XINTU’s Robotic Case Packer offers exceptional versatility and efficiency. Designed for a variety of products including food, beverages, pharmaceuticals, and chemicals, this machine ensures precise and high-speed packing. Key features include:
- Automated and flexible case packing
- High-speed operation with consistent accuracy
- Adaptable to different product sizes and shapes
- Reduces labor costs and enhances productivity
Experience seamless integration with XINTU’s advanced Robotic Packaging Machine solutions for reliable and efficient end-of-line packaging.
Main Features
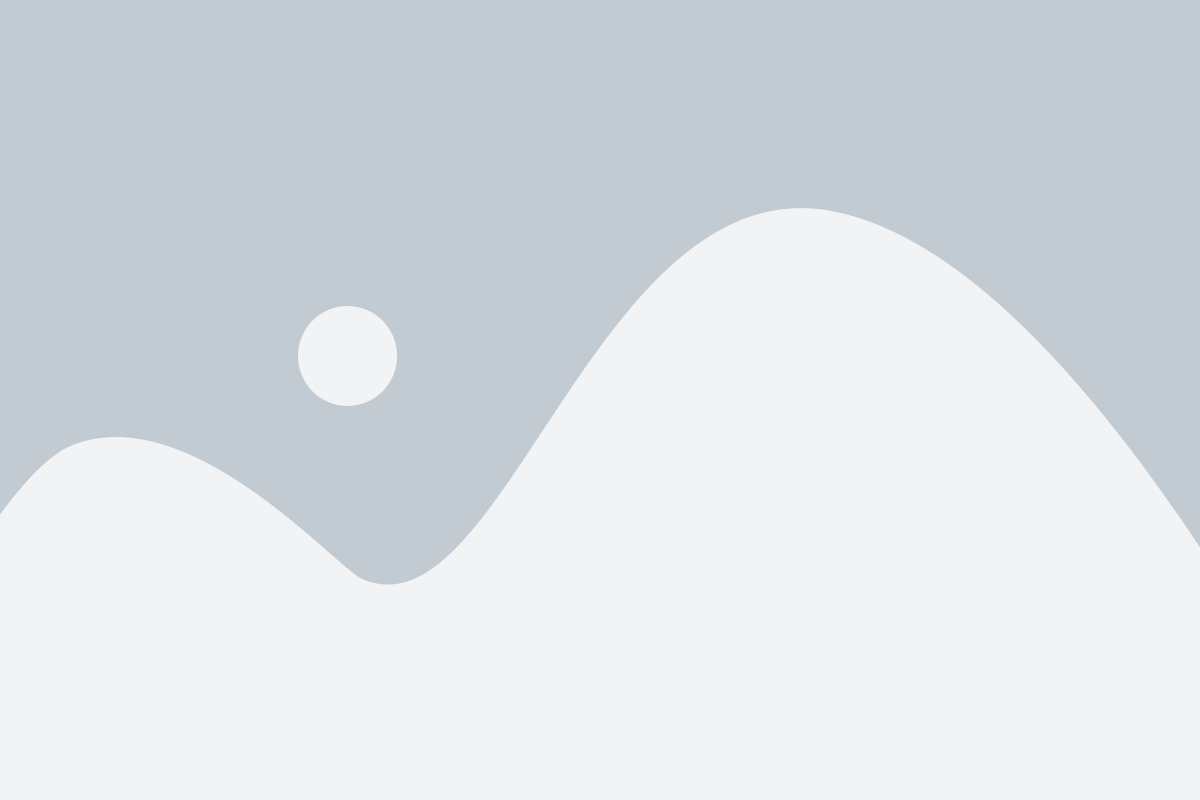
High-Speed Operation
Packs up to 40 cases per minute with precision.
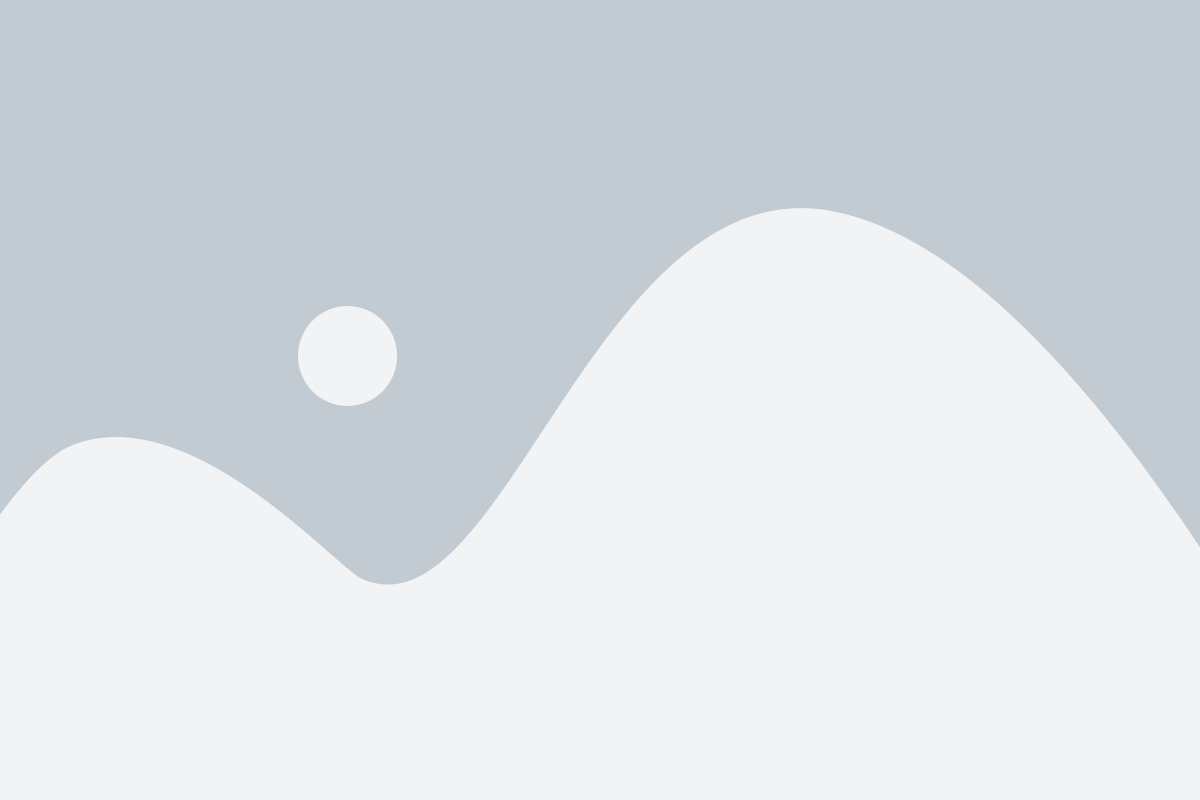
Flexible Handling
Adapts to various product sizes and shapes easily.
