a top load case packer involves several environmental considerations that can help reduce the overall environmental impact of the production process. One of the primary considerations is material usage. These machines typically use a significant amount of packaging material. Implementing material-saving measures, such as optimizing case sizes and using recyclable materials, can significantly reduce waste.
Energy efficiency is another important factor. Selecting machines with energy-saving features, such as variable frequency drives and energy-efficient motors, can help lower energy consumption and reduce greenhouse gas emissions. Regular maintenance to ensure the machine operates at peak efficiency also contributes to energy savings.
Waste management is a crucial environmental consideration. Minimizing packaging waste by using recyclable or biodegradable materials can reduce the environmental footprint of the production process. Additionally, optimizing the packing process to reduce product spillage and waste can improve overall efficiency and environmental performance.
Many top load case packers are designed with sustainability in mind, incorporating features that reduce energy and material usage. Choosing a machine from a manufacturer committed to sustainable practices can further enhance your environmental credentials.
Finally, consider the lifecycle of the machine itself. Investing in a durable, high-quality machine that requires fewer replacements and repairs can reduce the environmental impact associated with manufacturing and transporting new equipment. Proper disposal and recycling of old machines and components also play a role in environmental sustainability.
By addressing these environmental considerations, you can ensure that your use of a top load case packer is as sustainable and eco-friendly as possible, aligning with broader environmental goals and regulations.
Training staff to operate a top load case packer safely is essential for maintaining a safe work environment and ensuring the efficient operation of the machine. The training process should be comprehensive and ongoing, covering all aspects of machine operation, safety protocols, and maintenance procedures.
Start by providing detailed instruction manuals and safety guidelines from the machine manufacturer. These documents should be used as the foundation for your training program. Ensure that all operators are familiar with the machine’s components, control systems, and emergency procedures.
Hands-on training is crucial for effective learning. Allow operators to practice using the machine under the supervision of experienced personnel. This practical experience helps them become comfortable with the machine’s operations and understand how to respond to various situations.
Safety training should cover the use of personal protective equipment (PPE), such as gloves, safety glasses, and hearing protection. Operators should be aware of the potential hazards associated with the machine and know how to mitigate risks. This includes understanding the importance of keeping guards and safety devices in place and knowing how to use emergency stop buttons.
Regular refresher courses and safety drills can help reinforce safe practices and keep operators up to date with any changes in procedures or equipment. Encouraging a culture of safety where operators feel comfortable reporting issues and suggesting improvements is also beneficial.
By investing in thorough training for your staff, you can ensure the safe and efficient operation of your top load case packer, protecting both your employees and your production process.
Top load case packers have seen several technological advancements that enhance their efficiency, flexibility, and safety. One of the latest developments is the integration of advanced sensors and control systems that provide real-time data on machine performance. These systems allow for precise adjustments and monitoring, ensuring consistent packing quality.
Another significant advancement is the use of robotic arms for product handling. These arms offer greater flexibility and precision, allowing the machine to handle a wider range of product sizes and shapes. Robotic systems can also be programmed for various packing patterns, enhancing the machine’s versatility.
Energy efficiency has also improved with the introduction of variable frequency drives (VFDs) and energy-efficient motors. These features help reduce energy consumption and operating costs, making the machines more environmentally friendly.
The incorporation of automated inspection systems is another key advancement. These systems use cameras and sensors to monitor the packing process, identifying any issues such as misalignment or missing products. Automated inspections help maintain high-quality standards and reduce the need for manual checks.
User-friendly interfaces have become more common, making it easier for operators to control and monitor the machine. Touchscreen displays provide real-time data and allow for quick adjustments, improving overall efficiency.
These technological advancements have made top load case packers more efficient, flexible, and reliable, making them a valuable asset in modern packaging operations.