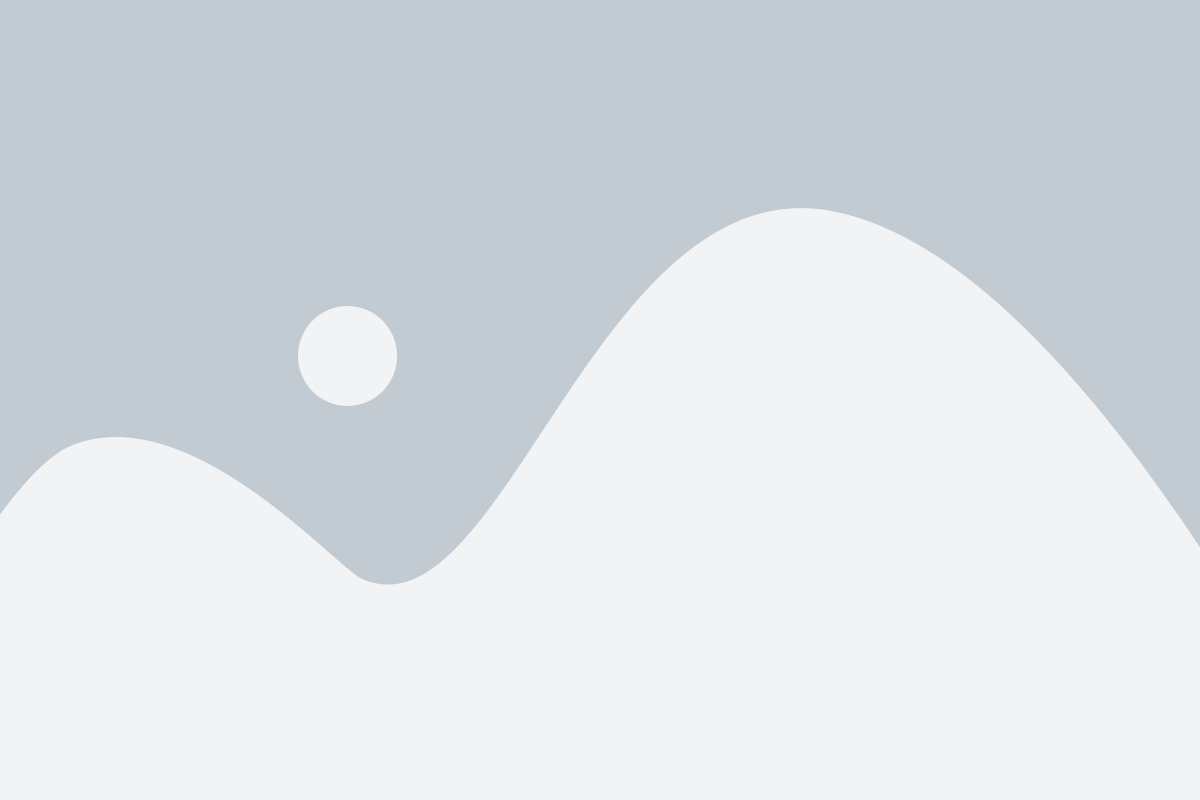
Compact Design
Occupies minimal floor space for efficient use.
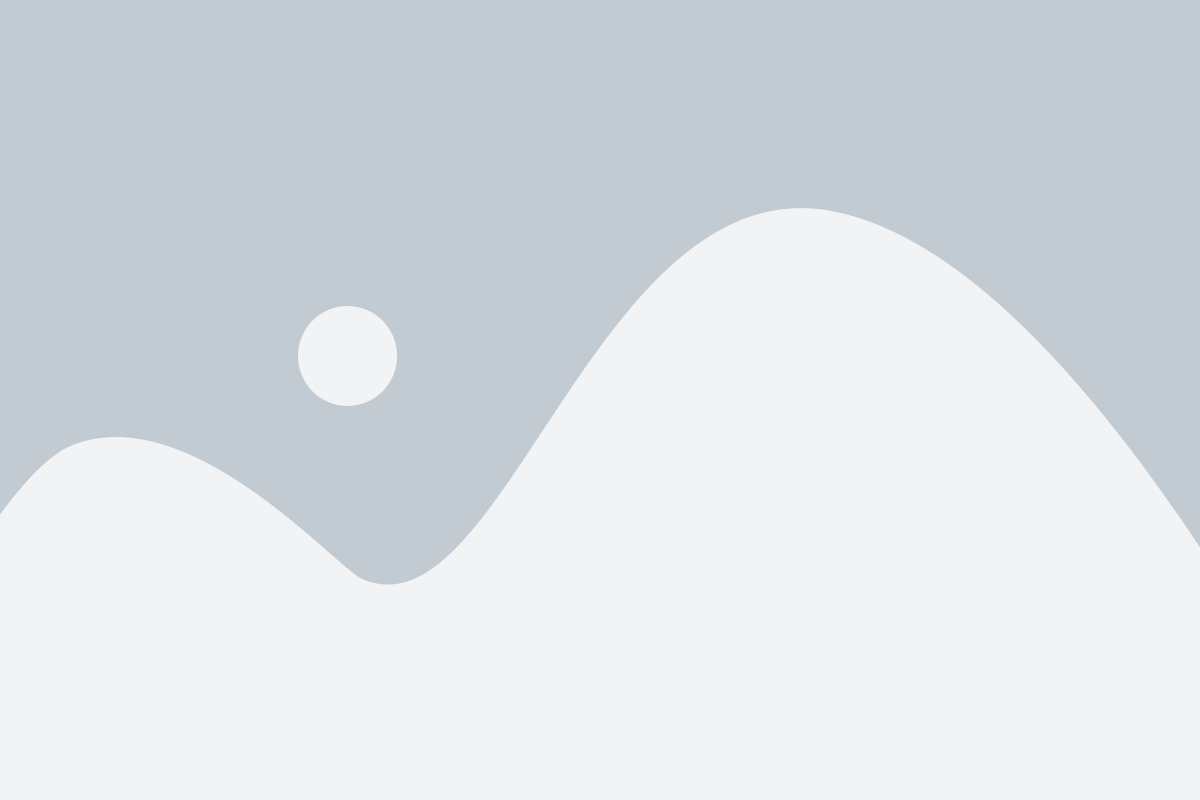
Easy Maintenance
Simple structure with fewer components for low-cost upkeep.
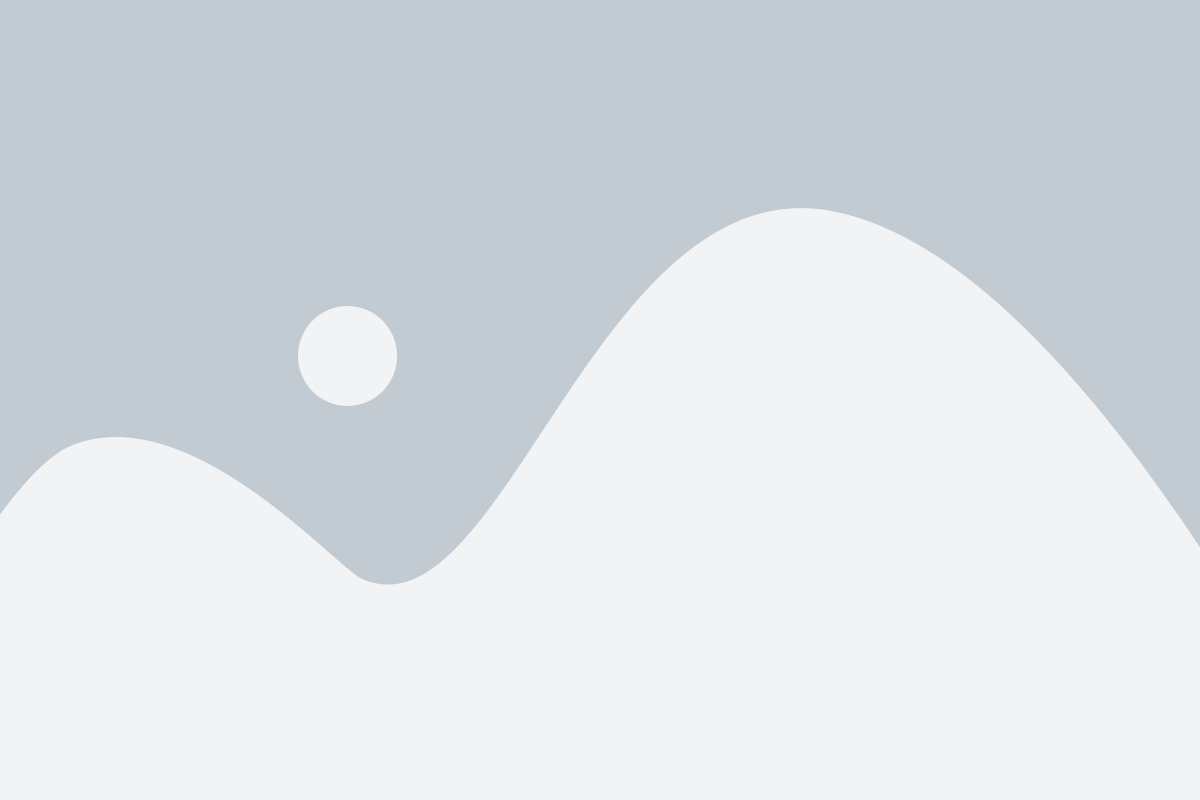
Integrated Vision System
Ensures accurate product identification and placement.
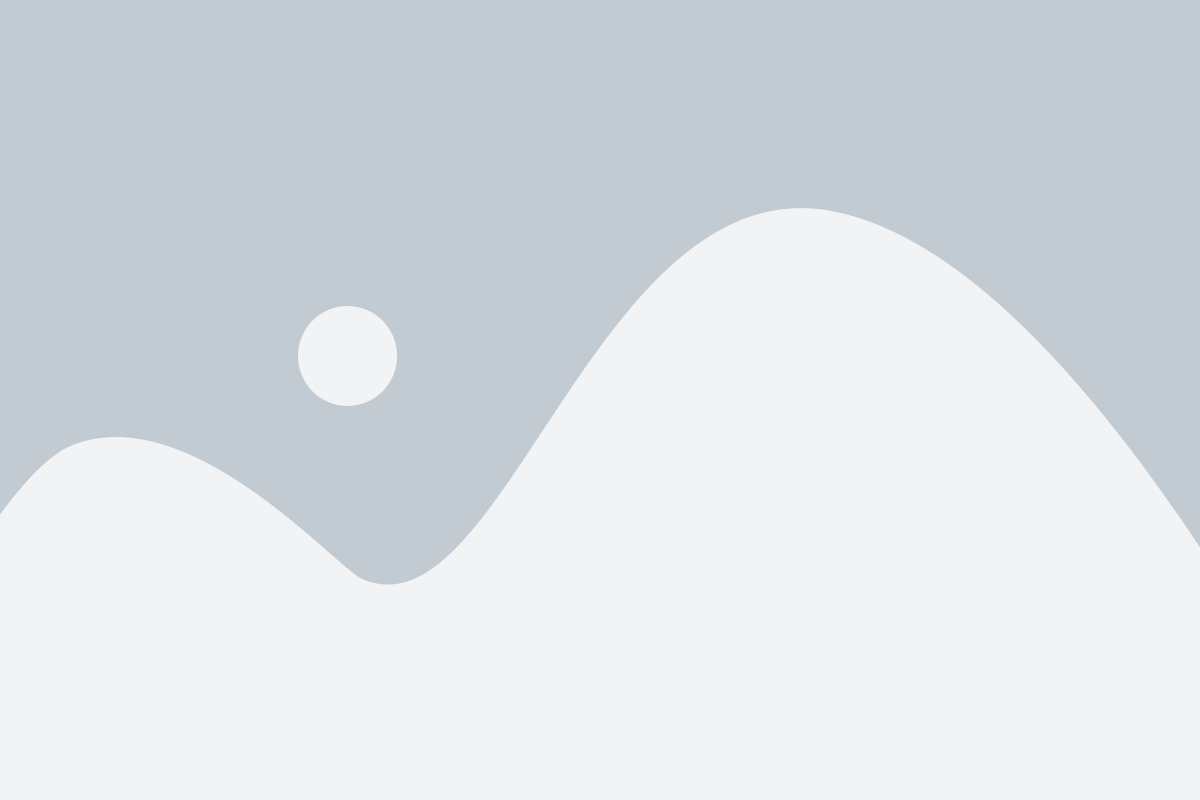
User-Friendly Interface
PLC and touchscreen controls for easy operation and troubleshooting.
ADVANTAGES
Rapid Pace
Packs up to 40 cases per minute.
Precision
Accuracy within ±0.1mm for consistent packing.
Flexibility
Handles loads from 10kg to 250kg.
Quick Switchover
Reduces changeover time to under 5 minutes.
SPECIFICATION
Speed
Up to 40 cases per minute
Up to 2400 cases per hour
Packaging speed vary according to robot pickup method and robot quantity.
Robot Payload& Arm Span
10kg-250kg Work Range: 800mm-3150mm
Choose suitable payload robots based on customer’s packaging neeeds
Operation
Horizontal pickup and place
Changeover
- Flexible Programming:Reprogram for different products in under 15 minutes with intuitive software.
- Quick Size Adaptation: Adjust case size settings in less than 5 minutes via touchscreen.
- Tool-Free Adjustments: Change grippers in under 10 minutes without tools.
Packing Method
Single case each time
Multiple cases each time
Control Method
PLC + touch screen + standard control buttons + signal switch, automatic / manual control modes optional
Power Supply
380V/50Hz or 60Hz(Customized to the industrial voltage of the customer’s plant)
Air Supply
0.5-0.7Mpa,> 600L/min
Package Support
bottled beverages, canned food, boxed food, bagged snacks, shampoo bottles, cleaning spray cans, toothpaste boxes, laundry detergent bottles, canned milk and beer, medicine bottles, nutritional supplement cans, medical equipment boxes, pillow bags, and stand-up pouches of nuts.
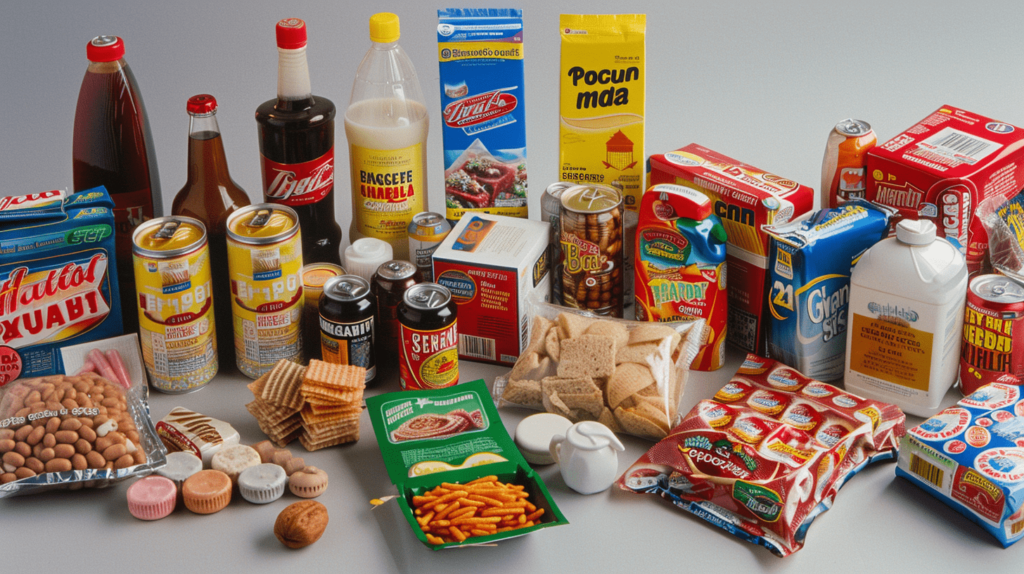
Case Support
RSC cartons and different sizes of cartons
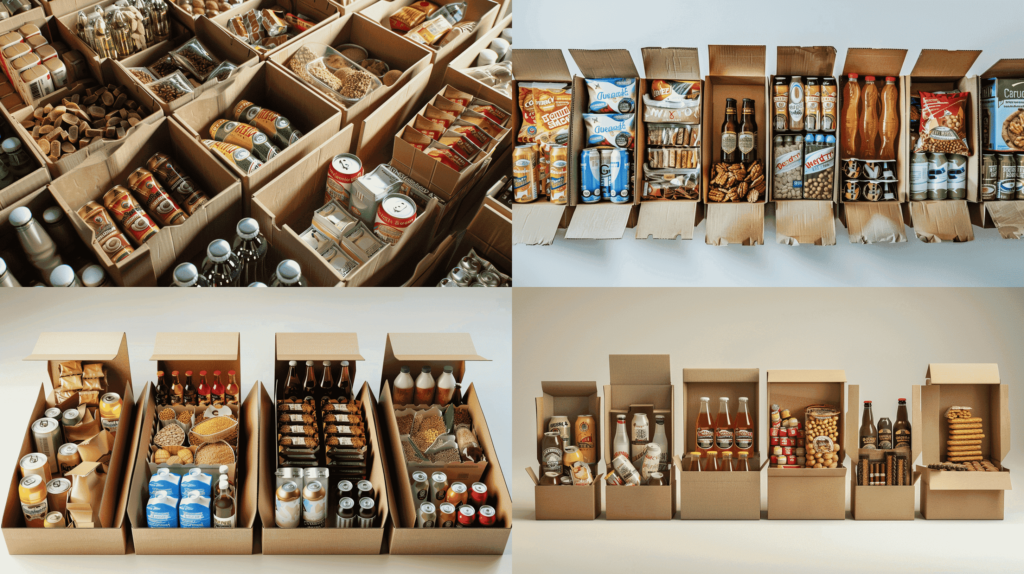
VIDEOS
Robotic Case Packer for Tin Can Food
The XINTU Robotic Case Packer is a high-speed, flexible, and automated packaging machine designed for the efficient packing of tin can food products. This robotic packaging machine can achieve speeds of up to 40 cases per minute, ensuring rapid and precise packing. Ideal for the food industry, it handles a variety of products and case sizes with ease. The end-of-line packaging robot seamlessly integrates into your production line, enhancing productivity and reducing labor costs. This industrial robot packer is perfect for applications requiring high-speed, reliable, and consistent packing performance.
Robotic Case Packer for Bottled Energy Drinks
The XINTU Robotic Case Packer is a high-speed, flexible, and automated packaging machine designed for the efficient packing of tin can food products. This robotic packaging machine can achieve speeds of up to 40 cases per minute, ensuring rapid and precise packing. Ideal for the food industry, it handles a variety of products and case sizes with ease. The end-of-line packaging robot seamlessly integrates into your production line, enhancing productivity and reducing labor costs. This industrial robot packer is perfect for applications requiring high-speed, reliable, and consistent packing performance.
Robotic Case Packer for irregular bagged products
The XINTU Robotic Case Packer for irregular bagged products operates at high speed and ensures precise and efficient packaging. This Automated Case Packer is ideal for irregularly shaped bagged products across various industries, including food, pharmaceuticals, and consumer goods. The Robot Case Packer can handle up to 60 bags per minute, significantly boosting productivity. Designed as a Flexible Case Packer, it seamlessly integrates into your existing production line, providing a robust Robotic Case Packing System. Utilize this High-Speed Robotic Packer to enhance your packaging efficiency and reliability, making it a perfect solution for complex packaging needs.
LAYOUT DRAWINGS
Explore our extensive range of Packaging layout solutions tailored for your project needs.
Layout of Delta Robotic Case Packer
Up to 40 cases per minute robotic case packing machine layout for food&beverage plants,Pharmaceutical factories, and consumer products plants.
RELATED EQUIPMENT
Integrated packaging line solutions
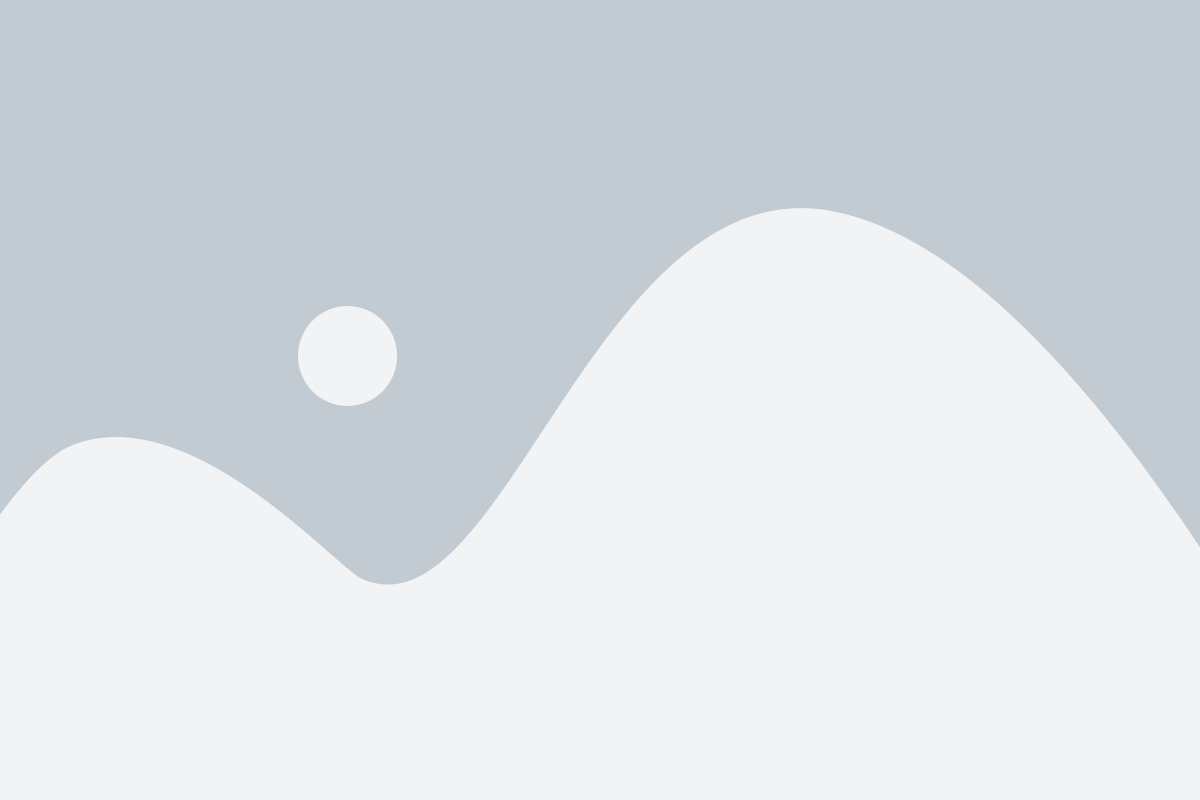
Delta Robot Case Packer
Lorem ipsum dolor sit amet, consectetur adipiscing elit. Ut elit tellus, luctus nec ullamcorper mattis, pulvinar dapibus leo.
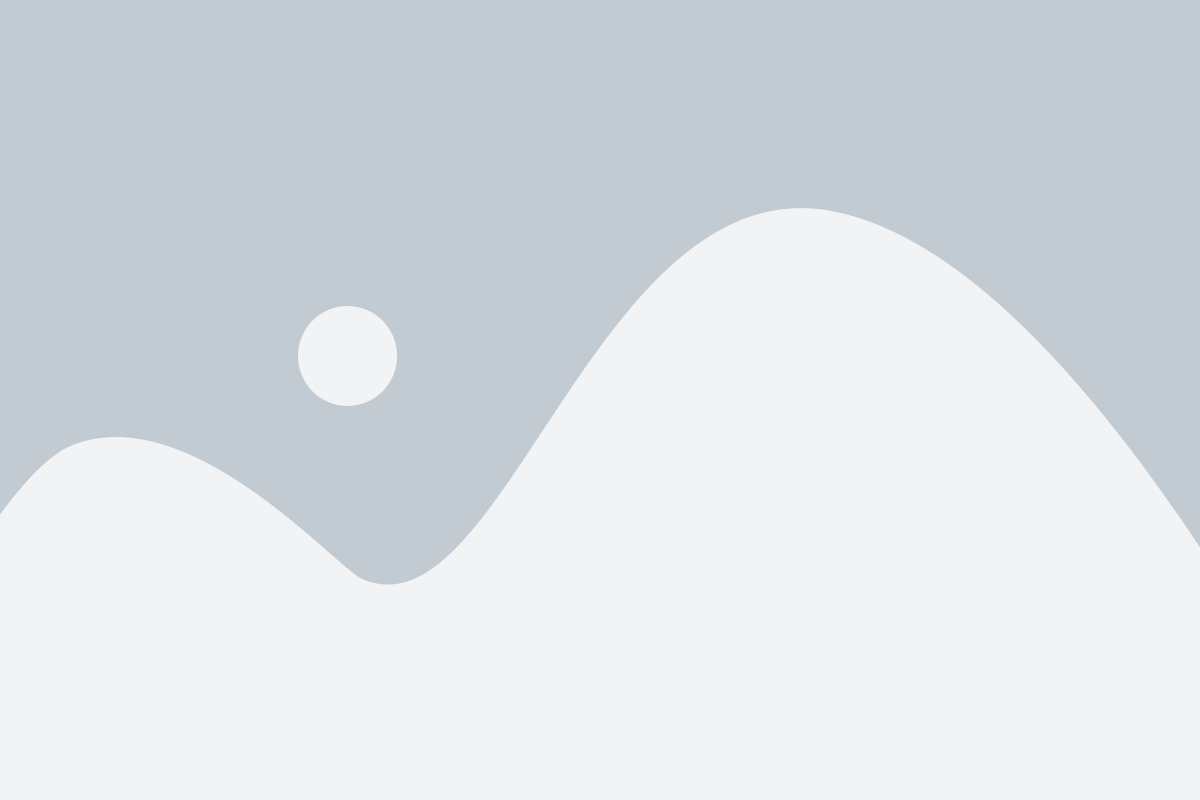
Robotic Arm Palletizer
Lorem ipsum dolor sit amet, consectetur adipiscing elit. Ut elit tellus, luctus nec ullamcorper mattis, pulvinar dapibus leo.
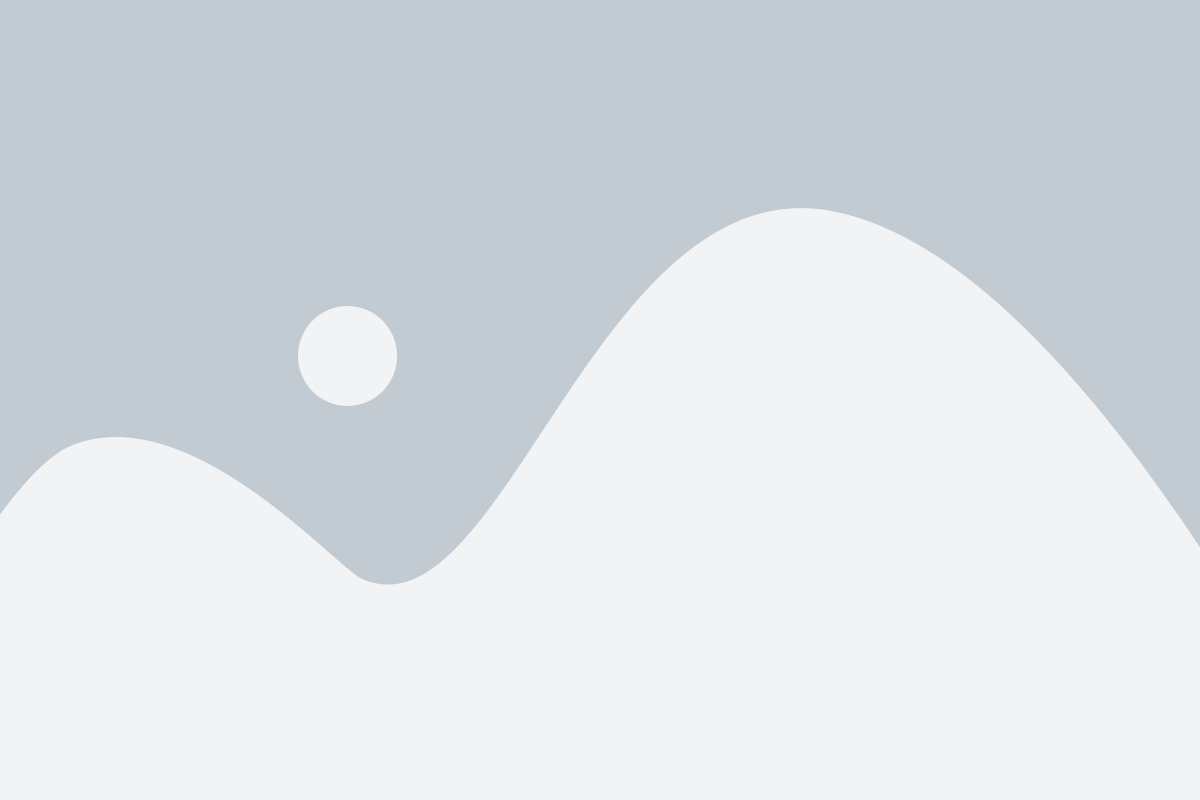
Robotic case packaging line
Lorem ipsum dolor sit amet, consectetur adipiscing elit. Ut elit tellus, luctus nec ullamcorper mattis, pulvinar dapibus leo.
FAQ
Listed below are the types of technical questions you may have about XINTU Robotic Case Packer
Working Principles of XINTU Robotic Case Packer
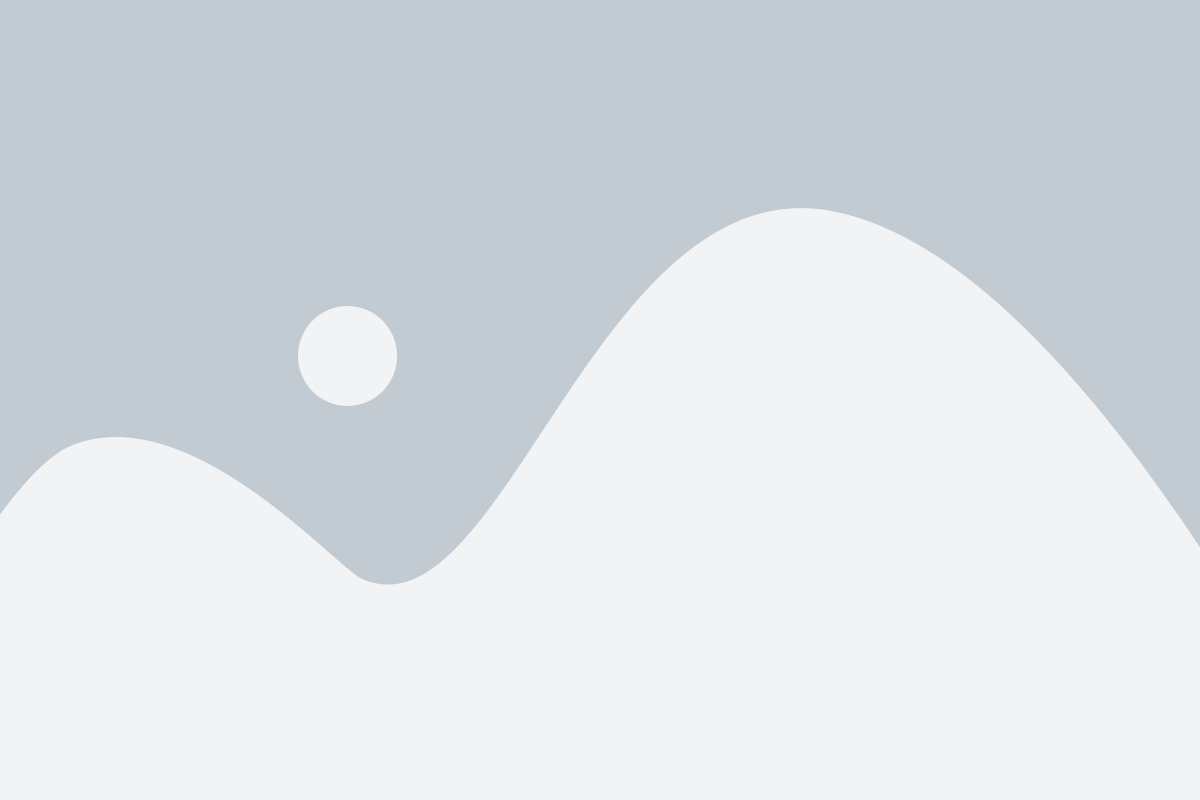
The XINTU Robotic Case Packer is a sophisticated automated packaging machine designed to streamline the end-of-line packaging process. Here’s how it works:
Robotic Packaging Machine Operation:
- Product Infeed: Products are fed into the system via a conveyor belt.
- Vision System: An integrated vision system identifies, sorts, and aligns products for precise packing.
- Robotic Arm Movement: The industrial robot packer, equipped with advanced motion control, picks products using specialized end effectors designed for various shapes and sizes.
- Case Formation: Cases are automatically formed and positioned in the loading area.
- High-Speed Packing: The high-speed robotic packer places products into cases with remarkable accuracy and speed.
- Case Sealing: Once filled, cases are sealed and prepared for palletizing or shipment.
The XINTU Robotic Case Packer ensures efficiency and consistency, making it an essential component of any modern packaging line. This flexible case packer can be adapted to handle a wide range of products, from bottles and cans to irregularly shaped items, providing a robust and reliable solution for your packaging needs.
Maintenance of Your XINTU Robotic Case Packer
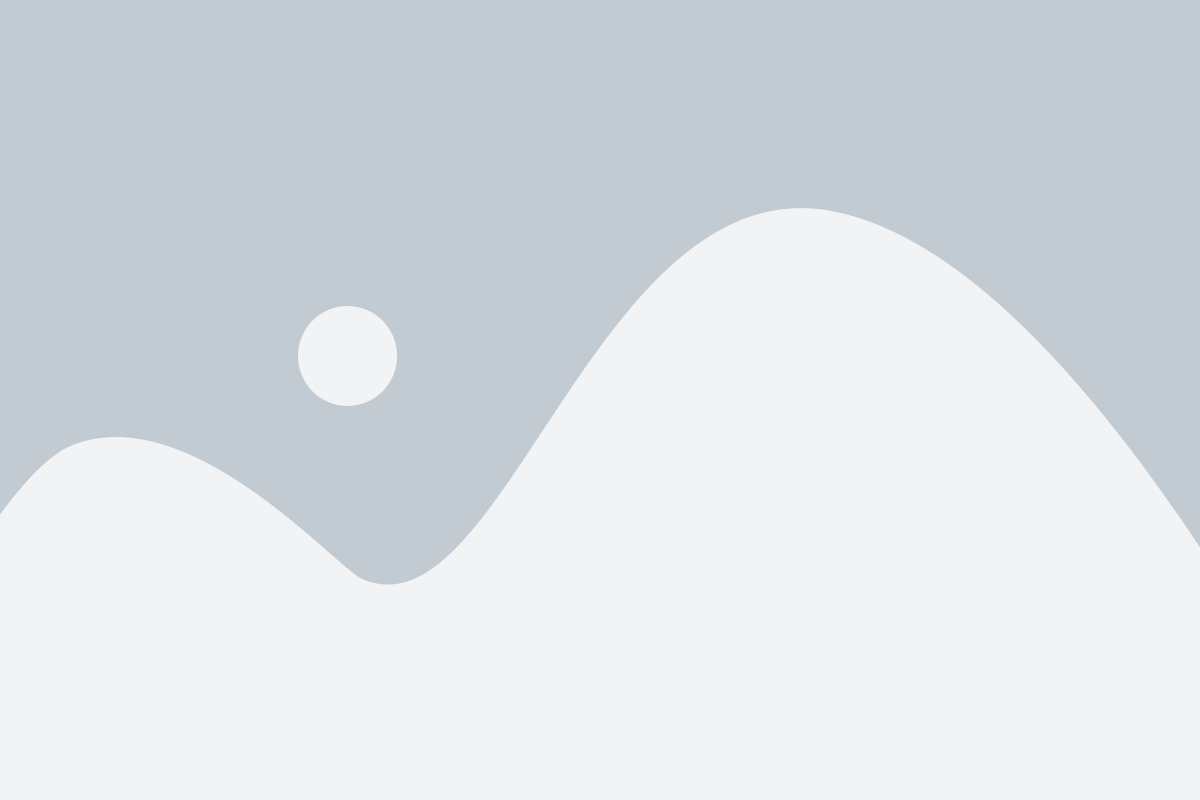
Maintaining your XINTU Robotic Case Packer ensures its longevity and optimal performance. Here are the key steps and considerations for effective maintenance:
Routine Inspection:
- Daily Checks: Inspect the robotic packaging machine for any visible wear and tear. Ensure all moving parts are lubricated and functioning smoothly.
- Weekly Maintenance: Clean the robot case packer and surrounding areas to prevent dust and debris buildup. Check for any loose bolts or connections.
- Monthly Inspection: Conduct a thorough inspection of the automated case packer’s electrical systems and sensors to ensure they are operating correctly.
Preventive Maintenance:
- Scheduled Servicing: Follow the manufacturer’s recommended service schedule. This typically includes detailed inspections and servicing by trained technicians.
- Component Replacement: Replace worn-out parts as per the maintenance schedule to prevent unexpected breakdowns. Keep a stock of essential spare parts.
- Software Updates: Regularly update the software of the robotic packaging machine to benefit from the latest features and improvements.
Common Maintenance Tasks:
- Lubrication: Regularly lubricate moving parts to reduce friction and wear.
- Calibration: Periodically calibrate the robotic arms and sensors to maintain precision in packing operations.
- Cleaning: Clean the machine, especially the end effectors, to prevent contamination and ensure hygienic packaging.
Safety Precautions:
- Power Down: Always power down the automatic case packer before performing any maintenance tasks to prevent accidents.
- Use Protective Gear: Wear appropriate protective gear, such as gloves and safety glasses, during maintenance.
By adhering to these maintenance practices, you can ensure the high-speed robotic packer continues to operate efficiently and effectively, minimizing downtime and maximizing productivity.
The XINTU Robotic Case Packer integrates advanced technologies to enhance efficiency, precision, and reliability in packaging operations. Below are the key technological features of the XINTU Robotic Case Packer:
Robotic Integration:
- Automated Case Packer: Utilizes state-of-the-art robotics to automate the case packing process, minimizing human intervention and maximizing productivity.
- High-Speed Robotic Packer: Capable of operating at high speeds to meet demanding production schedules without compromising accuracy.
Advanced Motion Control:
- Robotic Packaging Machine: Features sophisticated motion control systems that ensure smooth and precise movements of the robotic arms, enabling accurate product placement.
- Flexible Case Packer: Designed to handle various product sizes and shapes with minimal adjustments, providing flexibility in packaging different items.
Vision Systems:
- Robotic Case Packing System: Equipped with advanced vision systems to detect and identify products, ensuring correct orientation and placement within the case.
- Delta Pick and Place Case Packer: Uses vision-guided technology for precise pick-and-place operations, enhancing the efficiency of the packing process.
User-Friendly Interface:
- Automated Delta Robot Packer: Includes a user-friendly interface that allows operators to easily control and monitor the packing process, reducing the learning curve and improving operational efficiency.
- End-of-Line Packaging Robot: Provides real-time data and diagnostics, helping operators quickly identify and resolve issues.
Safety Features:
- Industrial Robot Packer: Incorporates multiple safety features, such as emergency stop buttons, safety light curtains, and interlock systems, to ensure the safety of operators and equipment.
- Robotic Carton Packer: Designed with robust safety protocols to prevent accidents and protect personnel working around the machine.
Efficiency and Reliability:
- Automatic Case Packer: Engineered for high reliability with minimal downtime, ensuring consistent performance even in demanding production environments.
- Delta Case Packing System: Optimized for energy efficiency, reducing operational costs while maintaining high throughput.
The XINTU Robotic Case Packer's cutting-edge technology provides a comprehensive solution for end-of-line packaging needs, enhancing overall production efficiency and product handling.
Installation Process:
Pre-Installation Preparation:
- Site Assessment: Evaluate the installation site to ensure adequate space, proper flooring, and necessary utilities (power, compressed air).
- Safety Measures: Implement safety protocols to ensure a secure installation process for personnel and equipment.
Unpacking and Inspection:
- Unpacking Equipment: Carefully unpack the robotic case packer and all its components. Inspect for any damage that may have occurred during shipping.
- Component Verification: Verify that all components listed in the packing list are present and undamaged.
Positioning the Equipment:
- Placement: Position the robotic case packer in the designated area. Ensure it is level and properly aligned with existing production lines.
- Anchoring: Secure the machine to the floor using appropriate anchoring methods to prevent movement during operation.
Electrical and Pneumatic Connections:
- Power Supply: Connect the automated case packer to the electrical power supply as specified in the installation manual.
- Air Supply: Connect the pneumatic systems to the compressed air supply, ensuring adequate pressure and flow rate.
System Integration:
- Connectivity: Integrate the robotic packaging machine with the existing production line and auxiliary equipment, such as conveyors and sensors.
- Programming: Upload and configure the necessary software programs for the robot case packer. This includes setting up parameters for different products and packaging requirements.
Testing and Calibration:
- Initial Testing: Perform initial testing to ensure all systems are functioning correctly. Check for proper movement, sensor readings, and communication between components.
- Calibration: Calibrate the robotic arms and other moving parts for precise operation. Ensure the machine operates within the specified tolerances.
Training and Handover:
- Operator Training: Provide comprehensive training for operators and maintenance personnel. Cover operational procedures, safety protocols, and troubleshooting methods.
- Documentation: Hand over all relevant documentation, including user manuals, maintenance guides, and warranty information.
Benefits of Professional Installation:
- Ensures optimal performance and longevity of the high-speed robotic packer.
- Minimizes downtime and potential issues during the startup phase.
- Provides a seamless integration with your existing end-of-line packaging robot system.
By following these steps, you can ensure a smooth and efficient installation of your XINTU Robotic Case Packer, maximizing its potential in your production environment.
Yes, the XINTU Robotic Case Packaging Machine is designed to handle a wide variety of product sizes and shapes with high efficiency and precision. Here’s how it achieves this versatility:
Flexible Case Packer Design:
- The machine is engineered to accommodate various product dimensions and configurations, making it suitable for diverse packaging needs.
Advanced Robotics:
- Equipped with sophisticated robotic arms, the machine can adapt to different product sizes and shapes without requiring extensive manual adjustments.
Automated Case Packer:
- Automated adjustments ensure that the machine can quickly switch between different product types, maintaining high productivity levels.
Vision-Guided Technology:
- Integrated vision systems allow the robot to identify and handle products of various shapes and sizes accurately, ensuring consistent packing quality.
Adjustable Components:
- The machine features adjustable components that can be easily modified to fit different products, providing flexibility in packaging operations.
High-Speed Robotic Packer:
- Capable of operating at high speeds, the machine can efficiently manage the packaging of products with varying sizes and shapes, ensuring optimal throughput.
The XINTU Robotic Case Packing Machine offers several advanced features designed to enhance efficiency, flexibility, and reliability in packaging operations. Here are the main features:
High-Speed Robotic Packer:
- Capable of operating at high speeds, this machine ensures fast and efficient packing processes, significantly increasing productivity.
Flexible Case Packer Design:
- The machine is designed to handle various product sizes and shapes, making it adaptable to different packaging requirements and applications.
Automated Case Packer:
- Featuring full automation, the XINTU Robotic Case Packing Machine minimizes manual intervention, reducing labor costs and increasing operational efficiency.
Advanced Vision Systems:
- Equipped with integrated vision systems, the machine can accurately identify and handle products, ensuring consistent and precise packing.
User-Friendly Interface:
- The machine comes with an intuitive user interface, making it easy to operate and maintain, even for operators with minimal training.
End-of-Line Packaging Robot:
- As an end-of-line solution, this robotic case packer integrates seamlessly into existing production lines, enhancing overall workflow and efficiency.
These features make the XINTU Robotic Case Packing Machine a versatile and powerful solution for various packaging needs, providing reliability and efficiency in diverse industrial applications.
Ensuring consistent packing with the XINTU Robotic Case Packing Machine involves several key features and technologies that maintain high accuracy and reliability in the packing process. Here’s how XINTU achieves this:
Advanced Vision Systems:
- Integrated vision systems detect and align products accurately before packing, ensuring each item is correctly oriented and positioned.
High-Speed Robotic Packer:
- The high-speed operation maintains a steady flow of products, reducing bottlenecks and ensuring consistent packing rates.
Precision Robotics:
- The robot arms are equipped with precision control, allowing for delicate handling of products to prevent damage and ensure consistent placement within the cases.
Automated Case Packer Technology:
- Automation reduces human error, ensuring that each case is packed uniformly according to preset configurations.
Real-Time Monitoring:
- The system continuously monitors packing processes and makes real-time adjustments to correct any deviations, ensuring consistent output quality.
User-Friendly Interface:
- An intuitive interface allows operators to easily set up and adjust parameters, ensuring the machine operates consistently at optimal settings.
These features ensure that the XINTU Robotic Case Packing Machine delivers consistent and reliable packing performance across various applications, enhancing productivity and product integrity.
Integrating the XINTU Robotic Case Packing Machine into an existing production line is designed to be seamless and efficient, ensuring minimal disruption and maximum compatibility. Here’s how you can achieve this:
Modular Design:
- The XINTU Robotic Case Packing Machine features a modular design, making it easy to fit into various production line configurations without extensive modifications.
Customizable Interface:
- Equipped with a customizable interface, the machine can be programmed to synchronize with your current production line’s operational parameters and control systems, ensuring smooth integration.
Communication Protocols:
- The machine supports multiple communication protocols, such as Ethernet/IP, Modbus, and OPC UA, facilitating easy communication with existing equipment and systems.
Flexible Layout:
- The flexible layout options allow the machine to be positioned at different points in the production line, accommodating space constraints and optimizing workflow efficiency.
Automated Case Packer Technology:
- Advanced automated case packer technology ensures that the machine can handle various product sizes and shapes, integrating seamlessly with the products processed on your existing line.
Integration Support:
- XINTU provides comprehensive integration support, including on-site assessments, customization, and installation services, ensuring that the robotic case packer fits perfectly within your production line.
By leveraging these features, the XINTU Robotic Case Packing Machine can be smoothly integrated into your existing production line, enhancing productivity and efficiency without causing major disruptions.
The energy requirements for operating the XINTU Robotic Case Packaging Machine are designed to ensure optimal performance while maintaining energy efficiency. Here are the key details:
Power Supply:
- The machine operates on a three-phase 380V 50Hz/60Hz power supply, which is standard for industrial equipment, ensuring it can be easily integrated into most production facilities.
Power Consumption:
- The total power consumption of the machine is approximately 4 kW. This includes the power required to operate the robotic arm, conveyor systems, and other auxiliary equipment.
Air Supply:
- The machine requires a compressed air supply with a pressure range of 6-7 kg/cm². The air consumption is typically around 460 L/min, which supports the pneumatic components of the machine.
Energy Efficiency:
- The XINTU Robotic Case Packaging Machine is designed with energy-efficient components to minimize power usage and reduce operational costs while maintaining high performance.
Integrated Systems:
- The machine’s control systems, including the PLC and touch screen, are optimized for low energy consumption, contributing to overall energy efficiency.
By understanding and meeting these energy requirements, you can ensure the XINTU Robotic Case Packaging Machine operates efficiently within your production line.
The XINTU Robotic Case Packer is equipped with several advanced safety features to ensure safe and efficient operation. Here are the key safety features:
Safety Sensors:
- The machine is fitted with multiple safety sensors that detect any obstructions or abnormalities in the operating area, ensuring immediate shutdown to prevent accidents.
Emergency Stop Buttons:
- Emergency stop buttons are strategically placed around the machine to allow operators to quickly halt operations in case of an emergency, providing an extra layer of safety.
Safety Guards and Fences:
- The machine is enclosed with safety guards and fences to protect operators from moving parts. These barriers prevent accidental contact with the robotic arm and other moving components.
Interlock Systems:
- The interlock systems ensure that the machine cannot operate unless all safety guards are in place and properly secured, preventing accidental startups during maintenance or adjustments.
Light Curtains:
- Light curtains are installed to create an invisible barrier around the machine. If this barrier is breached, the machine stops immediately, ensuring operator safety.
Visual and Audible Alarms:
- The machine is equipped with visual and audible alarms that activate in case of a malfunction or safety breach, alerting operators to take necessary actions promptly.
By incorporating these safety features, the XINTU Robotic Case Packer ensures a safe working environment, reducing the risk of accidents and enhancing overall operational safety.
Choosing the right robotic case packaging machine involves evaluating several critical factors to ensure it meets your specific packaging needs. Here’s a guide to help you make an informed decision:
Product Types and Sizes:
- Evaluate the variety of products you need to pack, including their shapes, sizes, and weights. Ensure the machine can handle the range of products in your production line.
Packaging Speed:
- Determine the required packaging speed. High-speed robotic case packers can handle more products per minute, but ensure the speed aligns with your production needs to avoid bottlenecks.
Integration Capabilities:
- Check how well the robotic case packer can integrate with your existing production line. It should seamlessly connect with other machines like conveyors, fillers, and palletizers.
Flexibility:
- Choose a machine that offers flexibility for future changes. A flexible case packer can adapt to new products or packaging formats without significant modifications.
Automation Level:
- Decide on the level of automation you need. Automated case packers reduce manual labor, improve efficiency, and enhance consistency in packing.
Footprint and Space:
- Consider the physical space available in your facility. Ensure the machine fits within the allocated space without causing congestion or workflow disruptions.
Maintenance and Support:
- Opt for a machine that offers easy maintenance and has reliable technical support. This minimizes downtime and ensures smooth operations.
Budget:
- Balance the cost of the machine with its features and benefits. A higher upfront cost may be justified by long-term savings and efficiency gains.
By considering these factors, you can select a robotic case packaging machine that optimizes your packaging operations and meets your production goals.
There are several types of robotic case packers available in the market, each designed to cater to different packaging needs and product types. Here are the main types:
Delta Robot Case Packer:
- Ideal for high-speed pick and place applications. It offers precise and rapid handling of lightweight items.
Articulated Robot Case Packer:
- Features a multi-axis arm that provides flexibility and precision. Suitable for a wide range of products and packaging configurations.
SCARA Robot Case Packer:
- Known for its speed and precision, typically used for tasks requiring rapid and repetitive motion within a confined workspace.
Collaborative Robot Case Packer:
- Designed to work alongside human operators, enhancing productivity and safety. Suitable for smaller, flexible packaging lines.
Cartesian Robot Case Packer:
- Operates on linear axes, ideal for simple pick and place operations with high precision.
Palletizing Robot Case Packer:
- Specializes in stacking and organizing products on pallets, suitable for end-of-line packaging solutions.
Hybrid Robot Case Packer:
- Combines the features of multiple types of robots to handle complex packaging tasks.
Using XINTU Robotic Case Packers offers several efficiency benefits, enhancing productivity and operational performance. Here are the key benefits:
High-Speed Operations:
- XINTU Robotic Case Packers can achieve speeds of up to 40 cases per minute, significantly increasing throughput.
Precision and Accuracy:
- Advanced vision systems and robotic arms ensure precise product handling and placement, reducing errors and waste.
Reduced Labor Costs:
- Automation minimizes the need for manual labor, lowering labor costs and mitigating the risk of human error.
Flexibility and Adaptability:
- These packers can handle a wide variety of product sizes and shapes, making them suitable for diverse packaging needs.
Consistent Performance:
- Robotic systems provide consistent performance, ensuring uniformity in packaging and improving overall product quality.
Space-Saving Design:
- Compact and efficient designs allow for integration into existing production lines without requiring significant floor space.
The production capacity of XINTU Robotic Case Packers varies depending on the specific model and its configuration. Here are the capacities for different models:
XINTU-RCP10:
- Capacity: Up to 10 cases per minute.
- Application: Suitable for small to medium-sized operations, ideal for food and beverage industries.
XINTU-RCP20:
- Capacity: Up to 20 cases per minute.
- Application: Designed for medium to large operations, commonly used in pharmaceuticals and cosmetics industries.
XINTU-RCP40:
- Capacity: Up to 40 cases per minute.
- Application: Optimal for high-speed operations, perfect for large-scale production in various industries including chemicals and consumer goods.
XINTU-RCP60:
- Capacity: Up to 60 cases per minute.
- Application: Best for ultra-high-speed requirements, suitable for large manufacturers with extensive production needs.
These capacities ensure that XINTU Robotic Case Packers can meet the diverse production demands of different industries, from small batch productions to large-scale, high-speed operations.
Optimizing the efficiency of your XINTU Robotic Case Packer involves several key strategies:
Regular Maintenance:
- Routine Checks: Ensure all components are inspected regularly to prevent wear and tear.
- Lubrication: Keep moving parts well-lubricated to reduce friction and extend the lifespan of the machine.
Proper Training:
- Staff Training: Train your operators thoroughly on the machine's functionality to minimize errors and maximize productivity.
- Safety Protocols: Implement and adhere to safety protocols to prevent accidents and reduce downtime.
Automation Integration:
- Seamless Integration: Integrate the Robotic Case Packer with your existing production line for smoother operations.
- Automation Software: Utilize advanced automation software to streamline processes and enhance coordination between different machines.
Regular Upgrades:
- Software Updates: Keep the machine's software up-to-date to take advantage of new features and improvements.
- Hardware Upgrades: Upgrade hardware components as necessary to improve performance and efficiency.
Optimal Settings:
- Speed Adjustments: Set the machine to optimal speeds for different products to ensure consistent packing without causing damage.
- Configuration Settings: Adjust configuration settings based on product sizes and shapes for better alignment and packing.
Monitor Performance:
- Performance Metrics: Regularly monitor performance metrics such as speed, accuracy, and downtime.
- Data Analysis: Analyze the collected data to identify areas for improvement and implement necessary changes.
1. Inconsistent Packing Quality:
- Issue: The packed cases are not uniform or products are misplaced.
- Troubleshooting:
- Check Calibration: Ensure the machine is calibrated correctly for the specific product sizes and shapes.
- Inspect Sensors: Clean and check sensors for proper alignment and functionality.
- Adjust Speed: Fine-tune the operating speed to match the product requirements.
2. Frequent Downtime:
- Issue: The machine experiences frequent stops and starts.
- Troubleshooting:
- Maintenance Schedule: Follow a strict maintenance schedule to prevent wear and tear.
- Software Updates: Keep the machine’s software updated to avoid bugs and improve efficiency.
- Component Checks: Regularly inspect and replace worn-out components.
3. Mechanical Jams:
- Issue: The machine gets jammed during operation.
- Troubleshooting:
- Clear Obstructions: Remove any foreign objects or product debris that may be causing the jam.
- Alignment: Ensure all parts are properly aligned and moving smoothly.
- Lubrication: Apply proper lubrication to reduce friction and prevent jams.
4. Sensor Malfunctions:
- Issue: Sensors fail to detect products or cases correctly.
- Troubleshooting:
- Clean Sensors: Keep sensors clean from dust and debris.
- Check Connections: Ensure all sensor connections are secure and undamaged.
- Calibration: Recalibrate sensors to maintain accurate detection.
5. Power Supply Issues:
- Issue: The machine experiences power fluctuations or interruptions.
- Troubleshooting:
- Stable Power Source: Ensure a stable and uninterrupted power supply.
- Inspect Wiring: Check all electrical connections and wiring for any signs of damage or wear.
- Voltage Regulation: Use voltage regulators to maintain consistent power levels.
1. Comprehensive Training Program:
- Overview: Implement a structured training program that covers all aspects of operating the Robotic Case Packer.
- Content: Include theoretical lessons, practical sessions, and safety protocols.
- Duration: Ensure the program is thorough and spans several days or weeks, depending on complexity.
2. Hands-On Practice:
- Simulation Training: Use simulation tools to let staff practice in a controlled environment.
- Real-World Scenarios: Provide real-world scenarios for hands-on experience under supervision.
- Step-by-Step Guidance: Offer step-by-step guidance during initial operations to build confidence and competence.
3. Safety Protocols:
- Emergency Procedures: Train staff on emergency stop procedures and safety protocols.
- Protective Gear: Ensure the use of appropriate personal protective equipment (PPE) such as gloves, safety glasses, and helmets.
- Hazard Awareness: Educate staff on potential hazards and how to avoid them.
4. Regular Assessments:
- Skill Evaluation: Conduct regular assessments to evaluate staff competency and understanding.
- Feedback Sessions: Provide feedback sessions to address any gaps in knowledge and improve skills.
- Certification: Consider certifying staff upon successful completion of training and assessments.
5. Continuous Learning:
- Refresher Courses: Offer periodic refresher courses to keep staff updated on new technologies and procedures.
- Advanced Training: Provide advanced training for experienced operators to enhance their skills and knowledge.
- Learning Resources: Make available resources such as manuals, video tutorials, and online courses for continuous learning.
1. Advanced Vision Systems:
- Improved Accuracy: Modern Robotic Case Packers now feature advanced vision systems that enhance accuracy and efficiency.
- Functionality: These systems enable the robots to identify and handle various product shapes and sizes with precision.
- Automation: Automated vision inspection ensures products are correctly oriented and placed, reducing errors.
2. Enhanced Flexibility:
- Adaptability: New advancements in robotic technology allow for greater flexibility in handling different types of packaging.
- Modular Design: The modular design enables easy upgrades and customization based on specific needs.
- Quick Changeovers: Enhanced mechanisms facilitate faster and more efficient changeovers between product runs.
3. Integration with IoT and AI:
- Smart Manufacturing: Integration with the Internet of Things (IoT) and Artificial Intelligence (AI) has revolutionized robotic case packing.
- Real-Time Data: IoT connectivity provides real-time data monitoring and predictive maintenance, improving uptime.
- AI Algorithms: AI algorithms optimize packing patterns and improve overall system efficiency.
4. High-Speed Capabilities:
- Increased Speed: Latest Robotic Case Packers offer high-speed capabilities, significantly boosting production rates.
- Efficiency: High-speed robotic arms and conveyors ensure rapid and consistent case packing.
- Precision: Despite the increased speed, these machines maintain high precision and quality standards.
5. Energy Efficiency:
- Reduced Power Consumption: New technologies focus on reducing energy consumption, making the machines more eco-friendly.
- Sustainable Operations: Energy-efficient motors and smart power management systems contribute to sustainable manufacturing processes.
- Cost Savings: Lower energy usage translates into cost savings for manufacturers.
6. User-Friendly Interfaces:
- Intuitive Control Panels: Modern Robotic Case Packers feature user-friendly control panels with intuitive interfaces.
- Ease of Use: Simplified programming and operation reduce the learning curve for operators.
- Remote Access: Advanced interfaces allow for remote monitoring and control, increasing operational flexibility.